Esp-dc, Trouble shooting, Electronic servo positioner – Flowserve ESP-DC Electronic Servo Positioner User Manual
Page 3
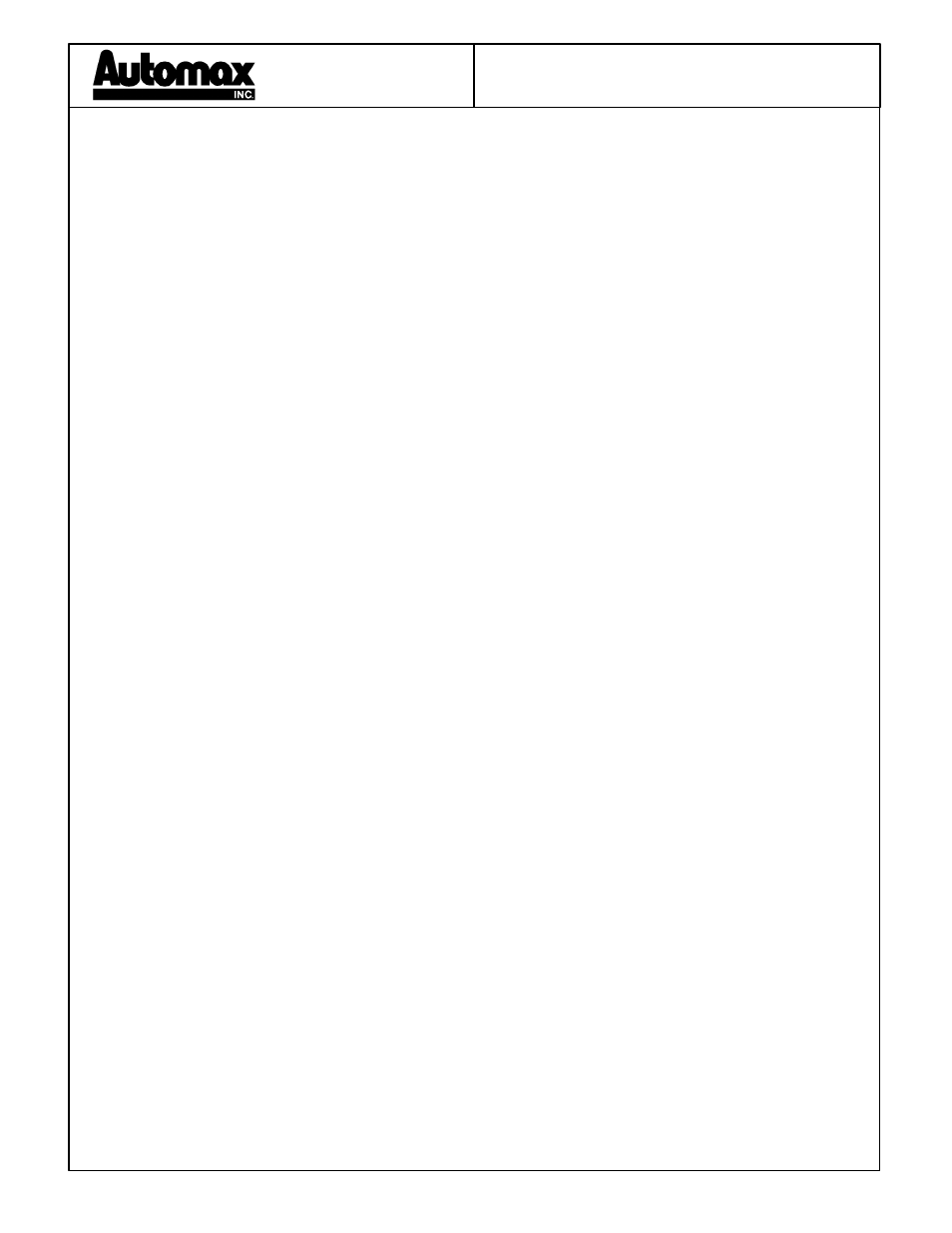
Trouble Shooting
Note: All of the Test Point voltage
measurements are taken in reference to test
point TP5 labeled "REF."
1
Actuator does not respond to the input signal.
A
Verify proper input configuration and signal
polarity connections. Measure voltage at
TP4 and verify it's in the range .4 to 2.0 Vdc.
B
Verify the proper power connections. Refer
to the schematic on page 4.
2
Actuator does not travel when CW or CCW
LED is lighted.
A
Check the safety overtravel cams and
overtravel switches, and adjust as needed
(see note 3).
B
If actuator exceeds full CW or CCW
positions, check the feedback potentiometer
voltage (see note 4).
3
Safety overtravel switches need adjustment.
Note: On valves with mechanical stops, the
safety overtravel switches must be set so that
the motor will disconnect prior to hitting the
mechanical valve stops.
A
Disconnect the actuator power connector J1
from the ESP-DC.
B
Drive the motor to 5 degrees past full CW by
placing DC power directly on the terminal of
the actuator electric motor. To drive the
motor CW, place +DC on the terminal with
the red wire.
Be careful not to drive the
actuator into any mechanical stops. This
may damage the actuator and the valve.
Set the CW cam so the overtravel switch
trips.
C
While setting CW safety overtravel switch,
ensure a voltage between 0.10Vdc and
0.20Vdc is measured at test point TP1
when switch is tripped. Otherwise see note
4 in this section.
D
Drive the actuator CCW until approximately
5 degrees past the standard full CCW
position by applying power to the motor
terminals, this time with the opposite polarity
from B. Adjust CCW cam (bottom) until
switch trips.
4
With the actuator in full CW position, the
feedback potentiometer voltage
should read
approximately 0.15 Vdc at TP1. If the feedback
potentiometer is not set correctly, the "dead
spot" at the end of the pot's rotation may cause
over/under travel or a lack of transmitter range.
A
Loosen potentiometer drive gear and rotate
potentiometer until approximately 0.15 Vdc
is measured at TP1, and then re-tighten
drive gear.
B
Recalibrate ESP-DC Zero and Span
adjustments, starting with Step 3 on page 2.
5
Actuator is oscillating or is not responsive to
small input changes, the Dead Band 'DB'
potentiometer may need adjusting.
A
Drive actuator to mid position and turn DB
CCW until both LED's energize, then
immediately turn CW until both LED's
de-energize. Turn adjustment CW an
additional 1/4 turn and operate actuator over
full range in small increments to check
operation. Voltage from test point TP2
should measure approximately 0.10 Vdc.
6
The FLT LED is lit and the actuator won't move:
The FLT LED indicates a FAULT condition,
where the actuator is drawing too much current.
Check the TORQUE potentiometer setting,
turning CW to increase the FAULT current limit,
Drive the actuator in the reverse direction to
reset . If this doesn't work, there may be an
obstruction in the valve.
7
Special precautions for operating the ESP-DC.
A
It is always necessary to limit actuator from
repeated safety overtravel switch trippage.
B
Always remove DC power to actuator, prior
to removing input signal, and apply signal
prior to applying DC power to actuator.
B00156-0
Page: 3 of 4
11444 Deerfield Road
Cincinnati, Ohio 45242
(513) 489-7800
FAX (513) 489-5243
ESP-DC
Electronic Servo Positioner