Flowserve MPT User Manual
Page 21
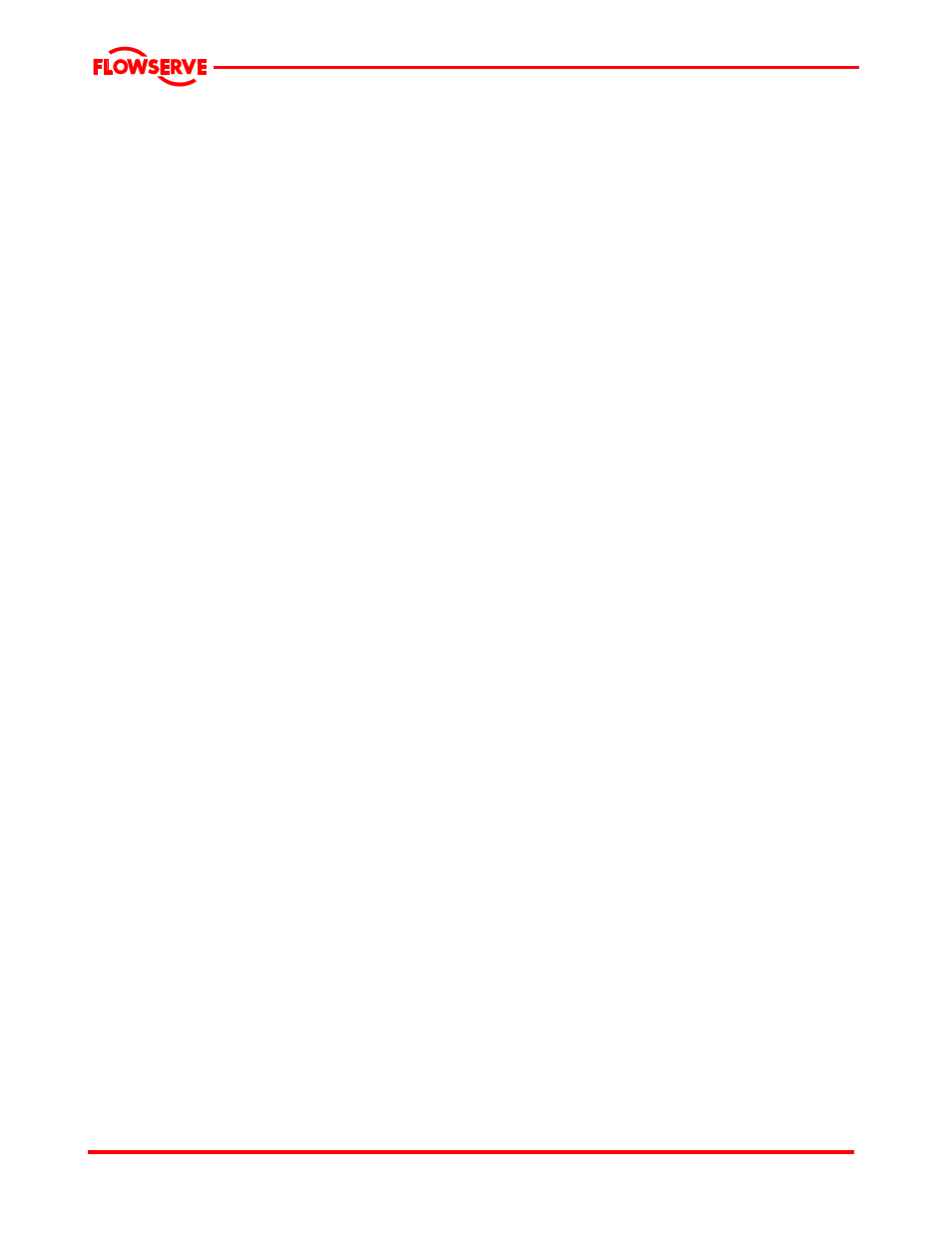
MPT USER INSTRUCTIONS ENGLISH 85392699 06-09
21 of 41
®
6.4.4 Part numbers and identification
Refer to section drawing for part numbers and
identification.
