Field service checklist – Greenheck Maxitrol Series 14 User Manual
Page 4
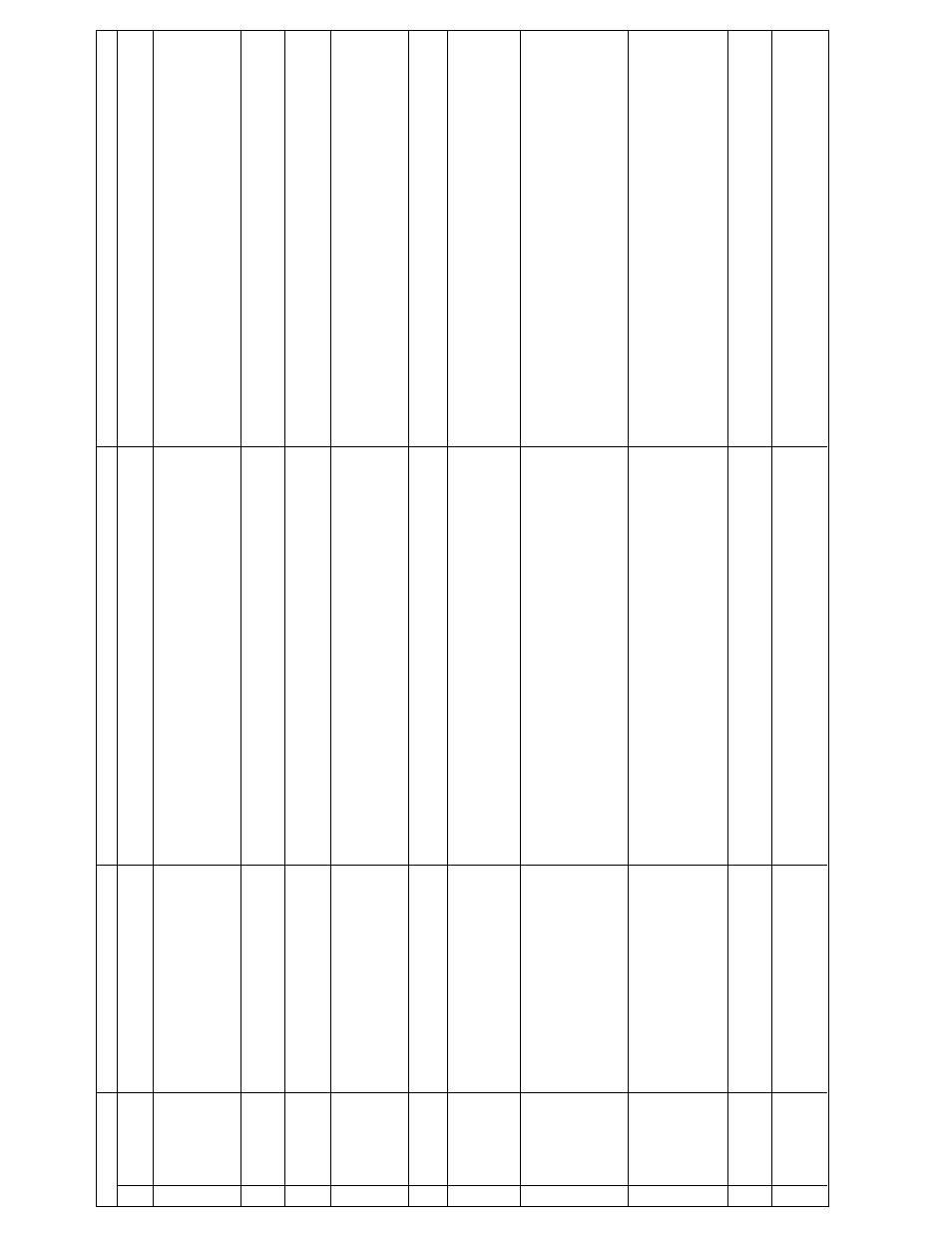
6.
Replace modulator head if not approximately 45-55 ohms for M611 Valve and 60-80 ohms
for MR212 Valve.
7.
Clean or replace plunger if necessary. Install as per diagrams page 3.
1
7
.
If flame stabilizes, adjust sensitivity control to maintain an even flame.
1
8
.
If the flame is steady throughout the entire modulating range, the TS114 must be moved.
1
9
.
If smooth operation results, isolate effected wiring from source of induced voltage.
2
0
.
If erratic or unstable D.C. voltages are obtained throughout the modulating range, the
amplifier may be assumed faulty. Replace. If erratic operation is noted only over a small
range of 2 or 3 volts, the voltage source may contain surges. Consult Maxitrol.
2
1
.
Sensed temperature will vary from TD114 dial settings. This is intentional.
2
2
.
Correct wiring.
2
3
.
See calibration procedure.
2
4
.
Move TS114 to location where average representative temperature can be sensed.
2
5
.
TD114 dial setting, then check thermostat setting and/or check wiring for shorts.
1.
Modulating valve improperly installed (or see
Symptom ‘L’).
7.
Plunger missing, jammed or improperly
installed.
1
0
.
Short circuit in TD114 Remote Temperature
Selector circuit or wiring.
1
1
.
Open circuit in TS114/TS10765. Discharge or
Inlet Air Sensor Circuit or wiring.
1
2
.
Jumper not connected across amplifier
terminals 2 and 3.
1
3
.
Foreign object holding valve open.
1
4
.
Plunger jammed.
1
5
.
Inlet pressure too low.
1
6
.
Incorrect outlet pressure adjustment of
Pressure Regulator.
1
7
.
Hunting.
1
8
.
Erratic air patterns or improper TS114 location.
1
9
.
