The quality – Manfrotto Triflector MKII Frame + Silver/White Panels User Manual
Page 3
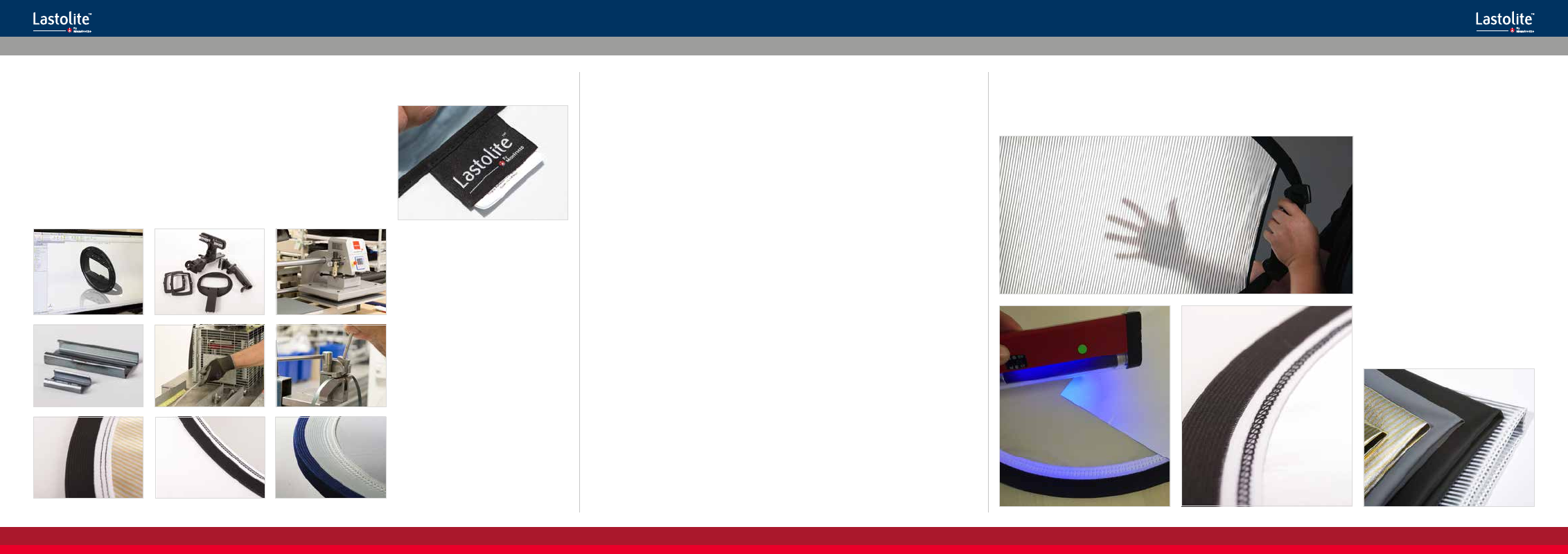
4
5
The Quality
At Lastolite By Manfrotto we not only make a range of innovative accessories to help photographers
and film-makers shoot great imagery, but we also take pride in offering world-class products
manufactured to the highest standards, ensuring they can withstand the repeated daily use of the
most demanding image-maker.
To keep our leading edge, we make significant investments into research and development to
ensure that we can continue to launch new and innovative products to meet the needs of the
ever-changing photo and video markets. Allied to our strict quality standards and attention to detail,
we are always looking at ways to improve the way our products are manufactured, too. We are
consistently developing new ideas and technology, which leads to investment in bespoke tooling
and mouldings. With the vast majority of our fabric-based products made in our huge Leicestershire
factory, we retain close control over quality.
High quality sprung steel is used inside all of our
collapsible products. The steel is ‘dressed’ to
ensure all the sharp edges and dirt are removed
so no damage is incurred during use and provides
maximum longevity. To join the ends of the steel
together we use a range of specially designed,
heat treated clips that guarantee a permanently
strong fix for the lifetime of the product. For added
peace of mind we offer a lifetime warranty on the
steel rim in all of our products.
The steel rim is incorporated into our products by
inserting it into our specially designed rim tape.
The rim tape is made from a hard wearing, woven
elasticated construction designed to withstand the
typical knocks and scrapes from daily use by a
busy Imagemaker. The thick woven construction
prevents the steel from wearing through and
potentially weakening the structure of the product.
We apply the same level of detail and quality to all
of our textiles as well. Each fabric is manufactured
to meet the needs of the product, specifying
the construction of the weave and the type of
raw materials used. Each fabric is then coated
or processed depending on the technical
performance required.
The textiles are also tested to make sure they meet the correct performance levels over repeated use and in adverse conditions. We have developed
a range of over 10 different technical fabrics used to manufacture our products, including our patent protected innovative TriGrip Difflector fabric.
Our diffuser fabrics are manufactured using only
the finest whiteners to reduce any chance of
unwanted colourcast. The fabric is also specially
coated to ensure colour balance and a uniformed
spread of light as it is passed through the material,
avoiding typical issues such as irregular distribution
and hot spots.
Our reflective surfaces are also specifically
designed for our products and not general
purpose textiles. We incorporate the correct level
of stretch into the weave of all our fabrics to ensure
the foil surface remains intact and does not crack
under tension and lead to delamination. We also
use the highest quality adhesive and lamination
processes to ensure the foil remains bonded to
the textile throughout the products lifetime and
provides a uniformed opaque surface to bounce
the light.
And finally to hold our products together we use
a triple thread, twin needle, loop stitch which
provides maximum strength and durability.