2 design of major parts – Flowserve MPT User Manual
Page 13
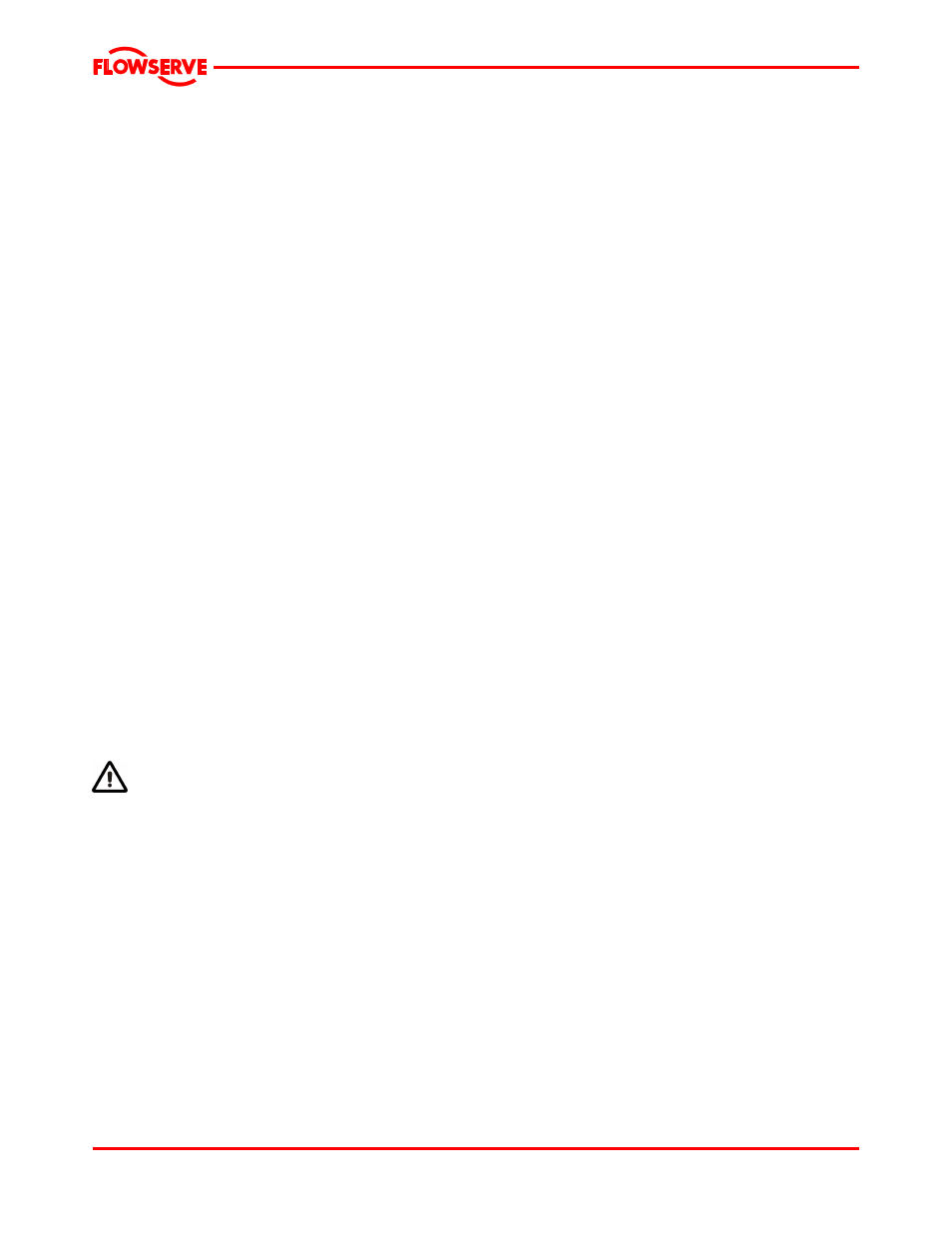
MPT USER INSTRUCTIONS ENGLISH 85392699 06-09
Page 13 of 41
®
3.2 Design of major parts
3.2.1 Pump casing
The volute type casing with integral priming
chamber is of rugged heavy duty construction for
minimum wear under the toughest operating
conditions. Removal of the casing is not required
when performing maintenance of the rotating element.
