Flowserve MPT User Manual
Page 17
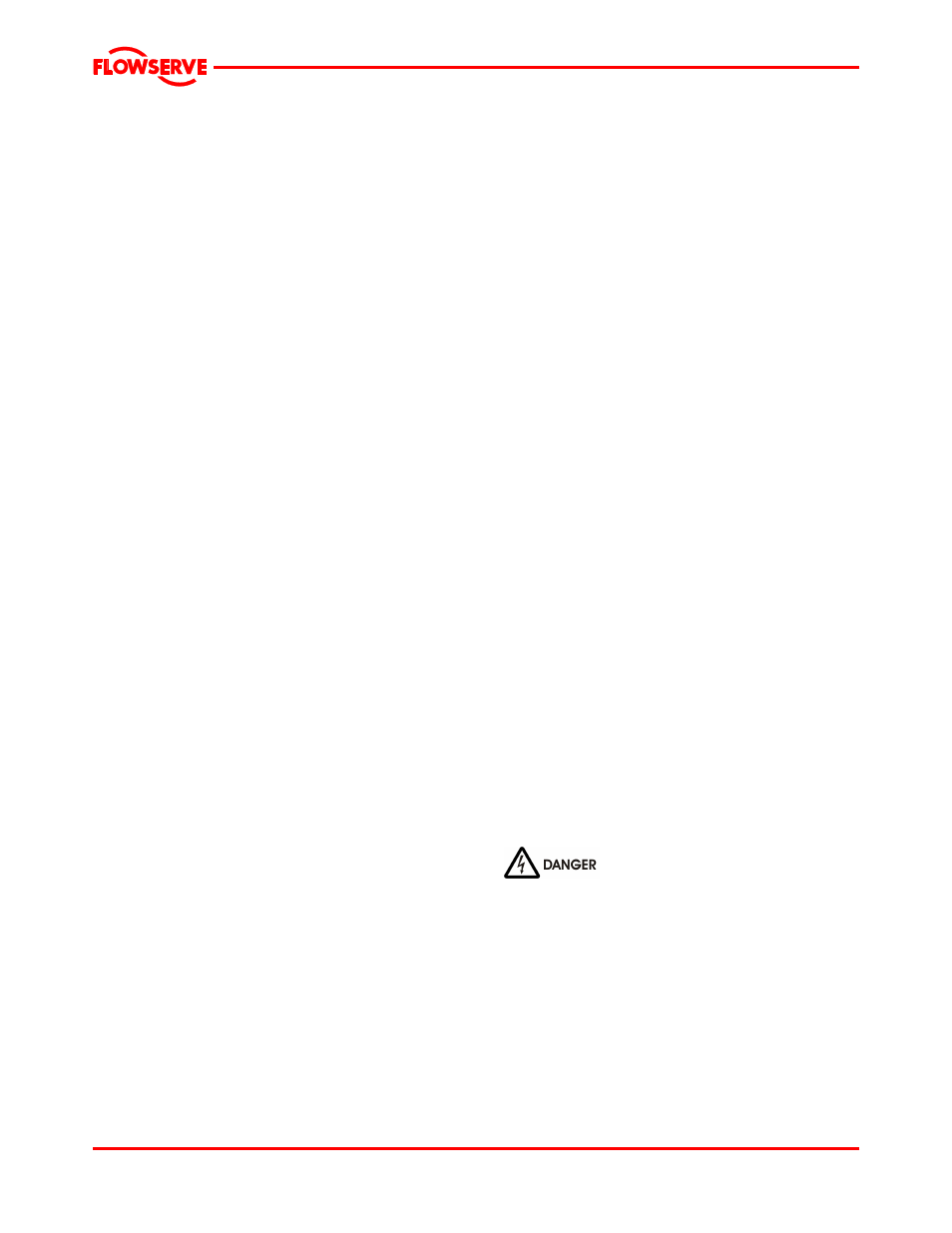
MPT USER INSTRUCTIONS ENGLISH 85392699 06-09
Page 17 of 41
®
4.4.2.5 Measure face gap
Face gaps may be measured between the
machined faces using feeler gauges, measuring
wedge, calipers, or suitable micrometer.
4.5 Piping
4.5.1 Protective covers
Protective covers are fitted to the pipe connections
to prevent foreign bodies entering during
transportation and installation. Ensure that these
covers are removed from the pump before
connecting any pipes.
4.5.2 Forces and moments on pump flanges
Maximum forces and moments allowed on the
pump flanges vary with the pump size and type and
are shown in section 3.3.3, Flange Loads. To
minimize these forces and moments that may
cause misalignment, hot bearings, worn couplings,
vibration, and the possible failure of the pump
casing, the following points should be strictly
followed:
•
Prevent excessive external pipe load
•
Never draw piping into place by applying force
to pump flange connections
•
Do not mount expansion joints so that their
force, due to internal pressure, acts on the
pump flange
4.5.3 Inlet pipe
The inlet pipe should be one or two sizes larger
than the pump inlet bore and pipe bends should be
as large a radius as possible. On suction lift the
piping should be inclined up towards the pump inlet
with long eccentric taper pipes incorporated to
prevent air locks. On positive suction, the inlet
piping must have a constant fall towards the pump.
4.5.4 Flow and pump suction
Flow should enter the pump suction with uniform
profile to minimize noise and wear. It is preferable
to have a straight length of suction pipe (approx. 8
to 10 times the pipe diameter) immediately
upstream of the suction nozzle and a straight
length of discharge pipe (approx. 5 to 8 times the
pipe diameter) immediately downstream of the
discharge nozzle.
Do not attach a short radius 90° bend directly on
the suction branch. A long radius suction bend may
be used as long as the bend is perpendicular to the
shaft center line of the unit. Do not install elbows at
an angle other than perpendicular to the shaft axis.
Elbows parallel to the shaft axis will cause uneven
flow into the impeller eyes.
Inlet strainers, when used, should have a net ‘free
area’ of at least three times the inlet pipe area and
a differential pressure device fitted to check for
blockage. Except in unusual circumstances,
strainers are not recommended in inlet piping. If
considerable foreign matter is expected, a screen
installed at the entrance to the wet well is
preferable.
4.5.5 Fitting valves and easy maintenance
Fitting an isolator and non-return valves can allow
easier maintenance. Never throttle pump on
suction side and never place a valve directly on the
pump inlet nozzle. If butterfly valves are used in the
suction line, the spindle must be parallel to the
pump shaft.
4.5.6 Piping and fittings should be flushed
before use.
4.5.7 Corrosive liquids
Piping for corrosive liquids should be arranged to
allow pump flushing before removal of a unit.
4.5.8 Air Release Valve
When a discharge check valve is applied an Air
Release Valve should be placed between the pump
discharge and the check valve. The Air Release
Valve’s function is to vent air from the pump during
the priming cycle. Flowserve Air Release Valves
are available.
4.6 Electrical Connections
4.6.1 Qualified electrician
Electrical connections should be
made by a qualified electrician in accordance with
the relevant local, national, and international
regulations.
It is important to be aware of the EUROPEAN
DIRECTIVE on electromagnetic compatibility when
wiring up and installing equipment on site. Attention
must be paid to ensure that the techniques used
during wiring/installation do not increase
electromagnetic emissions or decrease the
electromagnetic immunity of the equipment, wiring,
or any connected devices. If in any doubt, contact
Flowserve for advice.