Worcester actuation systems – Flowserve DRC-17 User Manual
Page 24
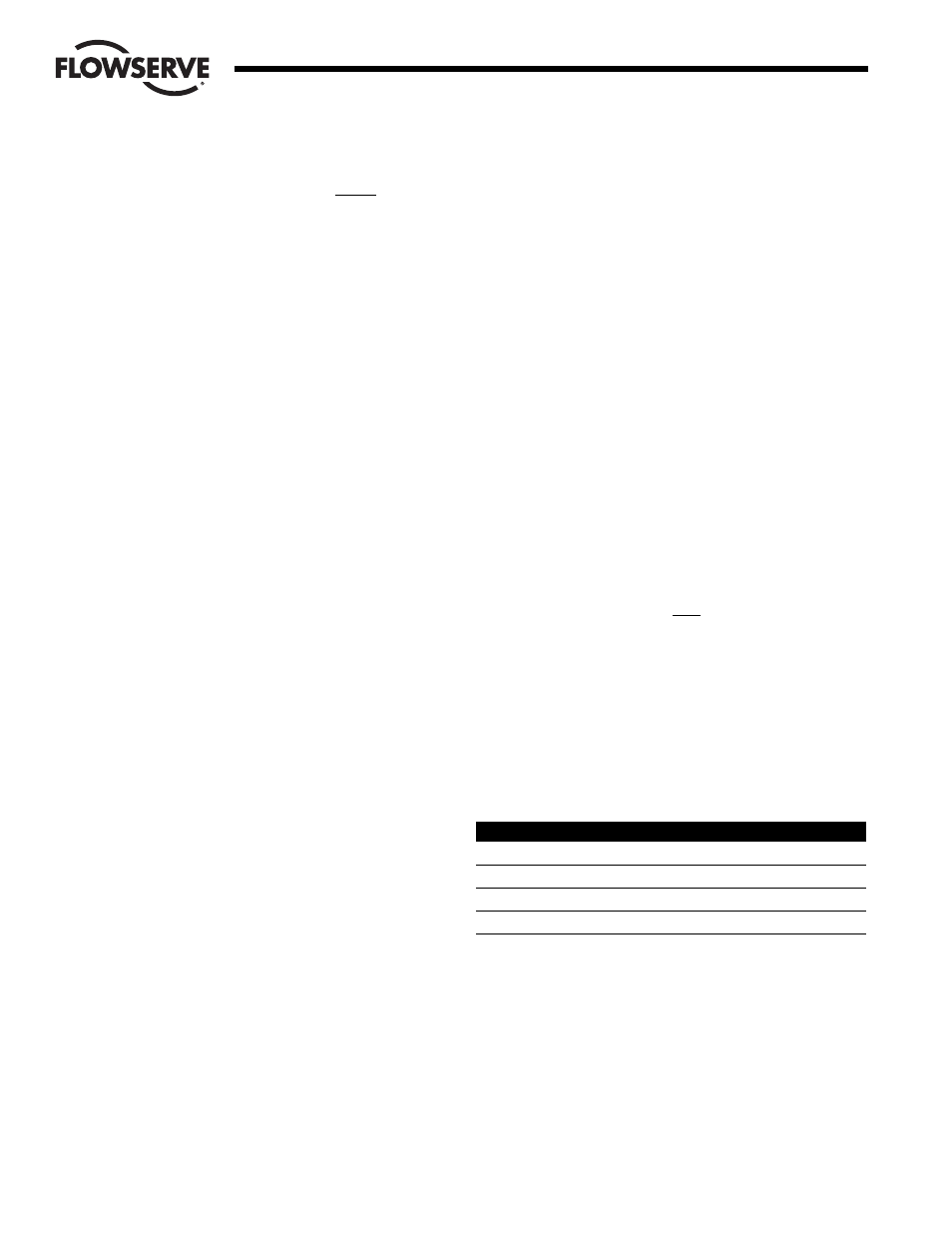
24
DataFlo Digital Electronic Remote Controller DRC17
WCAIM2058
4.9.7 Calibration of an RTD Process Input
NOTE: This procedure applies only if an RTD process
module is used. Example: DRC17 – 4 – R – 3 – 120A
RTDs are used to monitor a wide temperature range.
