Braking – BECKHOFF AL2000 Application User Manual
Page 14
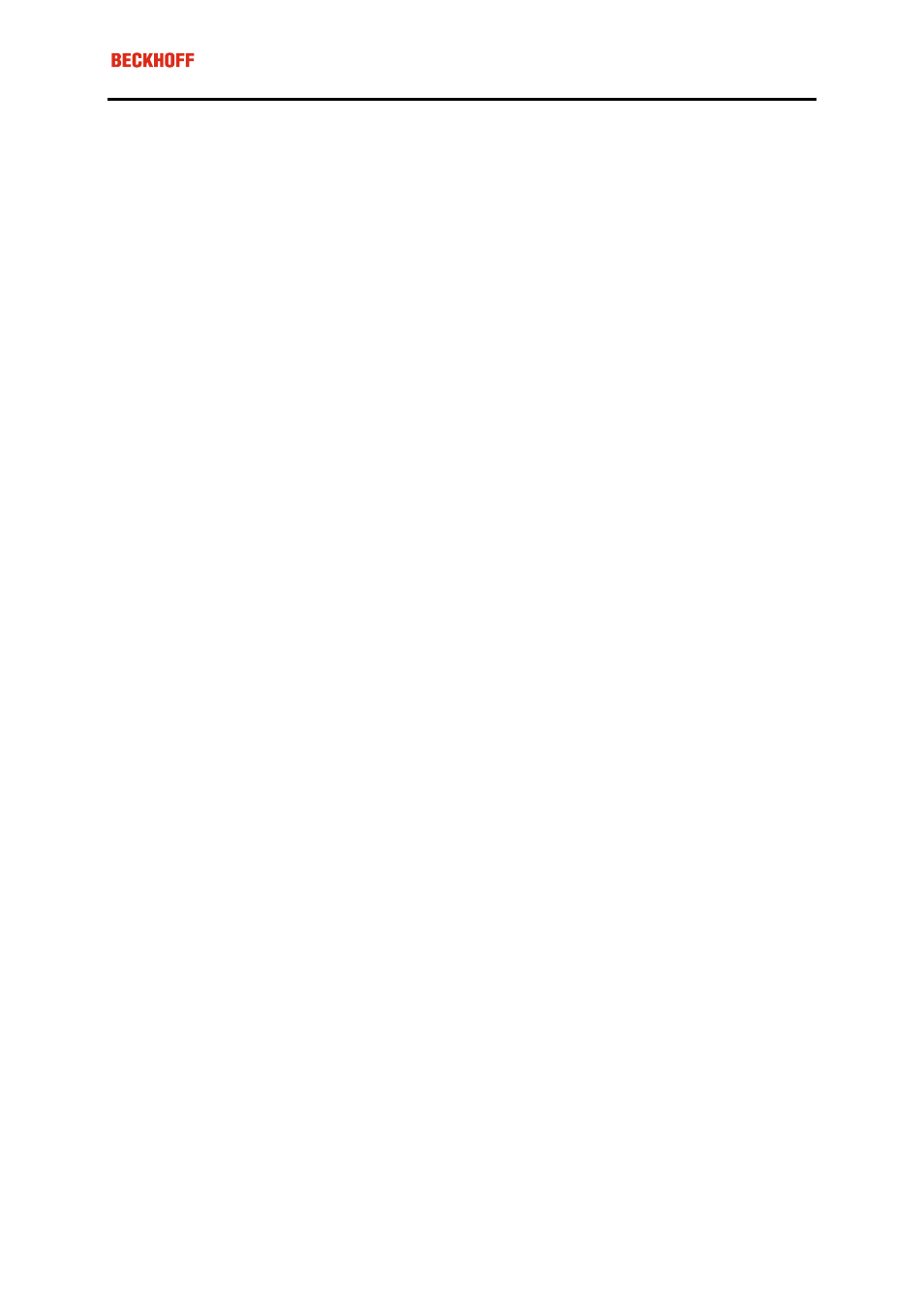
Eiserstraße 5 / D-33415 Verl / Telefon 05246/963-0 / Telefax 05246/963-149
14
Braking
A controlled stop by the servocontroller is recommended, especially with short runouts. The Servocontroller
stops the motor as quick as possible using the maximum force of the motor. This action has to be activated by a
signal from the position controlling system. Herefore power up is required. In addition there should be no error
status in the servocontroller.
Usually a linear motor’s braking depends on the power supply and position information. Without additive meas-
urements this could result in an uncontrolled rollout to the end of the track in case of power loss or measure-
ment and controlling errors. All active solutions need to be activated by the loss of power or control. This means
that a normal, free motion of the slide is only made possible by one or more unlocked or unbolted braking sys-
tems. Suitable is the use of relais.
Risky situations by uncontrolled roll out can be prevented in several ways, such as
1. The use of pneumatic rail guide brakes. This establishes a short runout. Some rail guide suppliers offer bra-
kes that are released by air pressure. These can be very useful for vertical applications and for some safety
situations.
2. Short-circuiting of the motor coils. This results in a moderate runout. A braking force is generated when the
coils are short circuited. There are standard relais for this action. The braking energy is dissipated in the coil
unit. Requirements for relay: current similar to Ipeak, contact resistance below 0.5 Ohms, switching time
according to application requirements.
3. The use of mechanical end stops. Mechanical end stops check the slide at the end of the track. So there is a
maximum run out. Non-flexible end stops are not suitable. Hydraulic or pneumatic dampers absorb the energy
of the movement and stop the slide. Springs cause the slide to be returned, but can be combined with damping
by short circuiting. Requirements: no damage/danger by uncontrolled movement possible
4. a combination of the mentioned measurements.
Which methods are useful depends on the application. For design, consider at least the following worst case
situations:
• Safety violation detected by sensors (linear motor must stop immediatly).
• Programming error, (uncontrolled movement at maximum speed).
• Overtemperature in motor, (linear notor must stop within seconds).
• Fatal error in the Servocontroller (uncontrolled movement).
• Main Power loss (loss of motor control and force).
• DC control Power loss (loss of motor control and force).
• Failure of end of track detector, (hitting end of track).
• Air pressure loss.