Esp-dc, Electronic servo positioner – Flowserve ESP-DC Electronic Servo Positioner User Manual
Page 2
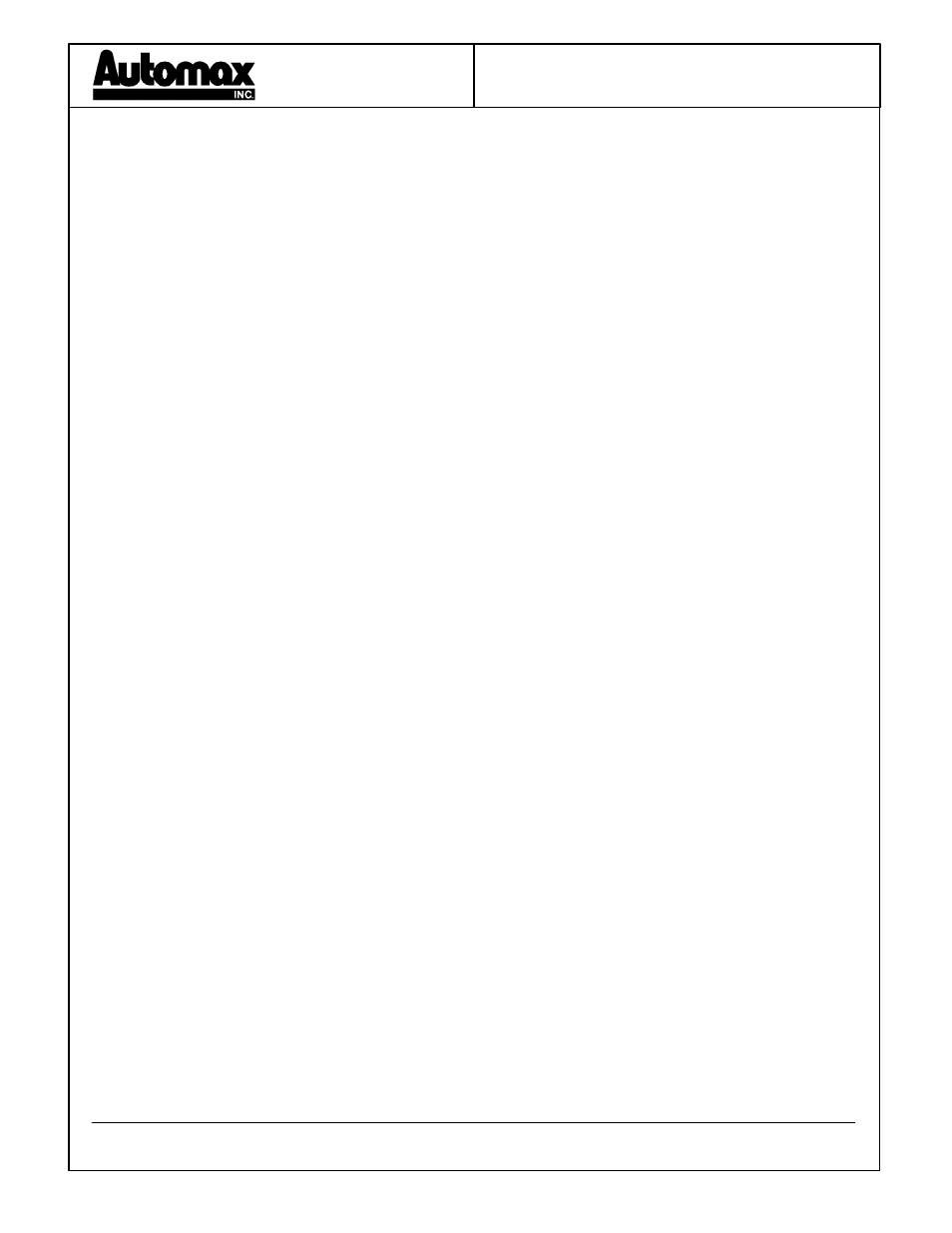
Valve Alignment and Servo Calibration
1
Connect DC power to terminals marked '+' and
'-' to junction block J3. The DC power supply
should be the same voltage as the actuating
motor (12 or 24 Vdc).
2
Safety overtravel switches disconnect the
motor if the actuator overtravels approximately
5 degrees past the full CW or CCW position.
On valves with mechanical stops, the safety
overtravel switches need to be set so that the
motor will disconnect prior to hitting a
mechanical valve stop. See note 3 under
"Trouble Shooting" on page 3 before
adjustment.
3
Minimum Position Adjustment:
Apply minimum input signal to ESP-DC terminals
+IN and -IN and adjust zero 'Z' potentiometer
until actuator stops at full CW* position and
CW*
*
LED turns off. Turn the 'Z' adjustment CW
to move actuator CW* .
4
At the minimum signal position, the voltage from
test point TP1 to TP5 should be approximately
0.15 Vdc. If not, see note 4 under "Trouble
Shooting".
5
Maximum Position Adjustment:
Apply maximum input signal to ESP-DC and
adjust span 'S' potentiometer until actuator
stops at full CCW* position and CCW* LED
turns off. Turn the 'S' adjustment CCW to
move the actuator CCW.
6
Due to zero-span interaction, repeat steps 3
and 5 until actuator positions repeat at both
ends of travel (usually 2 to 3 times).
SPEED and TORQUE adjustments
1
T
he SPEED potentiometer can be adjusted to
increase (CW) or decrease (CCW) the Speed
of the actuator.
2
The TORQUE potentiometer can be adjusted to
Lower (CCW) or Raise (CW) the maximum
torque output of the actuator before a FAULT
condition occurs. The factory setting is full CW
(maximum Torque).
ESP-DC Transmitter (optional)
Note: If the ESP-DC Transmitter is used, the valve
alignment and servo calibration must be completed
with the 4-20mA transmitter installed. Servo
calibration should be performed before transmitter
calibration.
1
Connect 4-20mAdc output leads to transmitter
terminals marked '+' and '-'.
2
For 90
`
operation, the two jumpers on the
transmitter should be set to connect pins 1 and
3 , and pins 2 and 4. For 180
`
rotation, the
jumpers should connect pins 1 and 2, and pins
3 and 4.
3
Drive actuator to the full CCW position and
adjust 'S' span adjustment of the ESP-DC
Transmitter for 20mA output.
4
Drive actuator to the CW position and adjust 'Z'
zero adjustment of the ESP-DC Transmitter for
4mA output.
5
Repeat steps 3 and 4 until the desired output is
achieved at both positions. If there is difficulty
achieving the desired range, see note 4 under
Trouble Shooting on page 3.
6
Standard ESP-DC Transmitters are direct
acting.
Important Notes About Reverse Acting
ESP-DC with Transmitter
N
ote: Reverse acting transmitter means a 4mA
output for full CCW, and a 20mA output for full
CW position.
7
If you are using a positioner that is not factory
calibrated for reverse acting with a transmitter,
you will need to order an Adapter Kit #108921.
8
If you have specified a reverse acting ESP-DC
with a transmitter, JP2 is to be set on the 'D'
right position.
A
The feedback potentiometer voltages as
measured from test points TP1 to TP5 on
the ESP-DC card are as follows:
FULL CCW
~ 0.15 Vdc
FULL CW
~ 1.42 Vdc
The drive LED's will now indicate the opposite of
the actual drive travel.
*
For Reverse acting, the CW and CCW directions marked with a * are reversed.
B00156-0
Page: 2 of 4
11444 Deerfield Road
Cincinnati, Ohio 45242
(513) 489-7800
FAX (513) 489-5243
ESP-DC
Electronic Servo Positioner