Wiring is run next to high voltage switching
circuits causing induced voltages.
2
0
.
Faulty Amplifier or erratic voltage supply.
2
1
.
Inlet Air Sensor is used.
2
2
.
Incorrect Wiring.
2
3
.
System out of calibration.
2
4
.
Improper TS114 location.
2
5
.
Room Override Thermostat circuit closed.
1.
Install properly.
2.
Prove the power source.
3.
Tighten connections or replace wiring.
4.
If modulating voltages are obtained, Check TS114 circuit for shorts. Replace TS114 if
necessary.
5.
If items 2, 3, and 4 check out and modulating voltages are still not obtained, amplifier
may be assumed faulty. Replace.
8.
Adjust to proper minimum fire.
9.
If reading is greater than 1.5” negative pressure, check for clogged filters or other
inlet air restrictions. Consult factory for other solutions.
1
0
.
Correct wiring if shorts exist.
1
1
.
If modulating voltages are obtained, check TS114/TS10765 for open circuits. Replace
TS114/TS10765.
1
2
.
Correct the wiring.
1
3
.
Clean seat. Clean valve or replace if necessary.
1
4
.
Clean, or if necessary, replace plunger.
1
5
.
Increase inlet pressure if possible.
1
6
.
See valve adjustments on page 8.
1.
Arrow on side of Valve should point in direction of gas flow.
2.
Check for 24V AC at amplifier terminals 7 and 8.
3.
Inspect for loose or broken wires between amplifier terminals 1and 2, and TD114
terminals 1 and 2, and TD114 terminals 1 and 3.
4.
Connect test resistor as described in Preliminary Circuit Analysis. Follow procedure
outlined.
5.
Check items 2, 3 and 4.
6.
Measure resistance across modulator terminals with connecting wires detached.
7.
Inspect. Plunger should be installed per diagrams page 3 and operate freely in solenoid
sleeve.
1
0
.
Inspect for shorts at or between Amplifier terminals 1 and 2 or TD114 terminals 1 and 3.
1
1
.
Check TS114/TS10765 for open internal circuit. Connect test resistor as described
in Preliminary Circuit Analysis. Follow procedure outlined.
1
2
.
Inspect.
1
3
.
Remove bottom plate and inspect valve and seat.
1
4
.
Inspect. Plunger should be smooth, clean, and operate freely in solenoid sleeve.
1
5
.
Read pressure at inlet to modulating valve using a manometer with unit operating at full
fire. Pressure should be equal to the sum of outlet pressure
setting plus pressure drop of
the valve (see Maxitrol Capacity Chart).
1
6
.
Read manifold pressure using manometer and compare with recommendation of
equipment manufacturer.
1
7
.
Adjust sensitivity control counter-clockwise.
1
8
.
Connect test resistor as described in Preliminary Circuit Analysis. Turn TD114 selector dial
so heater goes through its entire modulating range.
1
9
.
Temporarily wire each of TD114, TS114, and MR212 externally and observe heater/
equipment operation.
2
0
.
With test resistor connected (per Item #18) and TD114 locally connected (per item#19),
turn TD114 selector dial through entire modulating range. Observe D.C. voltage across
modulator terminals.
2
1
.
Inlet Air Sensor changes 1
0
for each 3.5
0
, 5
0
, or 8
0
outside temperature change from 60
0
(predetermined – turndown varies with model used).
2
2
.
Check wiring diagrams page 7.
2
3
.
Sensed temperature (thermometer next to TS114) does not correspond to TD114 setting.
2
4
.
Sensed temperature (thermometer next to TS114) does not represent average
discharge
air
temperature.
2
5
.
Remove Override Thermostat lead from terminal 2 of TD114.
2.
Short circuit or no voltage to the amplifier.
3.
Open circuit in TD 114. Remote Temperature
Selector circuit or wiring.
4.
Short circuit in TS114, Discharge Air Sensor
circuit or wiring.
5.
Faulty amplifier.
8.
See valve adjustments on page 8.
9.
Close main gas supply and measure manifold pressure with blower operating.
Reading should be less than 1.5” w.c. negative pressure.
6. Short circuit or open circuit in Modulator Coil.
9.
Excessive negative burner pressure.
8.
Incorrect by-pass metering valve adjustment.
SYMPTOM
POSSIBLE CAUSE
FIELD TEST
REMEDY
No gas flow.
Continuous
Low Fire (electronics
problem).
Continuous Low
Fire (electronics OK).
Incorrect Minimum
Fire Erratic or
Pulsating Flame.
Continuous High
Fire (electronics
problem).
Continuous High
Fire (electronics OK).
Incorrect Maximum
Fire.
Erratic or Pulsating
Flame.
Incorrect Discharge
Air Temperature.
A
.
Field Service Checklist
Burned out
Transformer.
2
6
.
Short circuit in modulator coil.
2
7
.
Short circuit between amplifier and modulator
valve.
2
6
.
Measure resistance across modulator terminals with red lead wires disconnected.
2
7
.
Inspect wiring.
2
6
.
Replace modulator head if less than 40 ohms.
2
7
.
Correct wiring is short is found.
Discharge Air
Temperature too
Low when T115 is
operative.
2
8
.
Too low an Override Temperature setting.
2
9
.
Burner capacity may be insufficient.
2
8
.
Check “Override Temperature Selector” of TD114.
2
9
.
Check for high fire (Maximum manifold pressure specified for heater).
2
8
.
Reset to correct temperature.
2
9
.
If on high fire, control can do no more. Heater unable to furnish additional heat to raise
temperature.
B.
C.
D.
E.
F.
G.
H.
I.
J.
K.
©2007 Maxitrol Comp
an
y,
All Right
s Reserved
4