Preventive maintenance - every twelve months – BUG-O Systems CWP-11 User Manual
Page 46
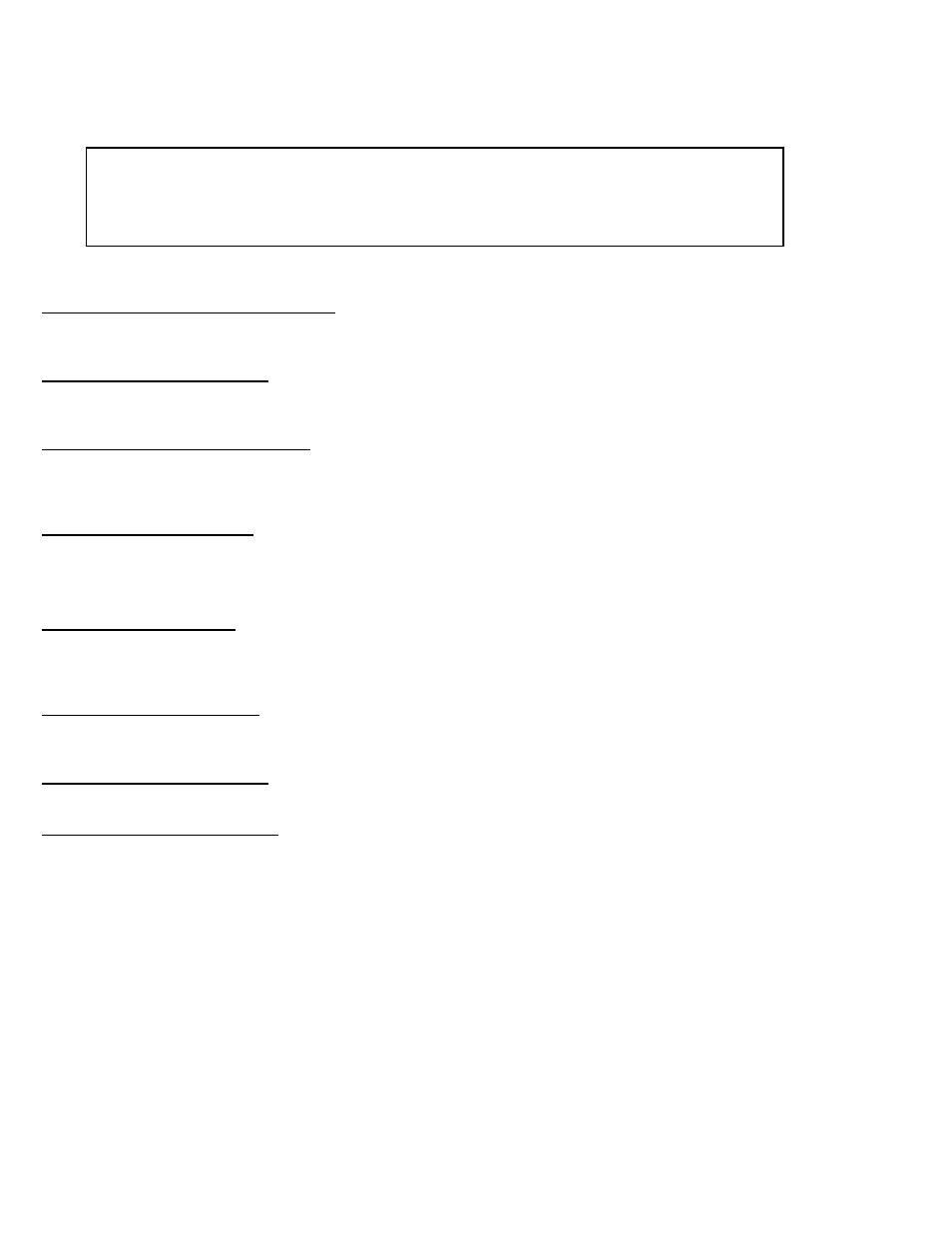
46
Refer to CWP-11 Exploded View. (Pg. 16)
1-1/2” Bearing With Fasteners Item #19:
Do not grease the bearing, it is greased for life by the manufacturer. If the grease fitting has not been removed and
plugged we suggest that you do so now. Earlier models may not have been plugged at time of assembly.
P.M. Motor Assembly Item #18:
Bodine gear motor lubrication. Fill gear motor to oil level indicator with worm gear oil conforming to AGMA#5EP
compounded oil (SAE#90) or Bodine lubricant (#L-23). Do not overfill.
LN-9 Wire Feeder Assembly Item #2:
Apply graphite grease to the gear teeth. Inspect the drive roll portion of the assembly, clean as necessary. Do not
use solvents on the idle roll because it may wash the lubricant out of the bearings. Do not apply grease to the drive
rolls.
Encoder Assembly Item #14:
Inspect for excessive wear. Keep the transmission assembly clean and lubricate with Lubriplate #630-AA.
Refer to CWP-11 Electrical Component Chart. (Pg. 31)
CWP-11 Collector Item #3:
The collector ring should be sanded once a year. If the collector ring is pitted badly it should be replaced. Inspect all
wires coming out of the collector ring for cut or missing insulation. All wires should be fastened to the center shaft
with a nylon cable tie. Tighten four set screws if needed.
Weld Cable Inlet 3/0 Item #10:
Ensure that the cable is fastened tightly to the collector ring. Inspect the cable for cut or missing insulation. Make
sure the micarta insulation tube on the cable is in good condition. Replace the cable if necessary.
Solenoid Adaptor Kit Item #15:
Inspect for damage. Replace if necessary.
LN-9 Control Cables #11, 12, 13:
Inspect the cable for cuts or missing insulation. Ensure that the elbow connector is not damaged. Ensure that all
terminal ends are snug. Replace cable if necessary.
PREVENTIVE MAINTENANCE - EVERY TWELVE MONTHS
IMPORTANT:
Make sure the input power at the power source is turned
off
and the 50' weld cable is
disconnected from the circle welder
prior to working inside the circle welder!