Kammer control valves, Trouble-shooting chart – Flowserve 035 300 Series User Manual
Page 8
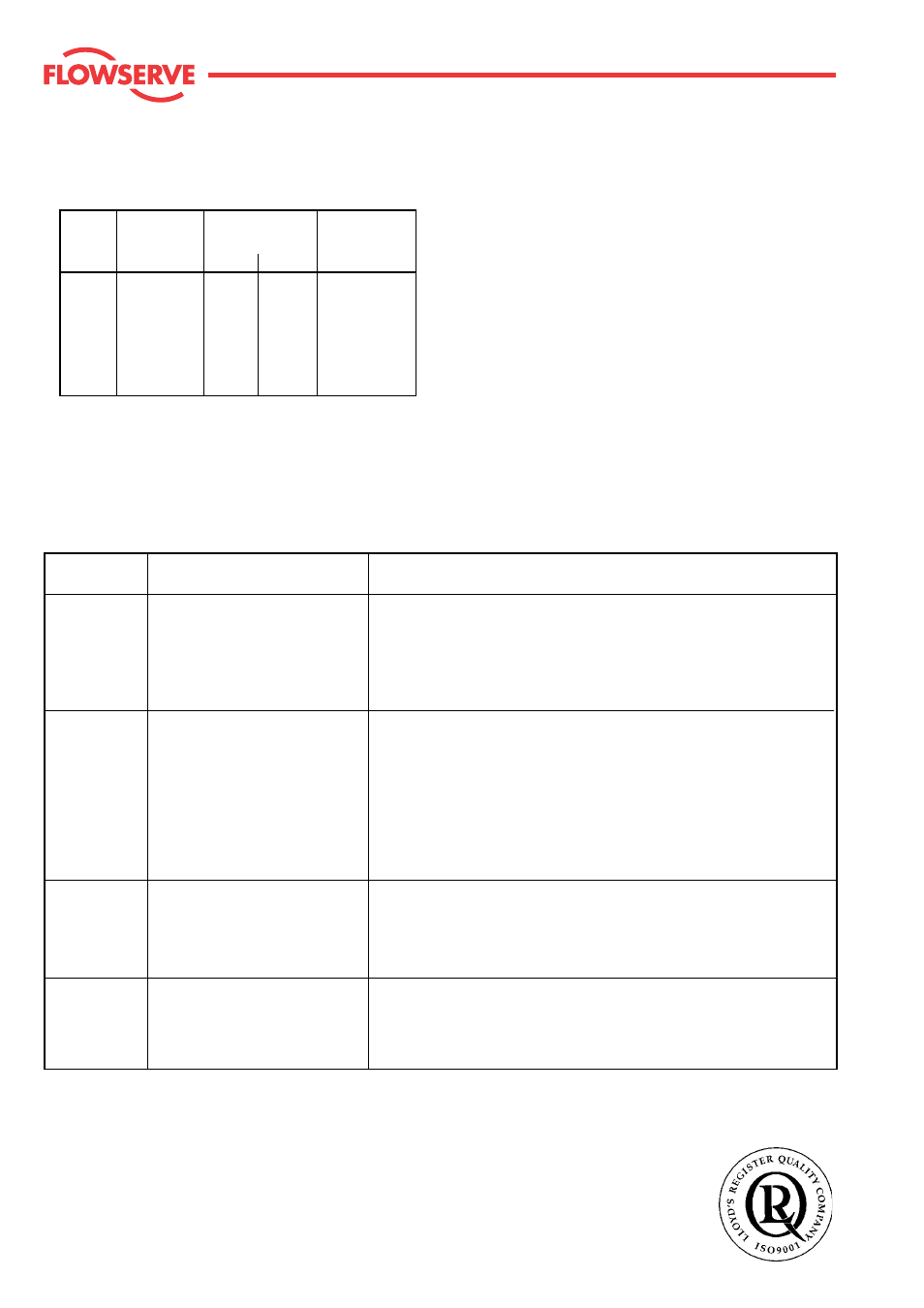
8
Flow Control Division
Kammer Control Valves
11.00
4.2.10 Using a torque wrench, gradually tighten all screws/
nuts to the prescribed torques (see following table),
alternating crosswise.
4.2.11 Replace packing by inserting packing rings one at a
time tapping each one down with a suitable bushing.
Hex bolt Waisted bolt
Studs
Thread
DIN 933
DIN 2510
DIN 939
A2-70
1.7709
1.7258
CK 35
M 8
20 Nm
–
–
–
M 10
35 Nm
–
–
20 Nm
M 12
60 Nm
44 Nm 36 Nm
35 Nm
M 16
145 Nm
115 Nm 92 Nm
80 Nm
M 20
280 Nm
–
–
–
M 24
250 Nm
–
–
270 Nm
IMPORTANT: ensure that the gaps in the packing
rings are distibuted evenly around the circumferance
in the packing box (gaps not in line).
Note:
different packings and fitting sequence is shown
in the spare parts list.
6.2.12 Insert packing follower. Fit gland nut for transport
purposes only. Gland nut to be fitted correctly and
tightened down when actuator is mounted.
4.2.13 When performing subsequent pressure test, note the
max. permissible pressure for the bellows. After the
check for leaks, close off test connection with plug or
suitable gauge.
Fault
Possible Cause
Remedy
Stem motion
1. Packing excessively tightened
1. Tighten gland nut slightly more than „finger-tight“
impeded
2. Operating temperature too
2. Note operating data and contact dealer
high for selected trim
3. Supply pressure inadiquate
3. Check system for leaks in the supply pressure or signal lines. Re-
tighten the connections, if necessary replace leaky lines
4. Positioner defective
4. See operating instructions for positioner
Excessive
1. Bonnet loose
1. See step 4.2.5 for correct tightening of bonnet.
leakage
2. Worn or damaged
2. Re-machine or replace seat ring/plug.
seat ring/plug
3. Gaskets damaged
3. Replace gaskets
4. Inadiquate actuator thrust
4. Check air feed. If air feed is OK, contact dealer.
5. Plug incorrectly adjusted
5. Correctly adjust plug according to step 3.2.4
6. Incorrect direction of flow
6. Check specification. Contact dealer
7. Handwheel incorrectly
7. Adjust handwheel
adjusted (acts like end stop)
Inadiquate flow
1. Plug incorrectly adjusted
1. Correctly adjust plug according to step 3.2.4
(short stroke)
2. Positioner defective
2. See operating instructions for positioner
3. Operating requirements
3. Check operating data. Contact dealer
too high
Plug slams
1. Plug adjustment incorrect
1. Correctly adjust plug according to step 3.2.4
2. Inadiquate supply pressure
2. Check supply pressure, seal leaks, remove blockage
3. Trim too large for
3. Replace trim
flow rate
Trouble-shooting Chart
Flowserve Essen GmbH
Manderscheidtstrasse 19
D - 45141 ESSEN
Tel.: +49 (0) 201 89 19 - 5 • Fax: +49 (0) 201 89 19 - 600
All data subject to change without notice
©09.2000 Flowserve Corporation. Flowserve and Kämmer are trademarks of Flowserve Corporation