Worcester actuation systems – Flowserve DRC-17 User Manual
Page 22
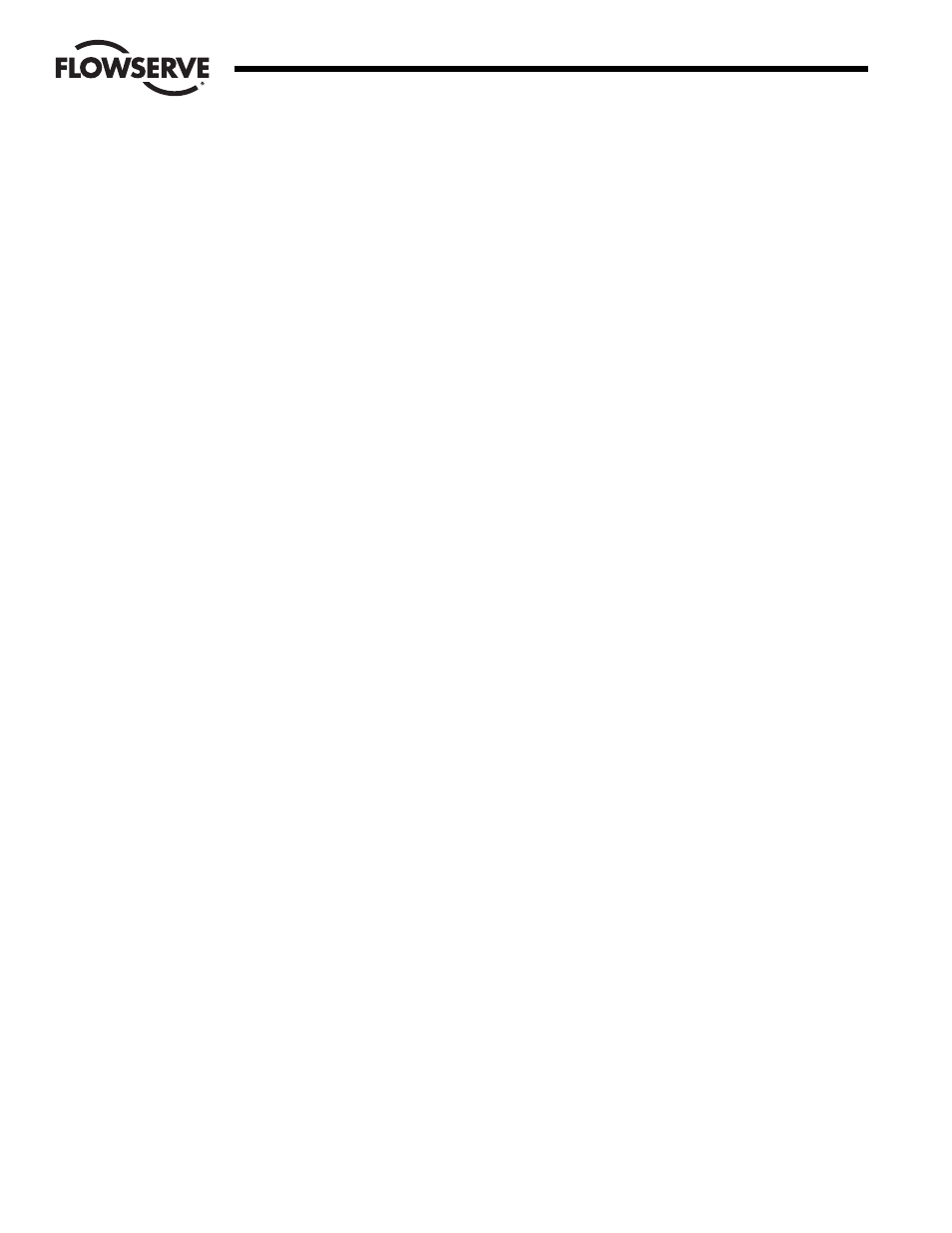
22
DataFlo Digital Electronic Remote Controller DRC17
WCAIM2058
When step 2 valve movement has completed, the
display will alternate between Step #2 and the number
of seconds the step has taken. Step 2 is waiting for
the process to stabilize at the new valve position. If
the process does not stabilize within 30 minutes, the
tuning procedure will be aborted and the TIMEOUT
message will be displayed. The error message will
remain until the ENT key is pressed.
