Piping instructions, Performance testing of pumps – Flowserve Machinery Components User Manual
Page 12
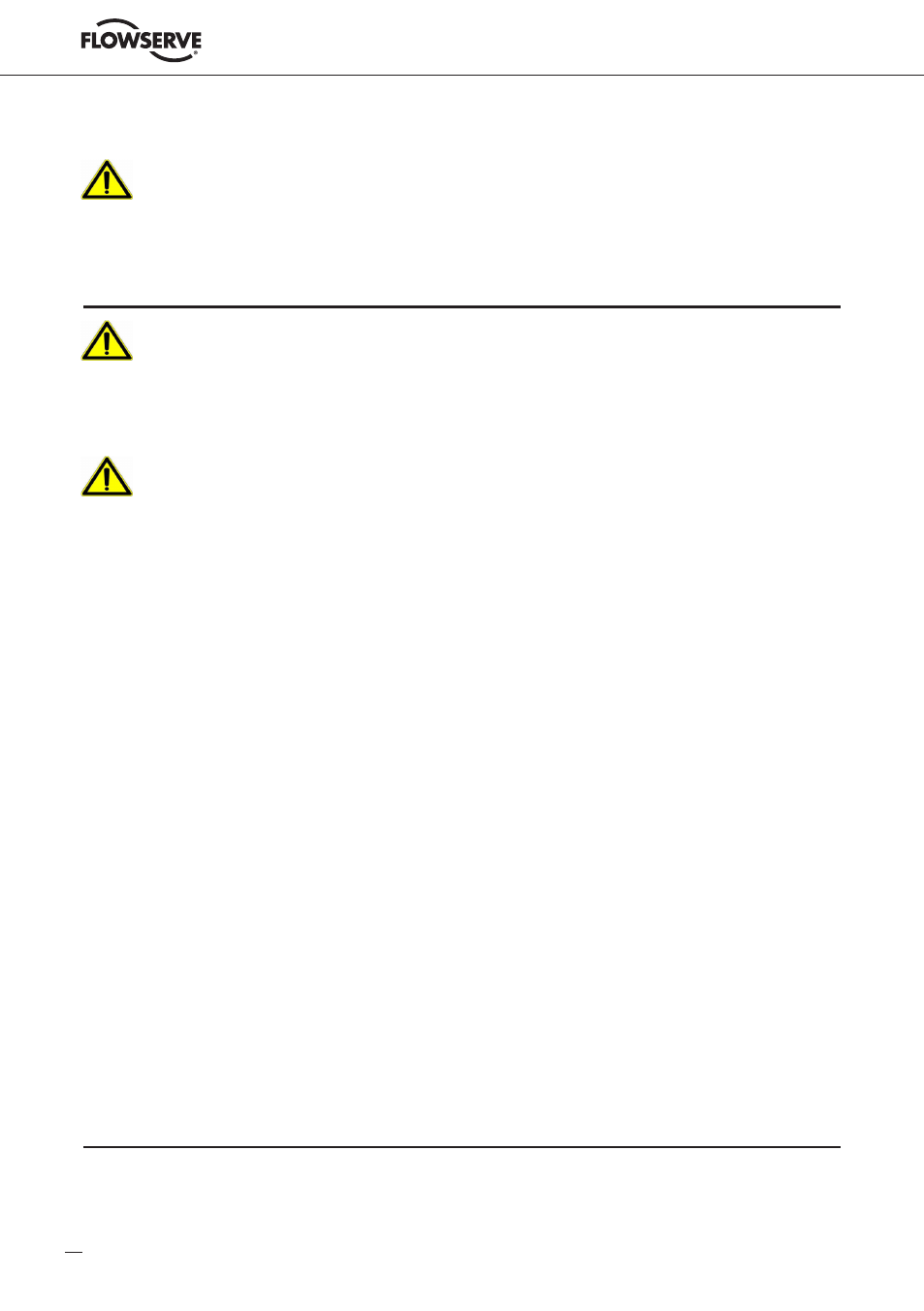
12
6.4.11 After bringing the unit up to operating conditions (pressure and temperature),
recheck pump to driver alignment. Make adjustments as necessary.
Parts of the mechanical seal that are moving during operation of the machine
(for example drive collar) have to be protected against contact with guards that
are in accordance with specifications of manufacturer from the machine.
7. Piping Instructions
Piping instructions are detailed on the mechanical seal assembly drawing.
These instructions must be followed precisely to ensure correct seal operation. Ensure that
piping is connected to the correct pipe ports to prevent unsafe situations.
For auxiliary systems: carefully read the maintenance instructions provided with the system.
The connections on the mechanical seal are properly marked.
Minimize restrictions, especially in closed loop piping arrangements.
Unless otherwise specified, the minimum internal diameter for pipe, tubing and connecting
hardware should be 12,7 mm (.500”).
Total pipe length and number of bends should be kept to a minimum.
Use smooth, large radius bends; do not use elbows, tees, etc. Orifices should be installed as
far away from the seal gland as possible. An exception to this rule should be made for orifices
fitted to drain piping. To avoid clogging of the orifice it is advisable to install it in the seal gland
so that the generated heat will serve to keep the leaked product fluid.
For “loop type” systems (API-plan 23, 52 and 53 A, B, C)
Pipe runs should be sloped continuously up or down to allow adequate circulation, proper
venting and draining. Make sure that the loop, including seal gland, does not include vapor
traps. Unless otherwise specified, reservoirs and coolers must be mounted 40 to 60 cm
(15” to 24”) above the seal inlet or outlet connection, whichever is the highest, to promote
thermosyphoning in standby condition.
Seals equipped with excess leakage detection
Excess leakage detection, often used with single or non-pressurized dual seals, is commonly
achieved by monitoring liquid level or pressure increases. With such an arrangement, the drain
line for normal leakage must slope downward continuously to the point of exit (e.g. sump).
Refer to the seal assembly drawing for additional piping requirements including the proper
location of the restriction orifice and instrumentation.
8. Performance Testing of Pumps
Pump manufacturers will often perform pump performance tests on water with the mechanical
seal installed. If the pump product used during field operation is not equal to water, seal designs