3 starting the chiller – AEC ACOA Series Air-Cooled Central Chillers User Manual
Page 35
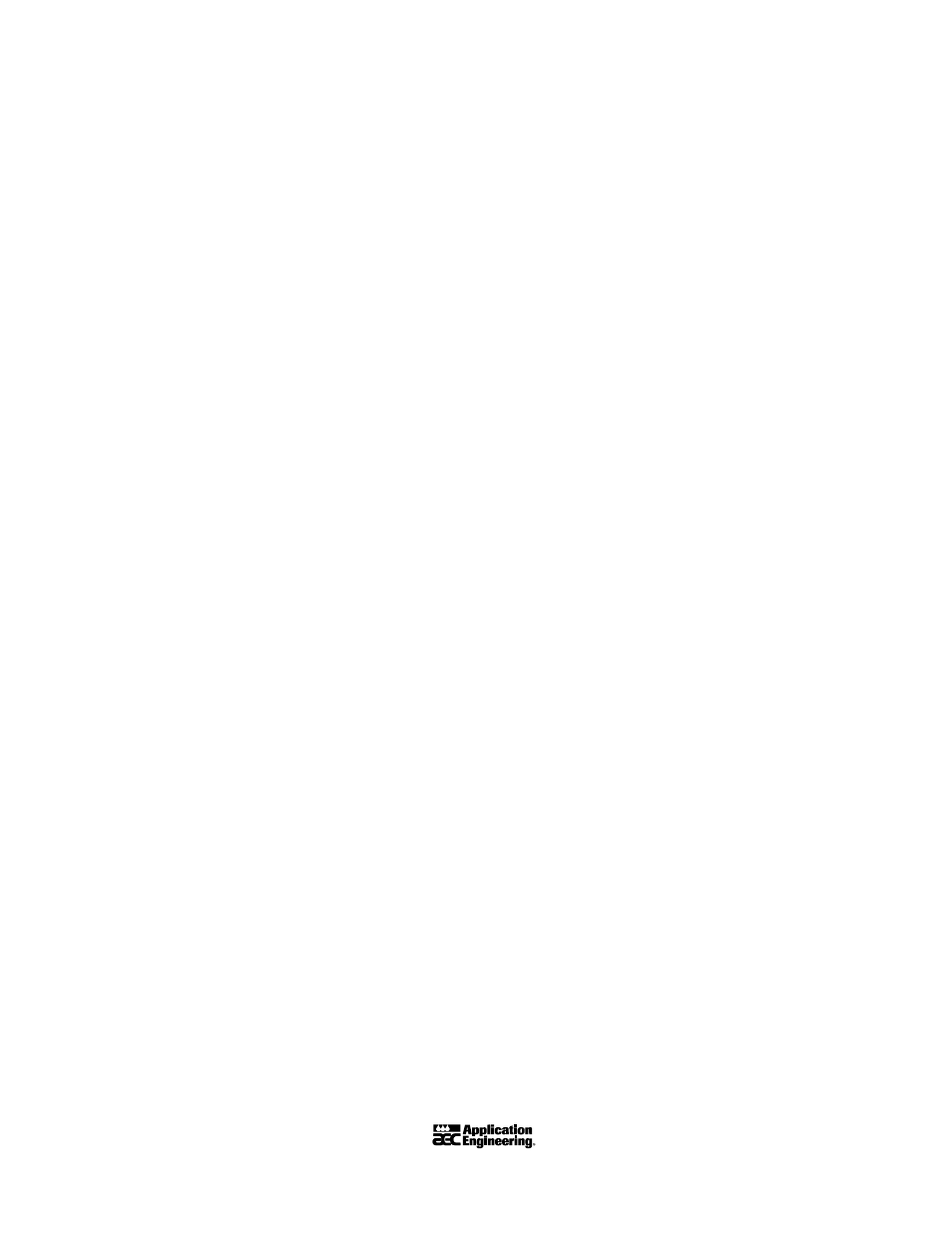
Calibrated refrigerant gauges have been connected to the suction, discharge and oil pressure
ports.
The optional or field installed chilled water supply and return valves on the chiller are open.
The auxiliary reservoir tank and process water circuit piping are filled with a water/glycol
mixture. The water/glycol mix should provide freeze protection to 20° below the leaving
water temperature or anticipated ambient.
The chilled water pump rotation direction has been checked, and the water flow and pressure
through the evaporator has been adjusted to the specified flow rate.
The remote condenser fans have been manually energized and checked for proper rotation
direction. Fans should pull air through the condenser coil and discharge vertically upwards.
You can change rotation on three-phase motors by interchanging just two wires on the main
terminal block.
All refrigerant valves are open.
5-3 Starting the Chiller
1. Energize crankcase heaters for at least 24 hours before startup. Crankcase oil temperature
must be at least 100ºF (38ºC). This action vaporizes any refrigerant dissolved in the oil,
and assures that the oil is within normal operating temperature range.
2. Before starting the compressor(s), check all three phases of supply voltage of all legs of
the motor. They must be within plus or minus ten percent (±10%) of the nameplate
voltage and not have an imbalance exceeding two percent (2%).
3. Start compressor(s), check the gauges and note if the pressures are within the prescribed
limits.
4. Check the refrigerant sight glass at the TX Valve to be sure it is free of bubbles. If not,
see Section 7-8 on Page 47.
5. Shut the compressor down and check the compressor crankcase sight glass for proper oil
level. It should be
1
/
3
to
1
/
2
up on the sight glass. If not, add oil. See Section 5-4 on the
following page for more information.
6. Restart the compressor and put the process under load. After an hour, check the
expansion valve superheat setting. It should be between 8ºF and 12ºF (-13ºC and -11ºC)
at full load design conditions. You may need to lower the superheat setting for proper
distribution. Turn the TX valve adjustment stem clockwise to increase the superheat
setting and counterclockwise to decrease the setting. Allow ample time between
adjustments to let the system re-balance.
7. Check electrical control settings and, if necessary, reset to the settings on the wiring
diagram. Safety controls are factory set and must be maintained at settings indicated on
the wiring diagram.
8. Adjust the freezestat cut-out to 10º below the process temperature you want.
Page 34
ACOA Series Air-Cooled Central Chillers