3 motor operation, 4 torque and travel limiting – Flowserve L120-190 through L120-2000 User Manual
Page 23
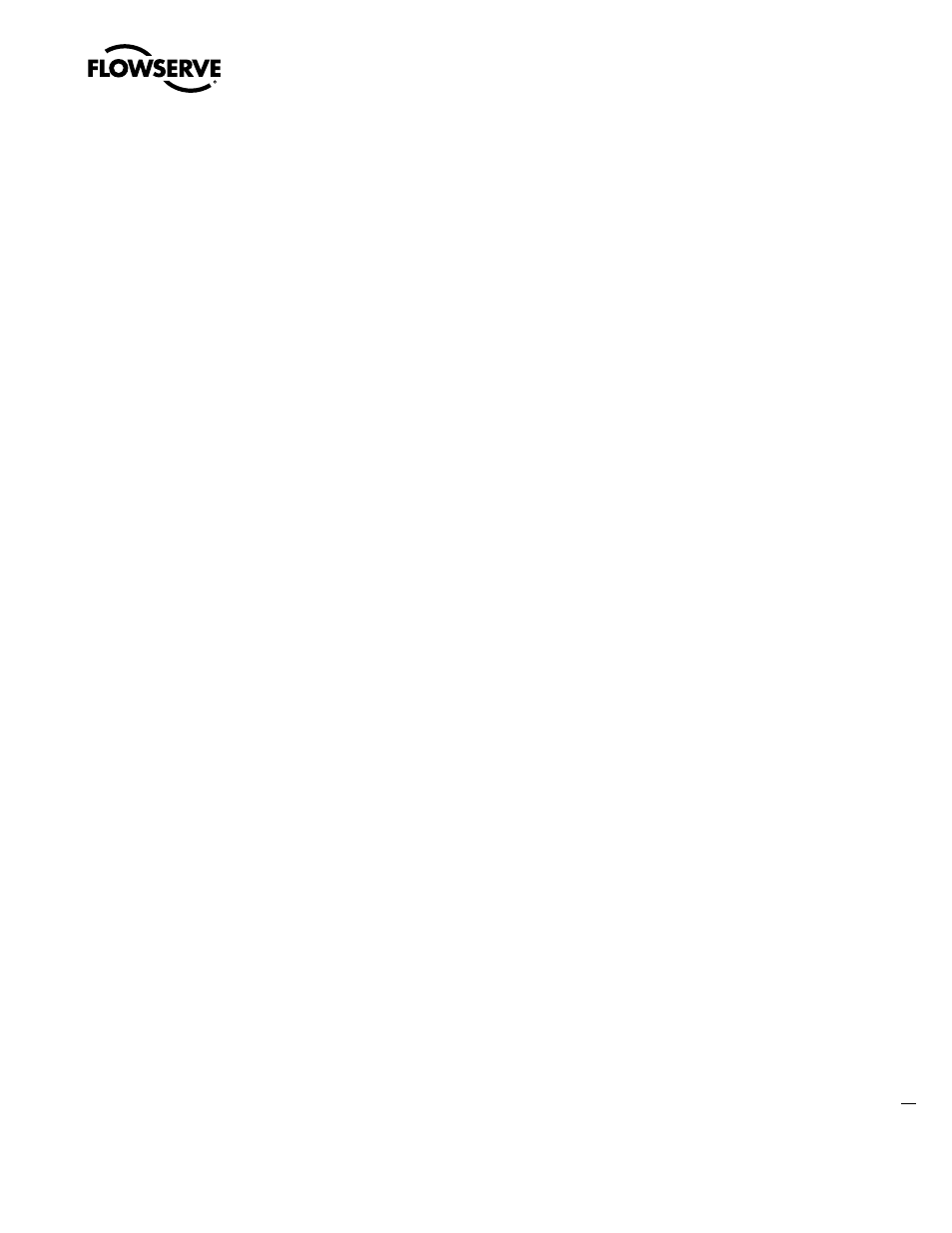
23
Limitorque
®
L120-190 through L120-2000 FCD LMENIM1203-00 – 10/11
flowserve.com
6.3 Motor Operation
The actuator is always available for motor operation whenever the motor is energized.
a
CAUTION: Do not force the declutch lever into motor operation. Lever will automatically return
to motor operation when the motor is energized.
Reset the travel limit switches prior to motor operation if the actuator has been dismantled or removed
from the valve. Piece numbers refer to Figures 8.1, 8.2, and 8.3 for L120-190 and -420, and Figures 8.4,
8.5, and 8.6 for L120-800.
In motor operation, the Motor Pinion (piece #31) drives the Worm Shaft Gear (piece #32), which drives
the Worm Shaft Clutch (piece #33) through the clutch lugs on both the worm shaft gear and the clutch.
The Worm Shaft (piece #17) is driven by splines on the OD of the worm shaft and on the ID of the
clutch. The worm shaft is splined to the Worm (piece #30-1) which drives the Worm Gear (piece #13).
Two lugs on the worm gear are engaged by matching grooves in the Drive Sleeve (piece #8). This
arrangement provides the no-lost-motion mode of operation and allows the worm gear to turn the
drive sleeve. The worm gear lugs may also be oriented outside the grooves to give the lost-motion
or hammerblow effect. The Stem Nut (piece #12) is rotated by internal splines on the ID of the drive
sleeve and external splines on the OD of the stem nut. This causes a threaded stem to translate in a
threaded stem nut and a keyed shaft to rotate in a keyed stem nut. Thrust is absorbed by Bearings
(piece #40, #41, #14, and #67 ) located at the top and bottom of the drive sleeve.
6.4 Torque and Travel Limiting
Unless otherwise stated, piece numbers refer to Figures 8.1, 8.2, and 8.3 for L120-190 and -420, and
Figures 8.4, 8.5, and 8.6 for L120-800.
The Geared Limit Switch (piece #305 of Figure 8.6) is driven directly by the worm shaft gear through the
limit switch pinion. Thus, the limit switch is directly connected to the output of the actuator and, once
properly set, remains in step with the valve position regardless of the electric or manual operation of the
actuator.
As the actuator increases torque, the worm and the Torque Spring Cartridge Assembly
(composed of piece #'s 16-1 through 16-8) move axially along the worm shaft, compressing the disk
spring packs. The torque spring assembly is calibrated such that a finite spring compression relates to
a finite output torque. Axial worm movement causes movement of the bearing cartridge that is geared
to the Torque Switch (piece #300). The torque switch is graduated and adjustable so it may be set to
interrupt power to the motor at a predetermined output torque level.