TE Technology TC-36-25-RS232 User Manual
Page 25
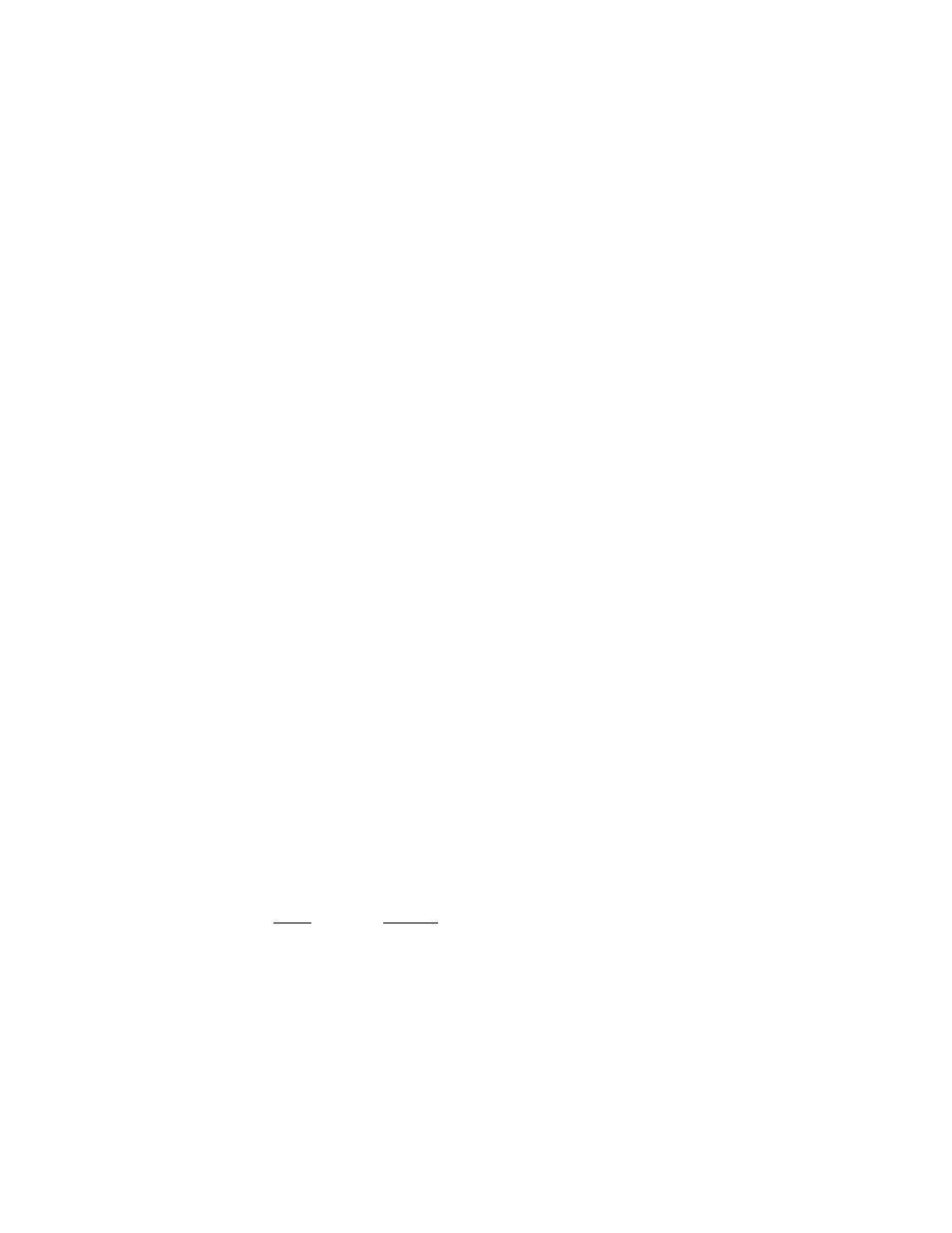
3.3
PROPORTIONAL BANDWIDTH:
The acceptable bandwidth values that may be entered are (1 to 100) degrees.
The proportioning bandwidth is the temperature span over which the output power is proportioned from -100% to
+100%. The bandwidth is centered about the temperature set point, and once set the proportional output will
vary as the actual temperature moves through the bandwidth range. That is, the controller output is +100% at the
end of the bandwidth range above the set point, it decreases to 0% power as it reaches the set point, and then
reverses to -100% as it reaches the end of the bandwidth range below the set point.
For example, suppose the controller is being operated in the cooling mode, the set point is 10.0 °C, and the
bandwidth is set to 5 °C (with INTEGRAL GAIN and DERIVATE GAIN both set to zero). The controller will be at
+100% output until the temperature cools to 12.5 °C. Power then starts to proportionally decrease as the sensor
temperature is cooled below 12.5°C. The power will be reduced to 0% when the sensor is at 10.0 °C. Finally, the
power will reverse polarity and proportionally increase to -100% if the sensor temperature decreases to 7.5°C.
If the bandwidth is set too narrow, the temperature will oscillate around the set point. If the bandwidth is too
wide, the controller will be slow to respond or may never reach set point.
3.4
INTEGRAL GAIN:
The acceptable values that may be entered are (0.00 to 10) repeats per minute.
With just proportional control, the controller’s output is, by definition, 0% when the actual temperature reaches
the set temperature. Because some non-zero output power level is almost always required to reach the set point,
using only proportional control will not allow the controller to maintain a desired set point. Therefore, introducing
an integral gain allows for an output amount other than 0% when the actual temperature reaches the set
temperature. It essentially shifts the output power to the average level required to maintain the desired set point.
For example, suppose the set temperature is 10.0 °C, the bandwidth is set to 5 °C, and the controller settled to a
constant 11.2 °C (corresponding to 48% power with only the proportional bandwidth active).
In this case the “error”, or difference in temperature between the set point and actual temperature, is 1.2
°C.
From the example in section 3.3 we know that the proportional output will change by 40% for every 1 °C
change in the error (this is bandwidth gain of 40 % per °C).
Let’s assume the integral gain is activated by changing its setting from “0” to “1 per minute”.
The integral function will now ramp the output at a rate determined by the error signal, the proportional
bandwidth gain, and the integral gain. The rate is determined by multiplying the error, the bandwidth gain, and
the integral gain. In this case, if the integral control is set to 1 repeat per minute, the controller will increase the
output power at a rate of 48% per 1 minute.
This output % is updated continuously. Of course, the maximum output is limited to +100% and the minimum is
limited to -100%.
If the integral gain is set too high, the temperature will oscillate. If integral control is set too low, it will take a long
time for the temperature to settle to steady state.
minute
/
48%
minute
1
C
1.2
C
40%
=
∗
°
∗
°
25