Flowserve V901 VariCool Desuperheater User Manual
Page 3
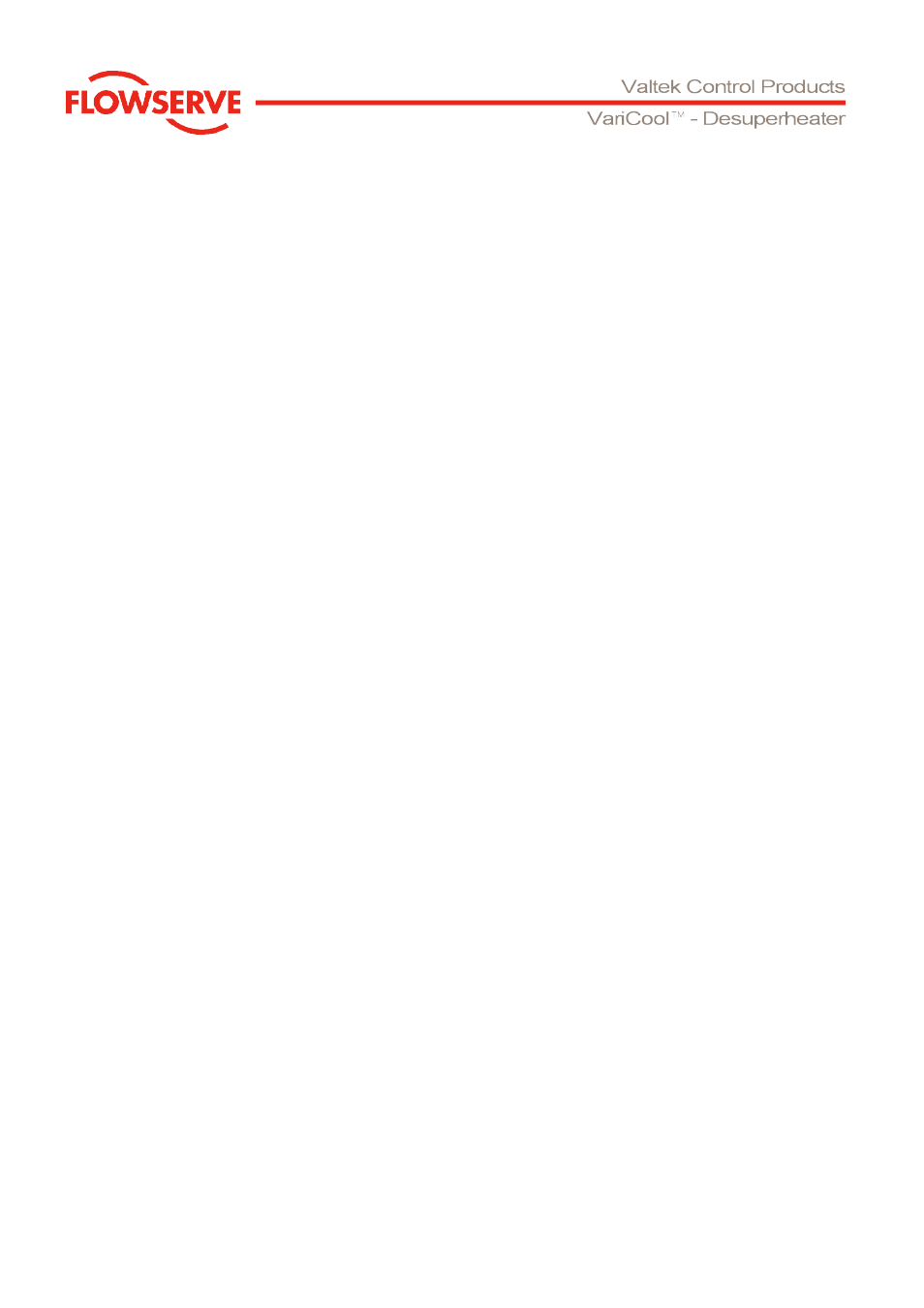
- 3 -
Application
Injection control valve for direct steam cooling applications. In combination with a SCHMIDT
multispring or central spring pneumatic actuator, optionally also with an electrical linear or rotary
actuator, can be controlled. Suitable for a wide range of applications due to simple design and
adaptability to different processes.
1 VARICOOL operating instructions
1.1 Installation
The device may only be assembled and put into service by qualified personnel. Qualified
personnel are persons who are familiar with the assembly, commissioning and operation of
this product and have the respective qualifications to perform these activities.
1.2 Delivery status
The SCHMIDT injection nozzle valves are delivered with assembled and calibrated
actuators. They are provided with a protective coating, any shiny parts are greased and the
body openings are provided with blanking plugs. The greatest care must be taken against
knocks or sudden movements during loading and transport, as the lifting appliances must
be attached without pressure on the stem and the position indicator by means of a rope
sling below the actuator mounting flange. Any damage of the corrosion protection during
transport must be remedied immediately. At the construction site, the injection nozzle valves
must be protected against the effects of weather, grime and other damaging influences by
being placed on a firm base in a closed room until required for installation. The blanking
plugs attached for protection of the flange and interior of the control valve may only be
removed at the installation site.
1.3 Installation recommendation
The successful employment of the injection nozzle valve depends directly on a suitable
design of the converting station. As the function of the converting station depends greatly on
the consideration of the physical possibilities, it is recommended to observe the stated
standard values. Deviations may lead to considerable fluctuations in the control loop for
which the nozzle valve manufacturer rejects any liability whatsoever. In borderline cases, an
expensive conversion of the steam converting station should be expected. Even though the
complex physical processes may in individual cases justify a deviation from the standard
values, this requires, however comprehensive system knowledge and the express approval
of the manufacturer.