9 check source and ack/fail switches, 10 analog inputs, 11 analog output – Fluke Biomedical 960SF-220 User Manual
Page 12: 12 high voltage power supply
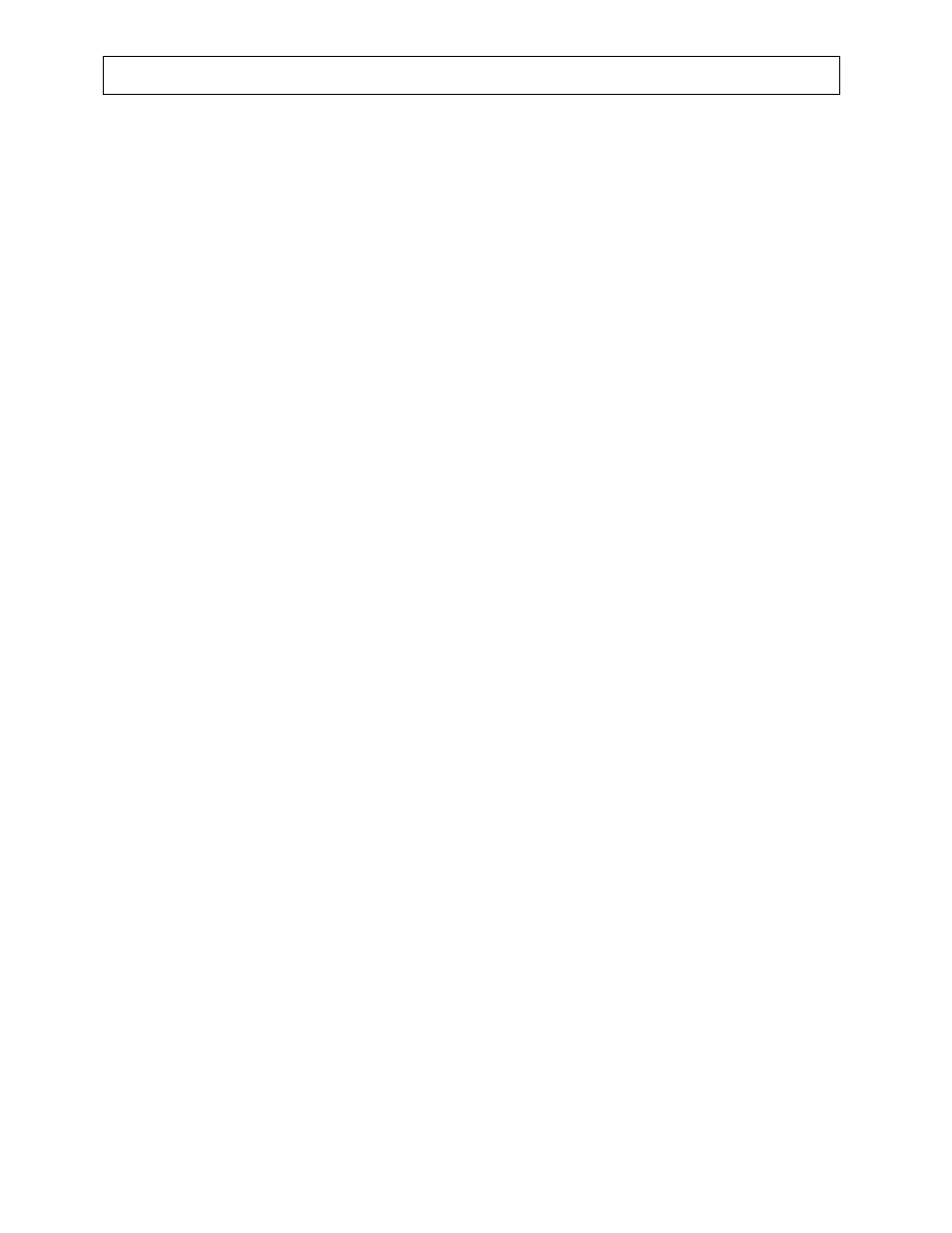
Victoreen 960SF-220,221,230,231
Operators Manual
2-4
2.9 CHECK SOURCE and ACK/FAIL Switches
CHECK SOURCE is a front panel momentary switch which, when pressed, causes the check source in
the detector to move in front of the detector. The ACK/FAIL switch is a momentary switch used to
acknowledge an alarm or warn condition. When the microprocessor flags an out-of-limits operating
condition, the operator can press the ACK/FAIL pushbutton to acknowledge the alarm. Since the out-of--
limits conditions which can be acknowledged by the microprocessor are firmware dependent, refer to the
operation section of the system manual to find out the additional alarms, other than WARN and ALARM,
that the ACK/FAIL pushbutton is used to acknowledge.
There are four indicator lights, controlled by the associated controller labeled ALARM, WARN, ACK/FAIL,
and CHECK SOURCE. The ACK/FAIL and CHECK SOURCE indicators are also pushbuttons and
provide a way to communicate with the controller. A HIGH VOLTAGE adjustment provides operator
control over the remote detector high voltage supply from the module. A TEST INPUT jack and an
associated TEST/NORM switch permits selection of a simulated detector signal for testing the module.
Normally the C/S Flip-Flop-flop is reset and the CHECK SET signal is low. When an operator pushes
SW4, he sets the C/S flip-flop and the CHECK SET signal becomes high (active) to cause the C/S
reading. FAIL SET will become active (high) if SW3 is pushed because the FAIL Flip-Flop is set.
2.10 Analog Inputs
This description applies only for the 960SF-220-10 Scaler and the 960SF-230-10 Scaler. There are four
0-10 V analog inputs that are converted to digital. These four analog signals are multiplexed by Z17 and
the signal to be converted is picked by decoding D0 and D1. CH2 (SIGNAL 2) is an optional high voltage
monitor-using jumper W15. Z8 is a 12-bit converter. Z9 and Z10 are READ ONLY registers. Digital data is
clocked into Z9 and Z10 upon end of conversion. They are read when READ 2 and READ 4 are active
(low) respectively.
2.11 Analog Output
Z11 is an 8-bit D/A converter and latches input data when WRITE 3 is active (high). R126 is ZERO
ADJUST and R127 is GAIN ADJUST. R126 sets the low limit and R127 sets the upper limit of the output.
DAC output goes into the input of Z2. Z2, Z3, and associated circuitry comprise the 4-20 mA analog
output. Feedback divider R23 and R24 insure load independent output to a maximum load impedance of
500 Ω.
2.12 High Voltage Power Supply
The scaler provides an adjustable high voltage power supply of 400 to 1800 V at 1 mA. R8 is the HIGH
VOLTAGE ADJUST driving Z4 that drives Q7. Q7drives the oscillator circuitry Q6, Q4 and T1 that
generates high voltage pulses rectified by bridge CR5, CR6, CR8, and CR9. This high voltage is divided
by a ratio of 300:1, then buffered by voltage follower Z39 that is fed back to the input of Z4 as feedback
for regulation. TP3 is the test point used to measure the scaled down voltage value. There is also an
ERROR input originated by an americium regulator (separate optional external module) that is fed into the
high voltage circuit at Z4 pin 3 to regulate high voltage when system gain needs to be changed. 960SF-
230 and 960SF-231 are configured for negative high voltage output.