Troubleshooting, Function descriptions, Overvoltage regulator – Yaskawa A1000 AC Drive User Manual
Page 10
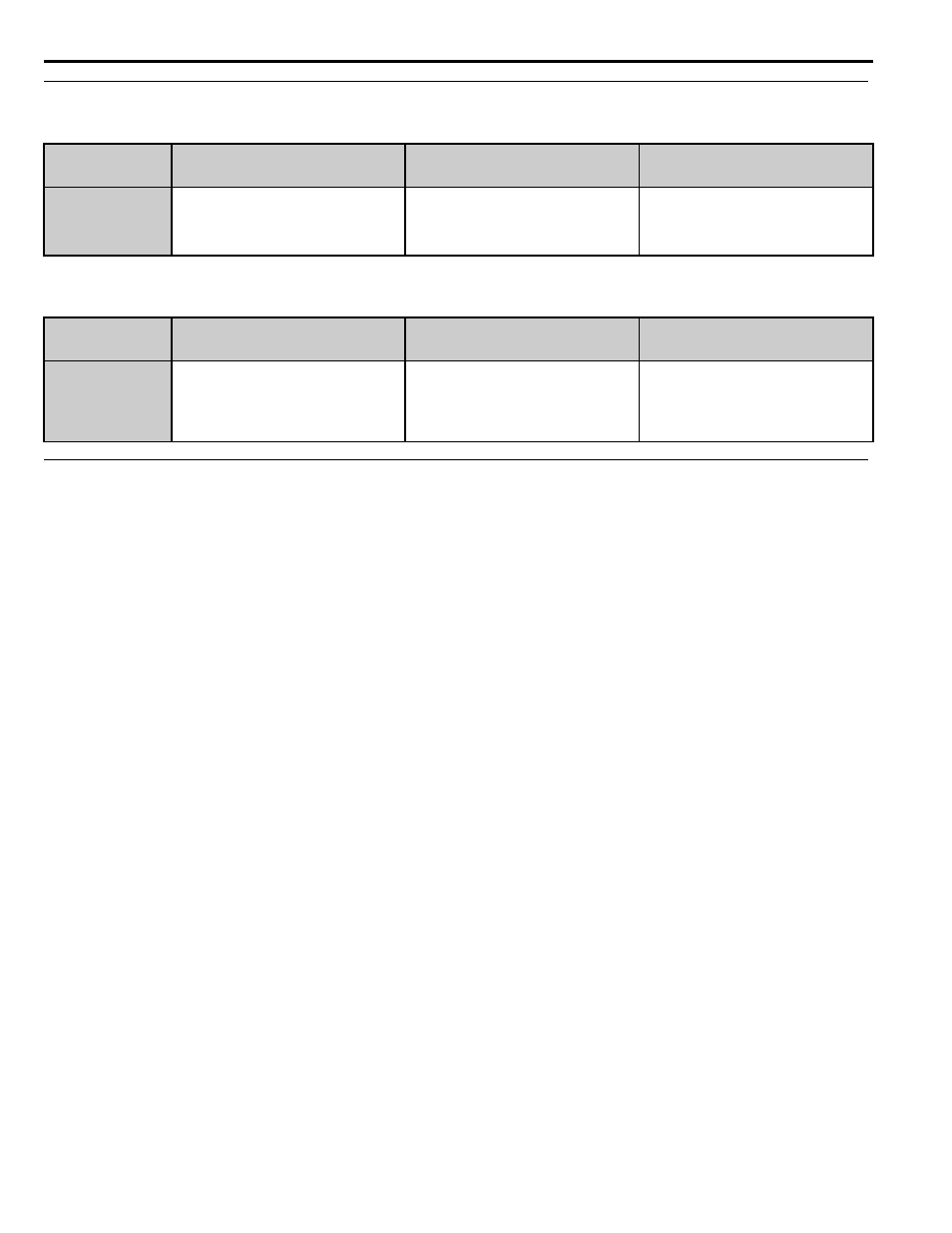
2 Overvoltage Suppression A1000 Custom Software
10
YASKAWA TM.A1000SW.062 Overvoltage Suppression A1000 Custom Software Supplement
Troubleshooting
Table 7 Fault
Table 8 Alarms
Function Descriptions
Overvoltage Regulator
The motor torque-producing current is detected and subtracted from the OV Regulator setpoint (P1-01). The result (error)
is run through the OV Regulator PI controller. The PI controller will add frequency to the frequency reference in order to
maintain a constant Iq setpoint. The PI controller will NOT subtract frequency from the frequency reference. This is done
to keep the torque producing current positive (motoring) thus preventing regeneration and subsequent overvoltage faults
(OV). This eliminates the need for a dynamic braking resistor package.
Optimizing Performance when Using Open Loop Vector Control
In order to obtain optimal performance when using the Open Loop Vector control method (A1-02 = 2), a motor auto-tune
should be performed. Ideally, the motor should be uncoupled from the load, and a Rotational auto-tune (T1-01 = 0) should
be performed.
If the motor cannot be uncoupled from the load, then a Stationary auto-tune (T1-01 = 1) should be performed. In this
software, Motor Rated Slip and Motor No-Load Current are not calculated in the Stationary auto-tuning method.
Therefore, these need to be calculated and manually entered prior to running the Stationary auto-tune. After entering the
E2-02 and E2-03 values, perform the auto-tune.
Motor Rated Slip (E2-02) should be calculated as follows:
Example: 4-pole, 60 Hz motor, Motor Rated Speed = 1730 RPM
E2-02 = (Motor Synchronous Speed - Motor Rated Speed)
× Motor Poles/120
E2-02 = (1800 RPM - 1730 RPM)
× 4/120
E2-02 = 2.33 Hz
Motor No-Load Current (E2-03) is calculated as follows:
Motor No-Load Current (E2-03) can sometimes be read directly off of the motor nameplate; it is often listed as NLA
(no-load amps). If there is no listing on the nameplate, motor no-load current can be estimated as follows:
Motor full load current (FLA)
× 35%.
Example: 4-pole, 60 Hz motor, Motor FLA = 60 Amps.
E2-03 = 60 Amps
× 35%
E2-03 = 21 Amps.
Fault Indication
LCD
<Memobus>
<1>
The JVOP-182 LED operator does not support the letter "k." On this operator, the Belt Break fault will be displayed as "b-br-."
Description
Cause
Countermeasures
Belt Break Detection
B-BRK
Belt Break
<3Ch>
The drive's output frequency was at the
maximum output frequency (E1-04) for more
than 30 seconds. See section 6.3 for details.
The belt has broken or the motor has become
uncoupled from the load.
Service or repair belt or coupling.
Alarm Indication
LCD
<Memobus>
Description
Cause
Countermeasures
Stopping Method
Selection Error
OPE12
Stopping Method
<0Ch>
This Operator Programming Error occurs
when the drive is in V/f or OLV control
mode, OV Suppression functionality is
enabled, and a stopping method has been
selected which is not compatible with OV
Suppression.
OV Suppression is enabled (P1-01 = 1), the
control mode is V/f (A1-02 = 0) or OLV
(A1-02 = 2), and one of the following
stopping methods has been selected:
-Ramp to Stop, (b1-03 = 0)
-Coast to Stop w/ Timer (b1-03 = 3)
1.If OV Suppression functionality is
required, select either Coast to Stop
(b1-03 = 1) or DC Injection Braking to Stop
(b1-03 = 2) stopping method.
2.Switch to an alternate control mode.
3.Disable OV Suppression (P1-01 = 0).