Operation, power actuated valves, Fluid dynamics of shutoff valve operation – Flowserve 50165 Nordstrom Figure User Manual
Page 15
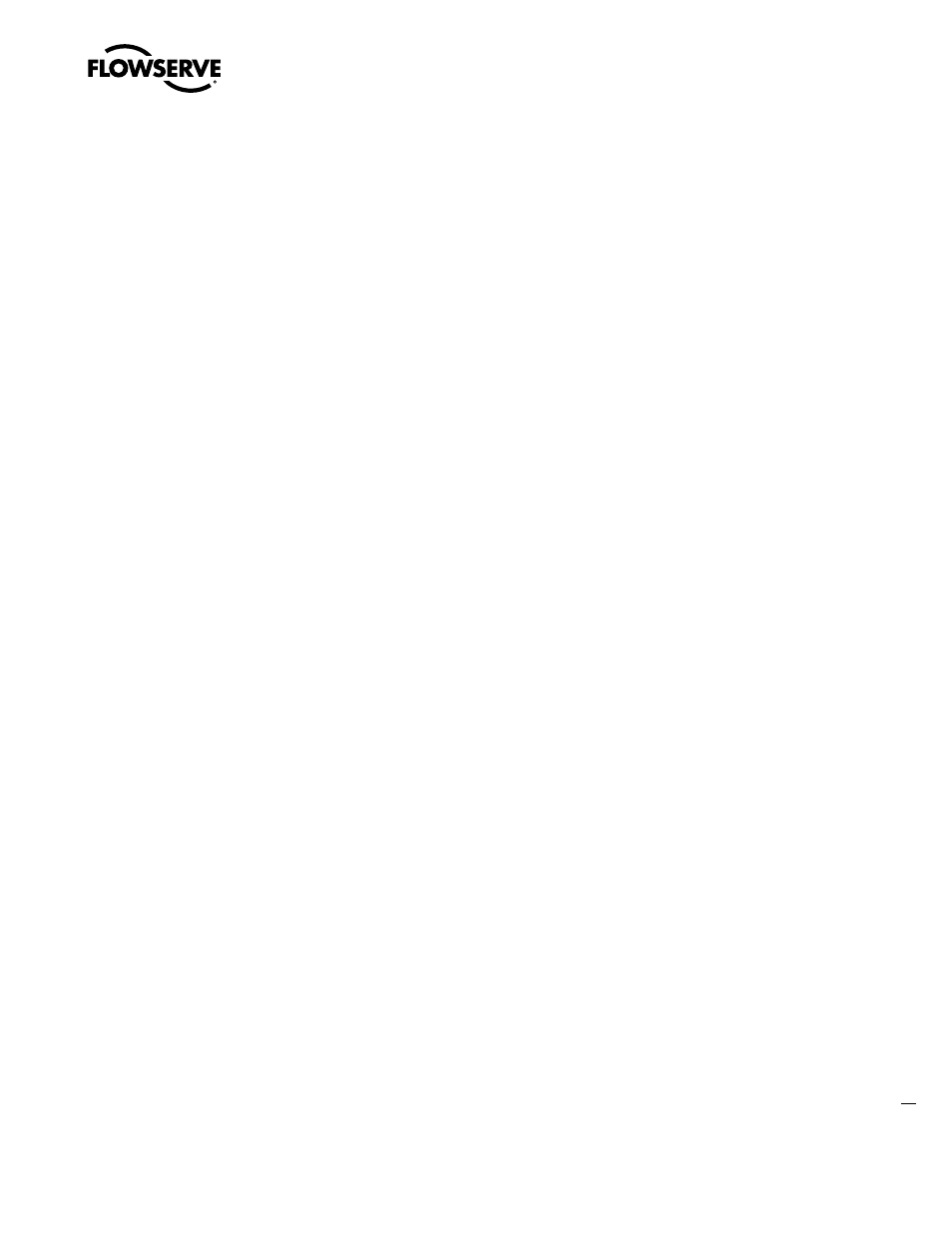
15
Nordstrom Figure 50165 and 50169 Dynamic Balance Iron Plug Valve FCD NVENIM2006-00 – 09/05
flowserve.com
Operation, Power Actuated Valves
Functionally, closure performance characteristics and backseating considerations are associated with all
valve types regardless of the means of operation. Satisfactory valve performance with power actua-
tion requires appropriate programming of the various requirements and constraints into the actuator
controls. Therefore, the actuator should be adjusted to deliver an adequate opening, running and closing
force to suit the anticipated service conditions. For position-sensitive valve types, the closing opera-
tion should be position controlled by external stops or limit switches. Be sure to consult the actuator
manufacturer’s operation manual for more detailed information.
Data required for selection and adjustment of power actuators should be delineated clearly in purchase
specifications for actuated valves. This data shall include but not necessarily be limited to:
a) Upstream pressure and differential pressure conditions at which both opening and closing shall
be required. Specify direction if applicable. Additionally, specify if valve operation is required under
high-flow “blow down” conditions.
b) Speed of operation required or the maximum time for opening and/or closing. Also, specify a
minimum time if required due to fluid dynamics.
c) Electrical power supply available (AC or DC voltage, phase, frequency) for electrical power actuators
or controls. Operating conditions for reduced voltages should also be considered.
d) Pneumatic pressure available for pneumatic actuators (cylinders or diaphragms). Also, specify
fail-open, fail-closed, fail-as-is, or any special requirements.
e) Requirements for position indication signals.
Actuator selection and adjustments should normally be made by NAI based on published literature
and/or technical advice of actuator manufacturer. NAI should be consulted when a manually operated
valve must be retrofitted with a power actuator.
a
Caution: Some valve actuators, when sized to provide specified loading, may have much
higher output at maximum switch or control settings and therefore be capable of damaging
valves if misadjusted. Valve and actuator manufacturer instructions should be followed closely
to prevent overloading valve stems, backseats and other structural parts. Successful operation
of power operated valves requires a diligent coordination of the skills and efforts of the valve
specifier, NAI and the actuator manufacturer. Most applications are problem-free, but miscom-
munication can lead to unreliable operation at one extreme and possible valve or actuator
damage at the other extreme.
Fluid Dynamics of Shutoff Valve Operation
A flowing fluid in a piping system has mass and velocity. Anything that causes a moving mass to
change its velocity will experience a reacting inertia force in proportion to the magnitude of the mass
and the rate of the imposed velocity change.
However, in the flow of gases the reacting inertia forces are inherently moderated by the compressibility
of the fluid that permits the instantaneous velocity change to be effectively limited to the mass of fluid
in the immediate vicinity. This, in addition to the self-cushioning capacity of the fluid column in the
upstream pipe, effectively precludes any significant problem of pressure surge in rapidly closed valves
in gaseous fluid piping.