HEIDENHAIN TNC 620 (340 56x-02) Cycle programming User Manual
Page 237
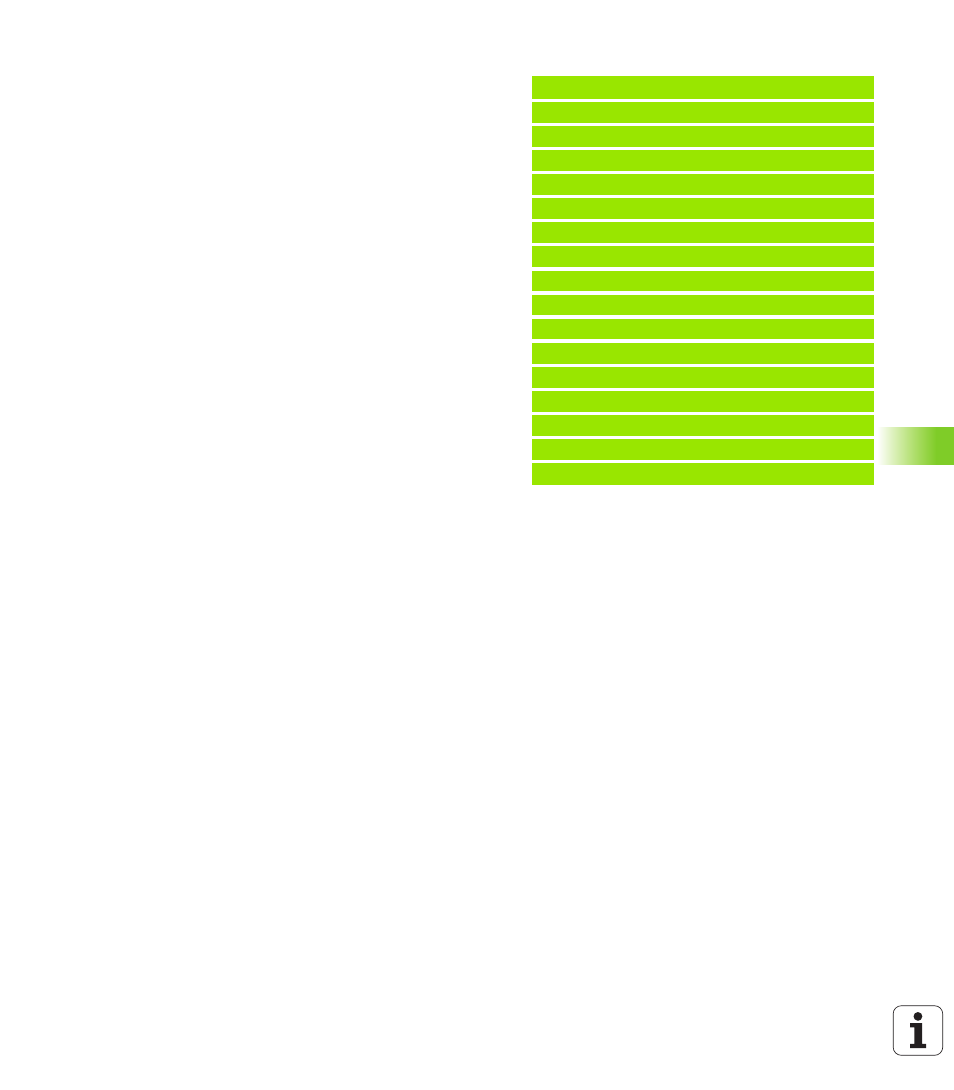
HEIDENHAIN TNC 620
237
1
0
.4 F
A
CE MILLING (Cy
c
le 232, DIN/ISO: G232, A
d
v
a
nced Pr
ogr
a
mming
F
e
at
ur
es Sof
tw
a
re
Option)
U
Setup clearance Q200 (incremental): Distance
between tool tip and the starting position in the tool
axis. If you are milling with machining strategy
Q389=2, the TNC moves the tool at the setup
clearance over the current plunging depth to the
starting point of the next pass. Input range 0 to
99999.9999
U
Clearance to side Q357 (incremental): Safety
clearance to the side of the workpiece when the tool
approaches the first plunging depth, and distance at
which the stepover occurs if the machining strategy
Q389=0 or Q389=2 is used. Input range 0 to
99999.9999
U
2nd setup clearance Q204 (incremental): Coordinate
in the spindle axis at which no collision between tool
and workpiece (fixtures) can occur. Input range 0 to
99999.9999
Example: NC blocks
71 CYCL DEF 232 FACE MILLING
Q389=2
;STRATEGY
Q225=+10
;STARTING POINT 1ST AXIS
Q226=+12
;STARTING POINT 2ND AXIS
Q227=+2.5 ;STARTING PNT 3RD AXIS
Q386=-3
;END POINT IN 3RD AXIS
Q218=150
;FIRST SIDE LENGTH
Q219=75
;SECOND SIDE LENGTH
Q202=2
;MAX. PLUNGING DEPTH
Q369=0.5
;ALLOWANCE FOR FLOOR
Q370=1
;MAX. OVERLAP
Q207=500
;FEED RATE FOR MILLING
Q385=800
;FEED RATE FOR FINISHING
Q253=2000 ;F PRE-POSITIONING
Q200=2
;SETUP CLEARANCE
Q357=2
;CLEARANCE TO SIDE
Q204=2
;2ND SETUP CLEARANCE