0 thermal considerations, 1 case temperature, 2 forced convection – KEPCO KFD 6-25-28W User Manual
Page 11: 3 heat sink models, 4 natural convection
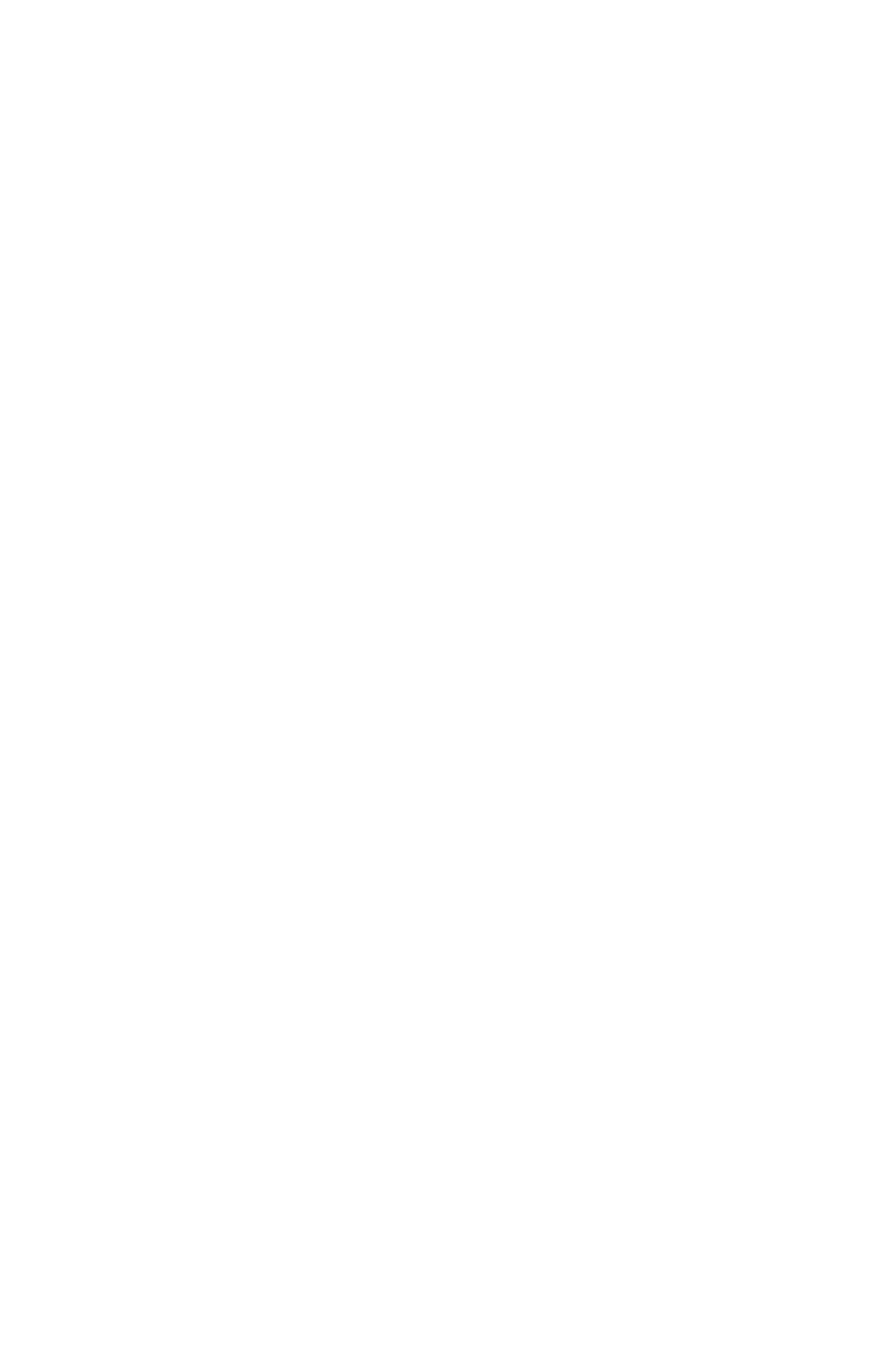
KFD 6-25-28/060801
7
18.0 THERMAL CONSIDERATIONS
To ensure reliable operation of the KFD unit, thermal management is important. Heat dissipated by the unit
is conducted to the case, and subsequently convected to the surrounding air. Convection cooling can be
improved by mounting a heat sink to the top of the unit. Six threaded holes, No. 4-40 [0.18 inches deep
(46mm)] are provided for this purpose. A dry pad or thermal compound should be used to minimize thermal
resistance between the case and the heat sink. The case temperature should not exceed 90 degrees C.
18.1 CASE TEMPERATURE
Proper cooling for the KFD D.C. to D.C. Converter can be verified by measuring the case temperature of
the module. It is measured on the top surface of the unit at a sensing point---3 inches (76mm) from the left
edge of the power module, and 0.7 inches (18mm) from the top edge of the unit. The case temperature
must not exceed 95°C while the unit is operating in the final system configuration. After the module has
reached thermal equilibrium, the measurement can be made with a thermocouple or surface probe. If a
heat sink is mounted to the case, make the measurement at the base of the heat sink as close as possible
to the heat sensing point. The contact resistance between the mounting surface and the heat sink must be
taken into account when making this measurement.
Maintaining the operating case temperature (Tc) within the specified range keeps internal component tem-
peratures within their specifications. That in turn helps keep the expected mean time between failure
(MTBF) from falling below the specified rating. The KFD Power Module is designed with temperature resis-
tant components such as ceramic capacitors that do not degrade during prolong exposure to high temper-
atures, as do aluminum electrolytic capacitors.
18.2 FORCED CONVECTION
The discussion that follows can be applied to all high powered KFD board mounted power modules in the
4.8in (121.9mm) x 2.5in (63.5mm) x 0.5in (12.7mm) package.
Increasing the air flow over the module improves cooling. In that regard Figure 11 shows the power derat-
ing (P
D
) versus local ambient temperature (T
A
) at air flows, from natural convection to 800 ft./min. (4.1 m/
s). The curves in this Figure were obtained from measurements made in a free stream of air approaching
a vertically oriented module on a printed wiring board, positioned in a rectangular passage. The Figure
can be used to determine the appropriate air flow for a given set of operating conditions.
For example, at P
D
=20W and T
A
=40°C, an air flow of 200 ft./min. (1.0 m/s) is sufficient to keep the module
within its ratings.
18.3 HEAT SINK MODELS
Figures 9 and 10 show a number of standard heat sinks that are available for the KFD Power Module,
labeled with their respective thermal resistances for natural convection. The heat sinks mount to the top
surface of the power module using No. 4-40 hardware, torqued to 5 in.lbs. To minimize contact resistance
and temperature drops, use a thermally conductive dry pad or thermal grease between the case and heat
sink.
18.4 NATURAL CONVECTION
The plots in Figures 12 and 13 represent power derating for a power module in natural convection when
attached to various heat sinks (these include designs with fins oriented along the length and designs with