When step 2 has completed, the shaft will be moved
clockwise by the specified valve increment, returning
it to the original starting position. The display will
show Step #3 while the valve is moving.
When step 3 valve movement has completed, the
display will alternate between Step #3 and the number
of seconds the step has taken. Step 3 is waiting for
the process to stabilize at the new valve position. If
the process does not stabilize within 30 minutes, the
tuning procedure will be aborted and the TIMEOUT
message will be displayed. The error message will
remain until the ENT key is pressed.
When step 3 completes, a set of PID parameters will
be computed. Those parameters include the P-term,
I-term, D-term, and the cycle time. The display will
alternate between P-term and the proposed valve. The
operator can examine the other values by pressing
the
and
keys.
At this point, the operator can either accept all of the
proposed values, or reject them. If the values are
accepted, they will be programmed and will be in use
when the Run Mode is re-entered. If the values are
rejected, the original PID terms will remain in effect.
To accept all of the proposed values, press the ENT
key. To reject the values, press the
key. After either
ENT or
is pressed, control will return to the
Manual Position Mode.
It may be desirable to run the Auto-Tune procedure
several times using different valve starting points and
different valve increments, writing down the proposed
PID terms for each procedure. In that way, an
operator can determine PID terms from the
intermediate results and install them in the Program
Mode. See section 4.4 for other notes on tuning.
4.9 Calibration Mode
The Calibration Mode is used to adjust electrical components for
accuracy and for the proper range. The DRC is calibrated from
the factory for the process module selected. For the best
accuracy the DRC can be calibrated in the system where it will
be used.
4.9.1 Entering the Calibration Mode
In the Run Mode, press either the
key or the
key
until the mode display appears.
Press ENT to edit the value. It will start blinking the
current mode.
Press either
or
until CAL is visible.
With CAL blinking, press the ENT key to change to the
Program Mode.
If the security code is zero, no security code is needed to
enter the mode.
Otherwise, when prompted for the security code, press
ENT.
Press
and
to enter the correct security code then
press ENT to enter the mode.
If the incorrect security code is entered, the Calibration
Mode cannot be entered.
Calibration is performed by displaying the item to be
calibrated, then executing the procedure for that item. The
steps in the calibration procedure will depend on the type
of setpoint input signal used and the process module
used. The calibration of valve position and cycle time is
the same for all models of DRC used. The steps below
assume the Calibration Mode has successfully been
entered.
4.9.2 Calibration of Valve Position
Press the
or
key until MaxCW is displayed
alternating with its voltage value.
Press ENT to calibrate the clockwise position, the display
will continuously show a voltage value.
Press the
or
key to adjust the valve position to the
correct full clockwise position. Adjust the feedback pot by
rotating the face gear, located on the actuator shaft, with
your fingers for a reading between .200 and .400 volts.
NOTE: It is not necessary to loosen or remove face gear
snap ring (if present) to rotate gear — it is a friction fit.
For gears that do have a snap ring and if for any reason
the snap ring must be removed, do not overstretch it. Use
the minimum opening to allow the ring to slip over the
gear.
With the valve in the proper full-clockwise position, press
the ENT key to record the position. The display will then
alternate MaxCW with its voltage value.
Press the
key once to display MaxCCW alternating with
its voltage value.
Press ENT to calibrate the counterclockwise position, the
display will continuously show a voltage value.
Press the
or
key to adjust the valve position to the
correct full-counterclockwise position.
With the valve in the proper full-counterclockwise
position, press the ENT key to record the position. The
display will then alternate MaxCCW with its voltage value.
The valve position is now calibrated.
Upon successful completion of this procedure, the cycle
time calibration procedure should also be performed.
Flow Control
Worcester Actuation Systems