When the DRC is ordered with an RTD process module,
the order code can specify the range and the module will
be factory-calibrated for that range. The module, however,
can be used in other temperature ranges. The RTD
module can be used in the temperature range of –200°C
to +800°C or –300°F to +999°F. For better control, the
RTD process module can be set to monitor a narrower
temperature range. The following procedure is used to
specify the degree units, upper and lower temperature
ranges, and voltage measurements of the upper and
lower temperature points.
Any one step in the following procedure can be
performed without performing the others. However, it is
recommended to perform all the calibration steps if any
one item is changed. Calibrating the RTD process module
involves adjusting the span and zero potentiometers on
the module and a calibrated 100-ohm platinum RTD
simulator is needed.
Attach a calibrated 100-ohm platinum RTD simulator to
the process input in place of the actual RTD used.
Press the
or
key until either Proc Lo or Proc Hi is
displayed alternating with its voltage value.
Press ENT to begin the RTD calibration procedure. The
display will show Units alternating with the current degree
units. If the temperature degree units are correct, go to
the next step. Otherwise, press the ENT key and use the
and
keys to change the value to either Deg C or Deg
F. When the correct units are displayed, press the ENT key
to lock in the units. Note that if the units are changed, the
upper and lower ranges will be set to the widest possible
range for the units selected. Be sure to check the upper
and lower range after setting the units.
Press
to advance to the Upr Rng display which
alternates with the upper temperature range. If the upper
range is correct, go to the next step. Otherwise, press the
ENT key and use the
and
keys to change the upper
range. The upper range must be at least 50°C or 100°F
higher than the lower range temperature. The lower range
may need to be lowered to properly set the upper range.
When the upper range is correctly displayed, press ENT
to lock in the value. This and the next step may need to
be repeated to get the proper range established.
Press
twice to advance to the Low Rng display which
alternates with the lower temperature range. If the lower
range is correct, go to the next step. Otherwise, press the
ENT key and use the
and
keys to change the lower
range. The lower range must be at least 50°C or 100°F
lower than the upper range temperature. The upper range
may need to be raised to properly set the lower range.
When the lower range is correctly displayed, press ENT to
lock in the value. This and the next step may need to be
repeated to get the proper range established.
With the temperature range properly set, press the
or
keys to get to the Hi ADC V display alternating with its
voltage value. Press the ENT key to begin voltage
calibration. Using the RTD simulator, simulate the upper
limit temperature and adjust the span potentiometer on
the module such that the voltage displayed is between
4.200 volts and 4.700 volts. Change the RTD simulator to
simulate the lower limit temperature and adjust the zero
potentiometer on the module such that the displayed
voltage is between 0.200 volts and 0.800 volts. Repeat
the above process until the upper and lower voltages are
within the stated limits. When completed, set the
simulator to the upper limit temperature. Press ENT to
lock in the upper limit voltage.
Press the
key twice to get to the Lo ADC V display
alternating with its voltage value. Press the ENT key to
begin voltage calibration. Using the RTD simulator,
simulate the lower limit temperature. Do not adjust either
the span or zero potentiometers in this step! Press ENT to
lock in the lower limit voltage.
The RTD process module is now calibrated for the
specified range. Press
to return to the Run Mode.
4.9.8 Calibration of a Thermocouple Process Input
NOTE: This procedure applies only if an thermocouple
process module is used.
Example: DRC17 – 4 – J – 1 – 120A
Thermocouples are used to monitor a wide temperature
range. When the DRC is ordered with a thermocouple
process module, the order code can specify the range and
the module will be factory-calibrated for that range. The
module however can be used in other temperature ranges
as shown in the table below. For better control, the
thermocouple process module can be set to monitor a
narrower temperature range. The following procedure is
used to specify the thermocouple type, degree units,
upper and lower temperature ranges, and voltage
measurements of the upper and lower temperature points.
Thermocouple
Fahrenheit Range
Celsius Range
Type J
32 to 900
0 to 500
Type K
32 to 999
0 to 550
Type T
32 to 750
0 to 400
Type E
32 to 650
0 to 350
Any one step in the following procedure can be
performed without performing the others. However, it is
recommended to perform all the calibration steps if any
one item is changed. Calibrating the thermocouple
process module involves adjusting a gain potentiometer
on the module and a thermocouple simulator is needed.
Attach a calibrated thermocouple simulator to the process
input in place of the actual thermocouple used.
Press the
or
key until either Proc Lo or Proc Hi is
displayed alternating with its voltage value.
Flow Control
Worcester Actuation Systems