Worcester actuation systems – Flowserve 10-40 39 ACCESS M Mounted Limit Switch User Manual
Page 2
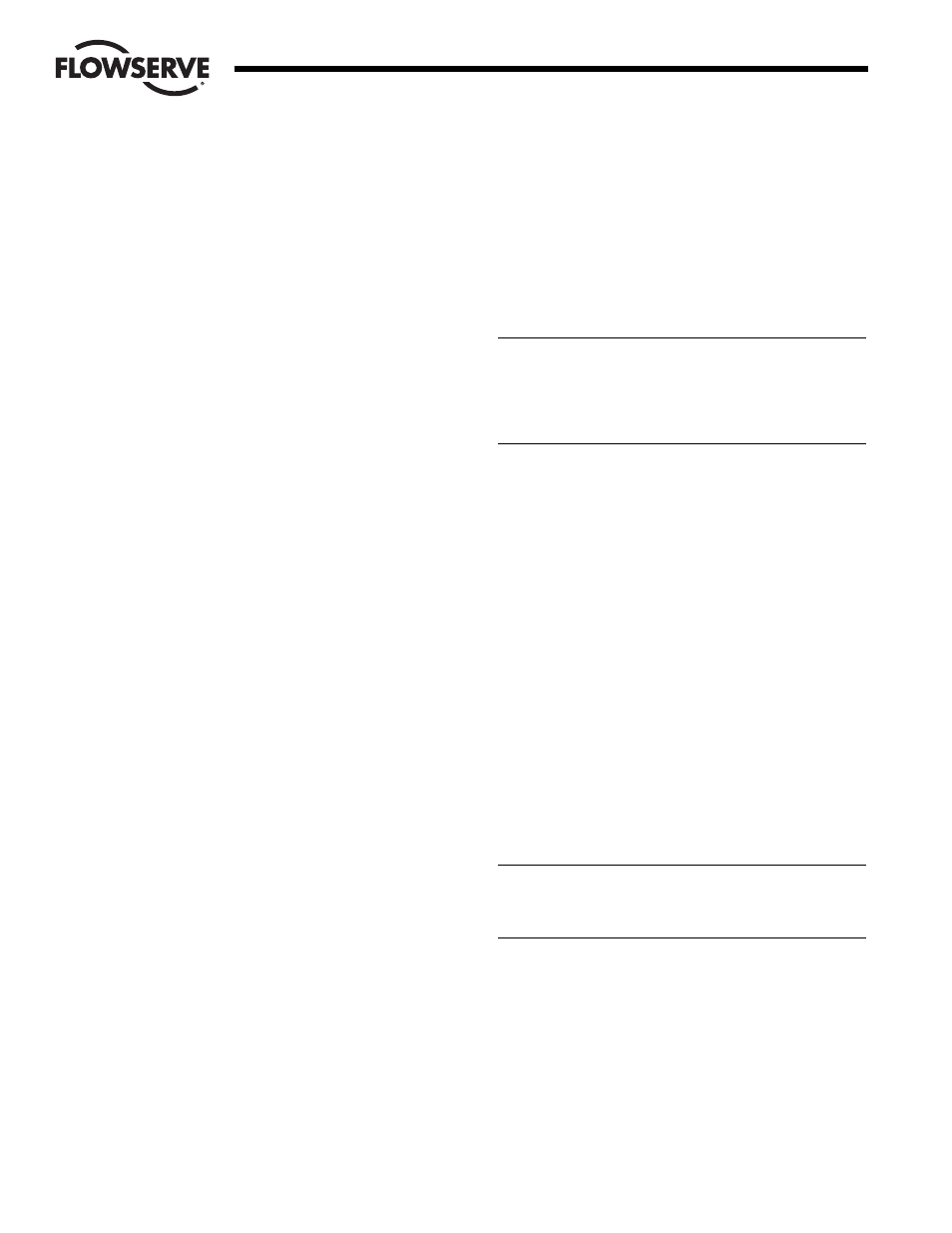
14848-A
2
The customers field connections to the circuit board take place on
terminal block P3 as follows:
Terminal 1 - Bus negative from 24 VDC supply
(Next to the P3 label)
Terminal 2 - CanL signal
Terminal 3 - Bus Shield
Terminal 4 - CanH signal
Terminal 5 - Bus positive from
24 VDC supply
The switch/sensor connections are made to the terminal block labeled
as P2. Terminal 1 is located next to the P2 label. The switches/sensors
are wired to the terminals such that terminals 1 & 2 are for SW2, and
terminals 3 & 4 are for SW1. Positive 24 VDC is provided on terminals
1 & 3 to the switches and the switch returns connect to terminals 2 &
4 respectively.