The pump is designed with radial o-ring seals allowing
the rotating element and cover plate to be easily
removed (back pull out).
3.2.2 Valve flap
The pump suction opening is fitted with a non-return
flap valve. The flap is a solid one-piece design and
is easily removed for cleaning or replacement.
3.2.3 Impeller
A fully balanced semi-open two vane impeller is
spigotted and screwed to the shaft. The back of the
impeller has integrally cast clearing vanes.
3.2.4 Wear plate
The casing is fitted with a reversible and renewable
steel front wear plate which is a close clearance
against the impeller vanes. If the wear plate
becomes excessively worn, it can be reversed to
present its unworn face to the impeller. The Model
80 wear plate is not reversible.
3.2.5 Cover Plate
A large cover plate below the suction facing retained
by two hand nuts is easily removed to access the
impeller and wear plate for fast cleanout of clogged
or tangled solids.
A PRESSURE RELIEF VALVE IS FITTED TO
THE COVER PLATE AND MUST NOT BE
REMOVED, PLUGGED OR MODIFIED.
3.2.6 Shaft
The shaft is of ample size to transmit the maximum
power required and to minimize deflection and
vibration even during intermittent stop-start
operation. Keys are used to transmit the torque. The
shaft drive end and keyway are in accordance with
ANSI B17.1.
3.2.7 Stuffing box (Seal housing)
The seal housing is positively located, sealed and
fastened to the bearing housing and forms an oil
chamber in which the seal runs fully immersed. The
oil cools and lubricates the seal faces and prevents
seal damage if the pump is run dry. The oil level is
monitored via the sight glass fitted high on the
bearing housing allowing the pump to be shut down
in the event of a seal failure – indicated by a sudden
drop in oil level or product showing in the oil. A vent
is also fitted at the top of the housing to maintain
even atmospheric pressure in the oil chamber.
The seal housing is easily replaceable if wear from
the impeller back sealing vanes becomes excessive.
3.2.8 Shaft seal
The stuffing box is fitted with a double mechanical
seal; the pump end has a hard faced balanced
rotary unit to prevent liquid and grit entering the seal
chamber. The outboard end separates the seal and
bearing oil chambers.
3.2.9 Bearing housing
The robustly designed bearing housing is rigidly
bolted and sealed to the pump casing. The housing
is fitted with oil breather/fillers and sight glasses to
indicate fill and low oil levels. The end cover is fitted
with a lip seal to exclude dirt and moisture. An
eyebolt is fitted to the housing for back pull-out
withdrawal.
3.2.10 Pump bearings and lubrication
The pump is fitted with two different types of ball
bearings. The thrust bearing is a double row angular
contact ball bearing, and the radial bearing a single
row deep groove ball bearing. The thrust bearing is
fitted at the outboard end in all pumps except the
MODEL 80, which has it fitted at the inboard end.
Both bearings run in a common oil bath and are
sized for a long service life.
3.2.11 Impeller adjustment
The bearing housing (back pull-out assembly) is
fastened to the casing with four locknuts; these
locknuts pass through four adjustable spacers in the
bearing housing flange. Accurate impeller setting is
affected by adjustment of these spacer and locking
with the locknuts.
The correct adjustment is 0.38/0.25 mm
(0.015/0.010 in.) clearance between impeller vanes
and wear plate.
Clearance between the impeller and seal housing is
fixed and does not need adjustment.
3.2.12 Driver
The driver is normally an electric motor. Different
drive configurations may be fitted such as an
internal combustion engine, turbines, hydraulic
motors, etc driving via couplings, belts, gearboxes,
drive shafts, etc.