0 valve maintenance, 0 disassembly – Flowserve Cast Globe Valves User Manual
Page 17
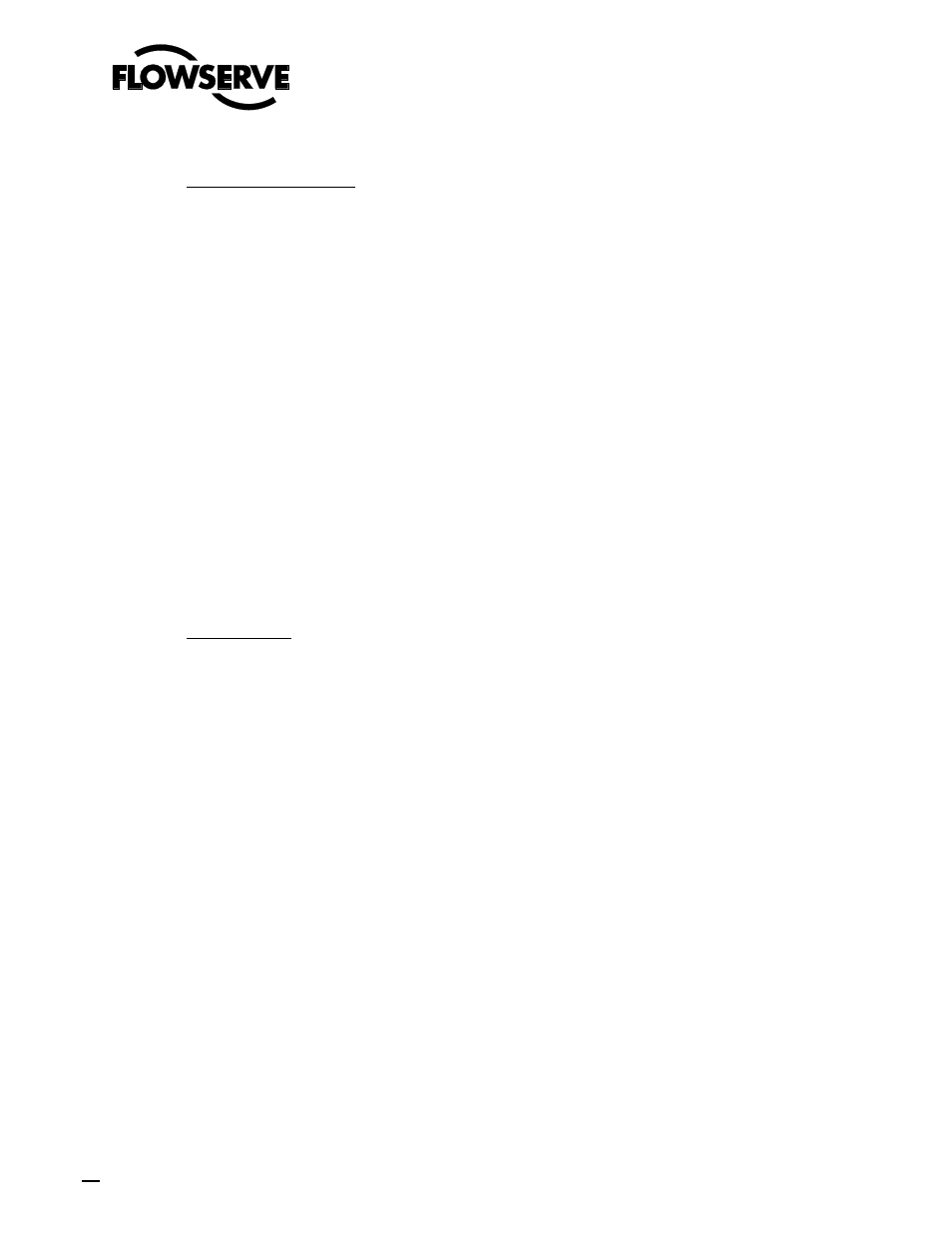
Globe Valves FCD ADENIM0011-00
17
5.0 VALVE MAINTENANCE
(Continued)
5.6
Refinishing Sealing Surfaces
Minor discontinuities in both the disc and seat sealing surfaces, which may cause leakage, can, in many cases, be
removed by lapping. Major defects such as cracks or deep gouges will generally require replacement of the part.
NOTE: Lapping is a polishing process in which a sealing surface is ground with an abrasive held in place by a
special fixture. The abrasive is commonly found in paste form or bonded to a paper backing. Detailed
instructions on the use of lapping abrasives and fixtures, normally supplied with such equipment, should be
adhered to.
In order to maintain seat tightness in globe valves, the sealing surface angles on both the disc and seat ring must be
kept within close tolerance (300 for the seat - 290 for the disc) it is important when lapping to use fixtures that will
maintain these angles. Anchor/Darling does not recommend lapping the disc directly to the seat. A good seal is
dependent on line contact. Direct contact lapping will result in excessive seat widths.
6.0 DISASSEMBLY
By carefully following these instructions any Flowserve valve can be easily disassembled and reassembled. If problems are
encountered with equipment, Flowserve Field Service should be contacted. The use of improper tools or methods may cause
severe damage to the valve and may void the warranty.
Prior to attempting disassembly of a particular valve, the specific assembly drawing for the valve should be referred to.
6.1
Actuator Removal
Valves are supplied with a wide variety of actuating mechanisms. The degree of difficulty involved in their removal
varies significantly. Simple bolt-on units such as handwheels, gear units and electric motor units are fairly
commonplace. Their removal only requires the use of good mechanical practice. More complex pneumatic and
hydraulic units may require specialized skills. Their removal and disassembly should only be attempted by trained
personnel. More detailed information on special actuators will be provided in a separate manual when applicable.
The following general guidelines are provided for information:
1.
Before any attempt to remove the actuator is made, personnel should verify that the system is
depressurized and drained.
2.
The valve should then be cycled partially to remove any trapped pressure and to insure that the disc is not
stuck in the seat.
3.
The disc should then be gently lowered into the seat.
4.
When the valve is to be completely disassembled, Flowserve recommends that the actuator be removed
from the valve separately from the yoke. This will simplify the rigging requirements.