4 three-dimensional tool compensation, Introduction – HEIDENHAIN TNC 426 (280 476) User Manual
Page 141
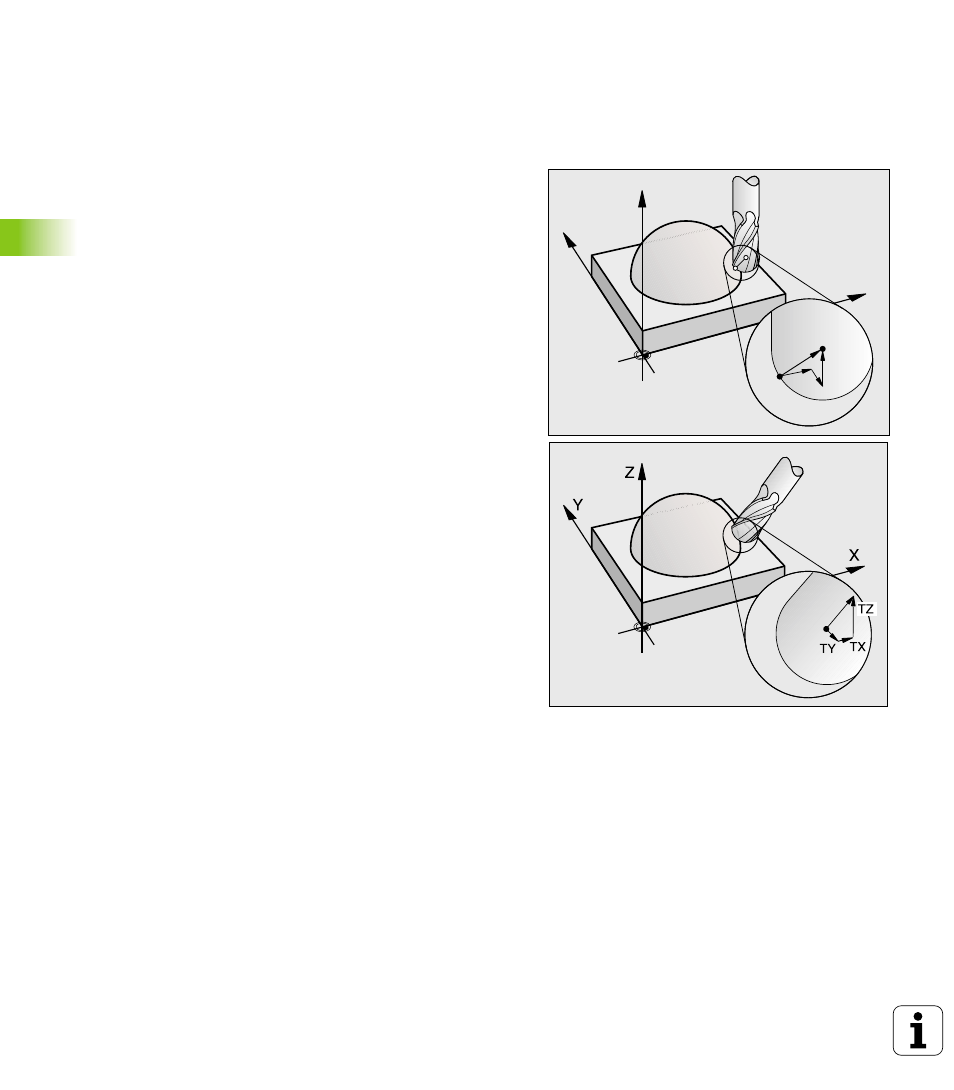
114
5 Programming: Tools
5.4 Thr
ee-Dimensional T
ool Compensation
5.4 Three-Dimensional Tool
Compensation
Introduction
The TNC can carry out a three-dimensional tool compensation (3-D
compensation) for straight-line blocks. Apart from the X, Y and Z
coordinates of the straight-line end point, these blocks must also
contain the components NX, NY and NZ of the surface-normal vector
(see figure above right and explanation further down on this page).
If, in addition, you want to carry out a tool orientation or a three-
dimensional radius compensation, these blocks need also a
normalized vector with the components TX, TY and TZ, which
determines the tool orientation (see figure at center right).
The straight-line end point, the components for the surface-normal
vector as well as those for the tool orientation must be calculated by
a CAD system.
Application possibilities
n
Use of tools with dimensions that do not correspond with the
dimensions calculated by the CAD system (3-D compensation
without definition of the tool orientation)
n
Face milling: compensation of the milling machine geometry in the
direction of the surface-normal vector (3-D compensation with and
without definition of the tool orientation). Cutting is usually with the
end face of the tool
n
Peripheral milling: compensation of the mill radius perpendicular to
the direction of movement and perpendicular to the tool direction (3-
D radius compensation with definition of the tool orientation).
Cutting is usually with the lateral surface of the tool
Z
Y
X
P
T
NZ
P
NX
NY