Flowserve Machinery Components User Manual
Page 14
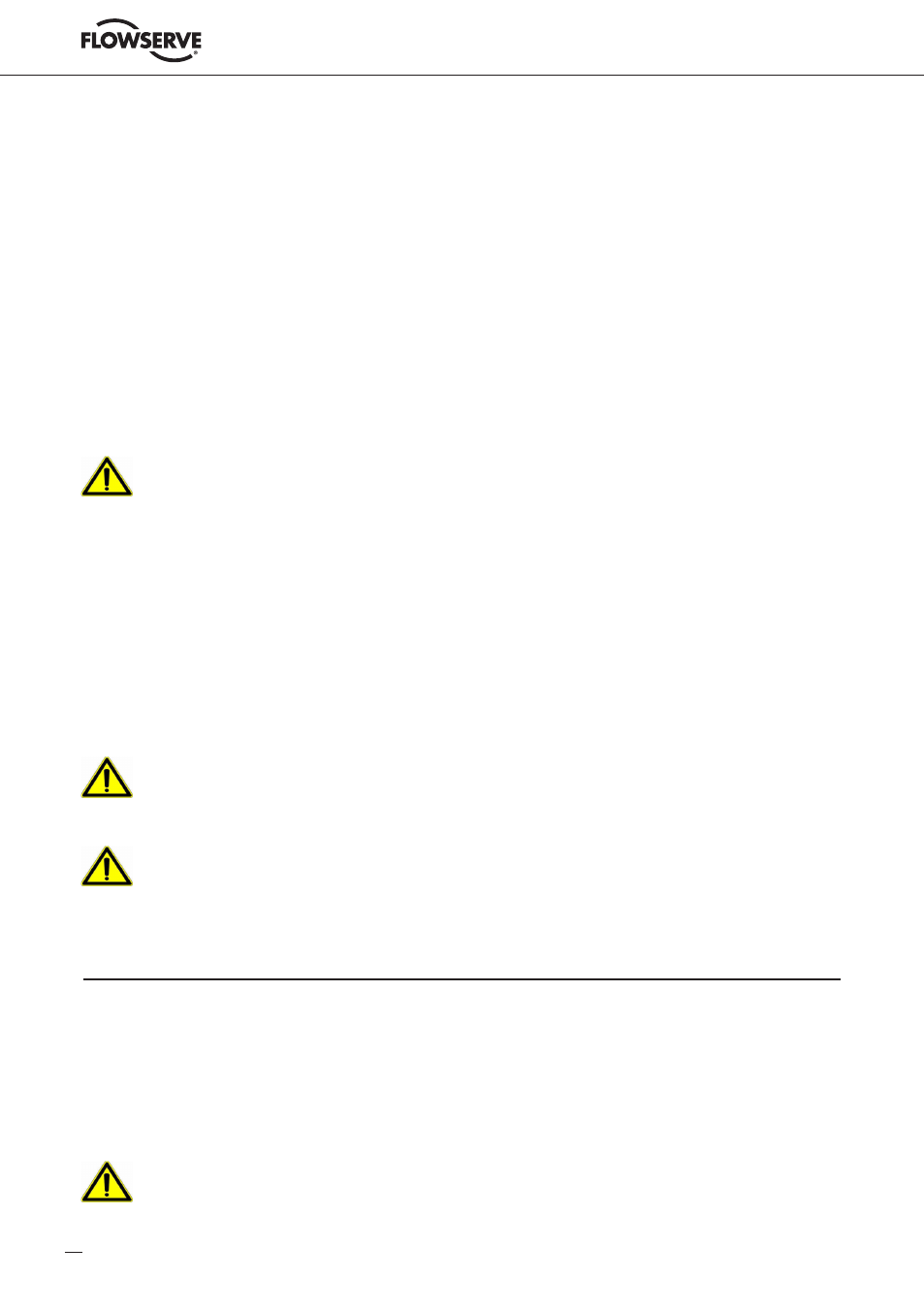
14
9.8
Liquid seal requirements: Do not start the equipment dry. Open valves to flood
equipment with product. Vent all air and/or product vapor from the equipment
casing and the seal chamber before start up. Vent casing and tubing of heat
exchange (if applicable).
Process fluid must flood and pressurize the seal chamber at all times for single seal
and non-pressurized dual seals. Barrier fluid must flood dual seals at all times during
equipment operation.
Gas seal requirements: Do not apply liquids to gas seal designs. Non-pressurized dual
seals with the outboard seal designed to work in gas must be connected only to a gas
purge, if applicable.
9.9
When required, dry steam should be applied to the quench connection.
Use a needle valve (or other flow restriction) to provide 0.1 bar (1 to 1.5 psi) steam
to the quench connection on the seal gland.
Take care to apply steam pressure gradually to prevent an unsafe situation due to
an excessive flow of hot steam being blown into the operator’s working area.
This should result in wisps of steam exiting the seal gland area. Ensure that all
condensate is drained from the supply line and open the steam quench slowly
before the pump is preheated to prevent thermal shock.
9.10 Start up equipment in accordance with normal maintenance procedures unless
specifically requested otherwise by Flowserve.
If the equipment is not operating properly (e.g. seals and / or bearings running hot,
cavitation, heavy vibration, etc.), shut down the equipment, investigate and remove
the cause.
The temperature of the external of the mechanical seal depends from the operating
temperature of the product and/or barrier fluid.
Proper precautions need to be taken to prevent contact with hot parts
Points 9.1 to 9.10 must be taken into account during the first start up as well as
during restarts after machine was stopped.
10. Shut Down, Disassembly
The equipment can be shut down at any time. Before the mechanical seal can be removed the
equipment must be de-pressurized and drained.
Operator must persuade himself before starting disassembling of mechanical seal that
the external of the equipment is cool enough to be handled without risk.
Barrier pressure (if applicable) must be relieved after the equipment has been de-pressurized.
Dismantling of the mechanical seal is only allowed after machine has been stopped.
!