Flowserve DS User Manual
Page 18
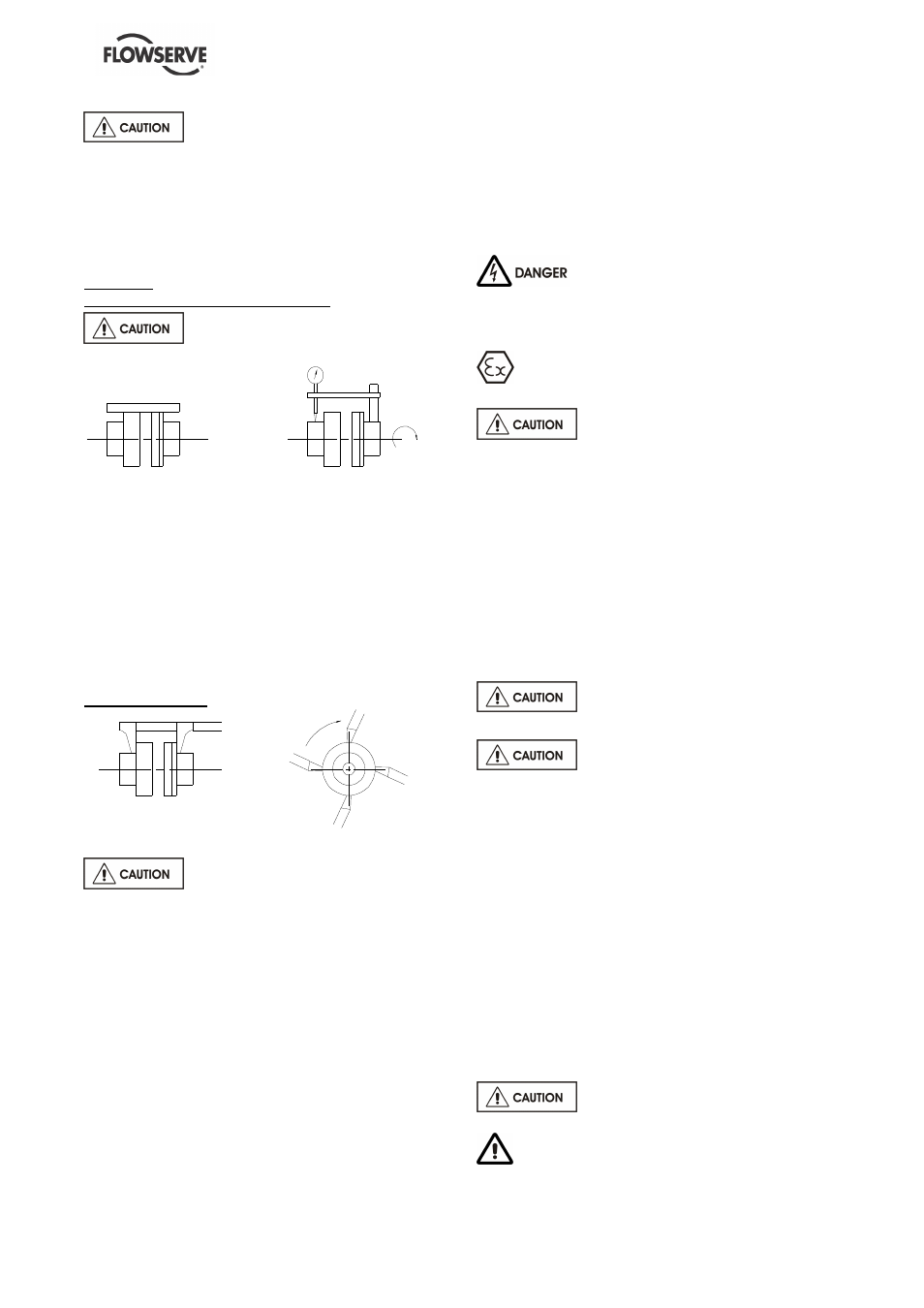
DS USER INSTRUCTIONS ENGLISH 71576283 - 02/13
02
Page 18 of 36
flowserve.com
The alignment MUST be checked.
Although the pump will have been aligned at the
factory it is most likely that this alignment will have
been disturbed during transportation or handling. If
necessary, align the motor to the pump, not the
pump to the motor.
Alignment
Parallelism and concentricity check:
Check the alignment at three or four
points, before piping assembly.
with a rule
with a comparator
Admissible margin for a motor with roller bearings
with European couplings:
= 0.15 mm parallel checking
= 0.1 mm angular checking
For US supplied couplings values to be used are:
= 0.02 in. parallel checking
= 0.05 in. angular checking
Check the couplings manual for further details.
Angular checking:
with a sliding rule
with a caliper gauge
The alignment will be definitive only
after pipe connection (see § 4.5.1).
In case of DSV with cardan shaft drive refer to
respective instruction.
If necessary, improve the machine alignment:
→
Complete unit mounted on common base plate:
The machines are first aligned accurately in our
workshops. Usually, any misalignment observed on
site is due to a wrong adjustment under the base
plate (disturbed during transport or because of
forces exerted by the piping). It is only necessary to
rectify the adjustment under base plate. If it proves
to be insufficient, modify the motor and the piping.
→
Pump and motor mounted on individual base
plates:
Machines are (or must be) first mounted on their
own base plate in the workshop. Once the pump is
set, it will be regarded as the fixed piece. Any
alignment necessary shall be carried out on the
motor.
Never connect the electric motor
before the setting has been completely finished.
4.5 Piping
The user must verify that the equipment is
isolated from any external sources of vibration.
Protective covers are fitted to the
pipe connections to prevent foreign bodies entering
during transportation and installation. Ensure that
these covers are removed from the pump before
connecting any pipes.
4.5.1 Suction and discharge piping
The dimensions of the pipes do not directly depend
on suction and discharge diameters of the pump:
a) First, choose a flow speed < 2 m/s (7 ft/s) at
suction, and about 3 m/s (10 ft/s) at discharge.
b) Take into account the available NPSH, which
must be superior to the required NPSH of the
pump.
Never use pump as a support for
piping.
Do not mount expansion joints in
such a way that their force, due to internal pressure,
may act on the pump flange.
Maximum forces and moments allowed on the pump
flanges vary with the pump size and type.
These external strains may cause misalignment, hot
bearings, worn couplings, vibrations and the
possible failure of the pump casing.
When designing the pipes (§ 4.5.2.1, § 4.5.2.2, §
4.5.3.1) take necessary precautions in order not to
exceed maximum allowed strains.
Forces and moments applied to the pump flanges
must never exceed the values shown in the overall
dimension.
Ensure piping and fittings are flushed
before use.
Ensure piping for hazardous liquids is
arranged to allow pump flushing before removal of
the pump.