The solenoid connects to terminal block P4 terminals 3 & 4. Positive
24 VDC is supplied to the solenoid coil from terminal 3 and the
solenoid coil return is connected to terminal 4. The solenoid is
energized by turning on a transistor which connects the return to
ground. Should it be necessary to operate a second 24 VDC 3 watt
device from terminals 1 and 2, terminal 2 is the positive supply and
terminal 1 is the return.
The circuit board has three 10 position rotary switches on board
(SW1, SW2, and SW3). SW1 and SW2 are used to set the MACID of
the board (i.e., address), with SW2 used for the most significant bit
and SW1 used for the least significant bit, e.g., for a MACID of 35,
SW2 would be set to 3 and SW1 would be set to 5. Valid MACID
values range from 00 to 63. A none-valid MACID setting on the
switches allows the MACID to be set through software.
SW3 is used to set the DeviceNet baud rate. Valid baud rate selections
are 125k, 250k, and 500k. SW3 position 0 represents 125k, SW3
position 1 represents 250k, and SW3 position 2 represents 500k. If
the SW3 position is set to an invalid setting it permits the baud rate to
be set through software.
NOTE: WHENEVER THE BAUD RATE AND/OR MACID IS CHANGED
VIA THE SWITCHES, THE BOARD POWER MUST BE CYCLED IN
ORDER FOR THE CHANGE TO TAKE EFFECT.
For additional information see Installation, Operation & Maintenance
Supplements 1, 2 and 3 that accompany this product.
When shipped for field installation, the limit switch (proximity
sensor)/solenoid assembly will be broken down into sub-
assemblies. The sub-assemblies are: (1) the switch (proximity
sensor) operator assembly, consisting of the switches (sensors),
bracket, springs and buttons; and (2) the enclosure (housing),
probes, solenoid, control block, block gasket, P.C. board and cover.
Hardware items and gasket are packaged separately. Retaining rings
and “O-Rings” shall be assembled.
NOTE: Access M Mounted Limit Switch (proximity sensor)/Solenoid
Kits fit only Revision R5 and later 39 Actuators. Included in the
Access M Mounted Limit Switch (proximity sensor)/Solenoid Kits is a
Rebuild/Accessory Addition Label which is to be marked and applied
to actuator after switch has been installed.
1. The Access M mounted limit switch (proximity sensor)/solenoid
assembly will be mounted on the right hand end cap (when
viewed from actuator nameplate) with conduit connection on the
right side of the housing (when viewed from the cover side of the
switch).
CAUTION: When actuator is installed in outdoor conditions,
water can enter the exhaust hole(s) of the control block and
then freeze. Worcester/McCANNA suggests a cover be used, or
mount the actuator such that the block exhaust hole(s) will not
fill with water.
The “standard” mounting configuration of the 39 actuator to the
valve is fail closed. In this configuration, SW-1, as described in
Section 7 and in the wiring diagram, will give indication when the
actuator is in the open position (Green LED is on). SW-2 gives
indication of the closed position (Red LED is on). Actuator shaft
rotation will vary, depending on which fail closed mounting is
used. See Section 8 for appropriate wiring diagram.
NOTE: The rotation of the actuator shaft CW (clockwise) or CCW
(counter-clockwise) is determined when viewing the actuator from the
nameplate side of the actuator, while being able to read the label from
left to right.
Fail open mounting configuration may be obtained by either
inverting the actuator, using in-line coupling, or mounting the
actuator cross-line (sizes 10-20) or indexing the coupling
(including valve ball and stem) 900 to the actuator shaft (sizes
25-40). In these cases SW-1 & SW-2 indication will be reversed
from the above but actuator shaft rotation will vary, depending on
which fail open mounting is used. Wiring shall be done per the
appropriate wiring diagram in Section 7 and adjustments per
Section 6.
2. Remove cover from enclosure.
CAUTION: The longer probe must be in the left hand through-
hole looking at the housing from the cover side. (Both probes
are the same length for the 1039 ACCESS only!).
3. Assemble the enclosure, with probe assemblies, to the actuator
inserting the housing gasket between the actuator end cap and
the housing. Important! Do not apply any grease to the gasket, it
must be installed dry. Secure with 4 machine screws. For all
ACCESS M units, 4 threaded tamper proof plugs are installed over
the machine screws. Once installed no attempt should be made to
remove these plugs. If it becomes necessary to remove enclosure
from actuator end cap, consult Worcester Controls/McCANNA.
Check the probes for freedom of movement by moving them back
and forth slightly.
Flow Control Division
Worcester Actuation Systems