Introduction, Douglas m kensrue – MK Products Pulse+ User Manual
Page 8
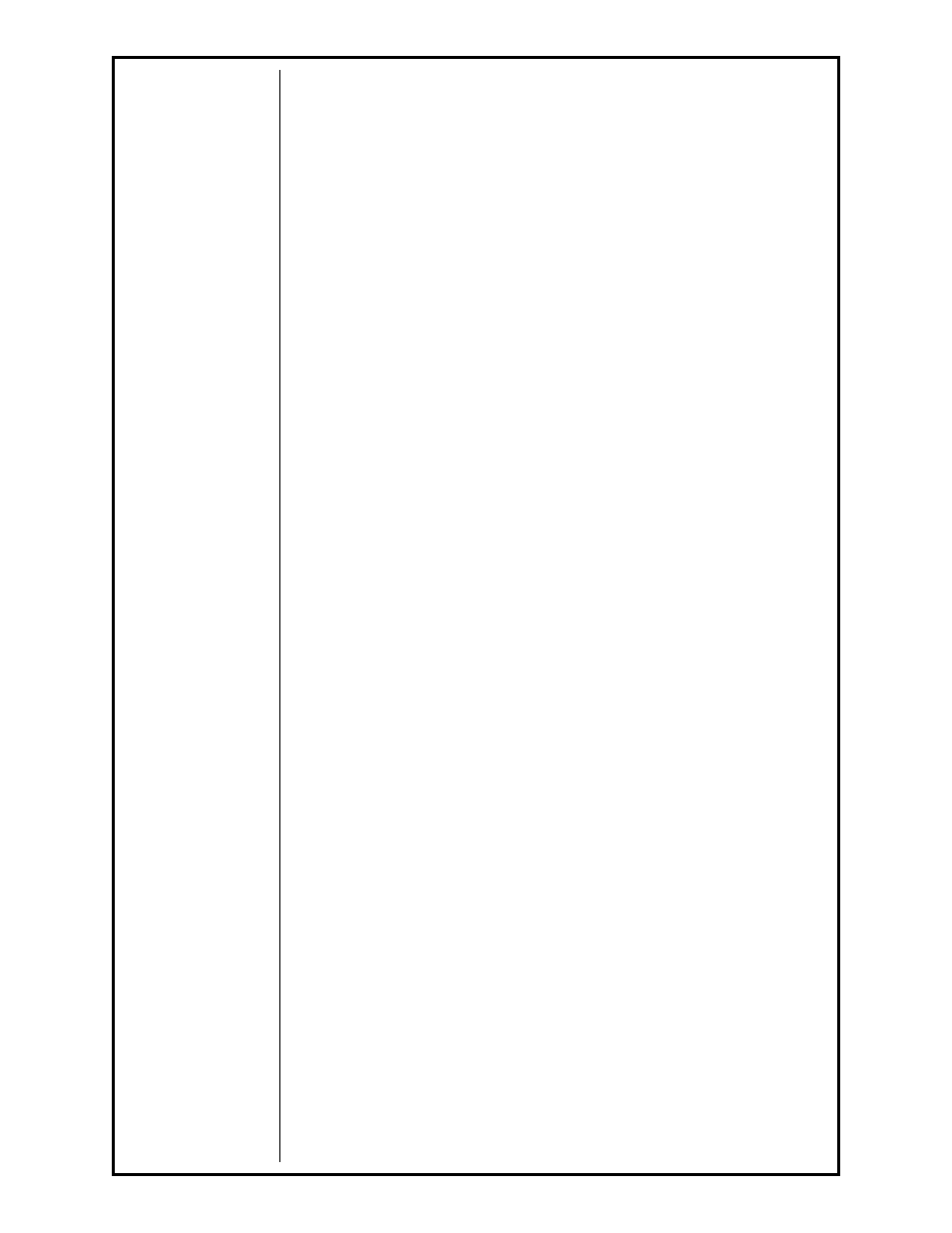
Pulse+ Owner's Manual Page 8
INTRODUCTION
MK Products’ patented Pulse+ is a transistorized pulse-generating
attachment which converts a conventional constant voltage (CV) D.C.
power supply into a variable pulsed arc welding machine.
The Pulse+ is exceptionally simple to operate and may be used with any
conventional constant voltage (CV) machine, up to 60 open circuit volts
and 300 amperes continuous current output. It provides pulse rates
continuously variable from 500 pulse per second, down to approximately
30 pulses per second. This of course, includes the frequencies of 60 and
120 pulse per second, available from thyristor supplies operating at line
frequencies.
The power supply voltage control set the peak voltage, and the background
level is a fixed value by design. The “On time” control is used to adjust the
length of the pulse during metal transfer and can be used to apply more
heat to the weld. The “Off time” control regulates how close the “on”
pulses are together, which can reduce the amount of heat into the weld.
The Pulsed-arc process is a transfer process wherein spray transfer occurs
at regular intervals rather than at random intervals. The welding current
rapidly switches from high pulsed current to low background current level.
The background current sustains the arc, while each pulse supplies just
enough power to free one droplet from the wire tip. In the time between
pulses, the welding current is reduced, and no metal transfer occurs.
Pulsed spray uses a lower average current than in regular spray transfer.
This lower average current makes it possible to weld out of position. By
using a lower average, less heat is put into the metal, causing less distor-
tion of the material being welded. Thin metal sections may also be welded
more easily with pulsed spray, and it creates very little metal spatter. In
addition, the pulse agitation aids in cleaning action and outgasing, which
reduces porosity.
The pulsed spray transfer method can use larger diameter electrode wire
and still produce a small weld. This is a great advantage, because larger
diameter electrode are less expensive than smaller ones. Also, nonferrous
wire of a larger diameter can be fed through the wire feeder much easier
without risk of bending or jamming. This also allows using one size wire for
a variety of jobs using many different thicknesses of metal and joint
designs with just one setup in the wire feeder!
At MK Products, we stand behind every product manufactured and ensure
that it is free from defects and will perform to the specification con-
tained in this manual. If for ANY reason you are not completely satisfied
with your purchase, we will make every effort to repair, replace, or refund
your purchase.
That is my guarantee.
Douglas M Kensrue
President
MK Products