6.4.5 Replacing coupling parts
•
Isolate electric driver at circuit breaker
•
Disassemble and remove coupling guard
•
When standard Flex. Pin coupling is fitted, cut
worn rings from coupling pins, clean pins,
expand new rings onto pins, and reassemble
coupling
•
When other than standard coupling is fitted,
refer to the coupling manufacturer’s instructions
6.4.6 Complete disassembly
6.4.6.1 Rotating Element (Back pull-out
assembly)
•
Remove coupling guard and coupling spacer or
drive belts as applicable
•
Drain pump casing by removing vent plug
[6521] and drain plug [6515-0]. Remove any
auxiliary piping and equipment if applicable
•
Drain oil from seal chamber and bearing
housing by removing drain plugs [6515-1]
•
Remove bearing housing fastener nuts [6580-1]
and slinging housing from the eyebolt [1020]
provided; carefully lift the back pull-out
assembly clear of the casing and remove to
clean work area. Note that bearing housing is
sealed and located into casing with O-ring
[4610-0] and will have to be bumped free
6.4.6.2 Removal of Impeller
•
Remove impeller setscrew and washer [2913
and 2905-0]
•
Prevent shaft from rotating and unscrew
impeller from shaft (right hand thread)
6.4.6.3 Removal of Seal Housing and
Mechanical Seal
•
Remove socket setscrews [6579] and bump
seal chamber free from spigot location on
bearing housing. Take care not to damage
stationary face of inboard seal which is mounted
in housing bore
•
Back off seal drive screws and withdraw seal
assembly from shaft
6.4.6.4 Removal of Shaft and Bearings
•
Remove hexagon setscrews [6570-0] retaining
bearing cover [3260] and withdraw cover
complete with lip seal [4300]. Note gasket
between bearing housing and cover. Discard
gasket and lip seal and replace with new parts
on assembly
•
Press or drive shaft, complete with bearings,
from bearing housing in the direction of the
coupling end of the shaft
•
Remove the drive end bearing circlip [6544]
from the shaft. Note that the circlip is fitted to all
size pumps except the MODEL 80. Remove the
bearings from the shaft using a suitable bearing
puller applying pressure to the inner race only to
avoid damaging the bearings or shaft. Bearings
SHOULD NOT be refitted, but if it is intended to
reuse them, they should be wrapped in plastic
ready for washing and inspection
6.4.6.5 Removal of Wear Plate
Remove handnuts [6580-1] and withdraw
coverplate [1223-0]. Remove hexagon setscrews
[6570-1] and separate wear plate from cover. Note
on all pump sizes except the MODEL 80, the wear
plate is reversible.
6.4.6.6 Removal of Valve Flap
Remove nuts [6580-0] from suction flange studs on
all pump sizes except MODEL 80, which uses
hexagon setscrews [6570-5], and remove suction
flange complete with valve flap. Remove check
valve pin [6570-4] and withdraw flap.
6.5 Examination of parts
6.5.1 Used parts
Used parts must be inspected before assembly to
ensure the pump will subsequently run properly. In
particular, fault diagnosis is essential to enhance
pump and plant reliability.
6.5.2 Casing, impeller, wear plate, and seal
housing
Inspect for excessive wear, pitting, corrosion,
erosion, or damage and any sealing surface
irregularities. The wear plate on all pump sizes can
be re-machined to restore its wearing face and on
all sizes except the MODEL 80 can be reversed to
present an unworn face to the impeller. Replace as
necessary.
6.5.3 Shaft, keys, and impeller setscrew
Check shaft for straightness and any damage and
bearing lands for fit, the bearings should be a
maximum 0.013 mm (0.0005 in.) interference fit on
shaft. Check keys for damage and fit in keyways
and impeller setscrew for erosion damage.
6.5.4 Gaskets, O-rings, and lip seals
After dismantling, discard and replace.