Pid operation – Auto-Zone Control Systems Auto-Zone CV-C Controller Installation Guide (Version 01A) User Manual
Page 38
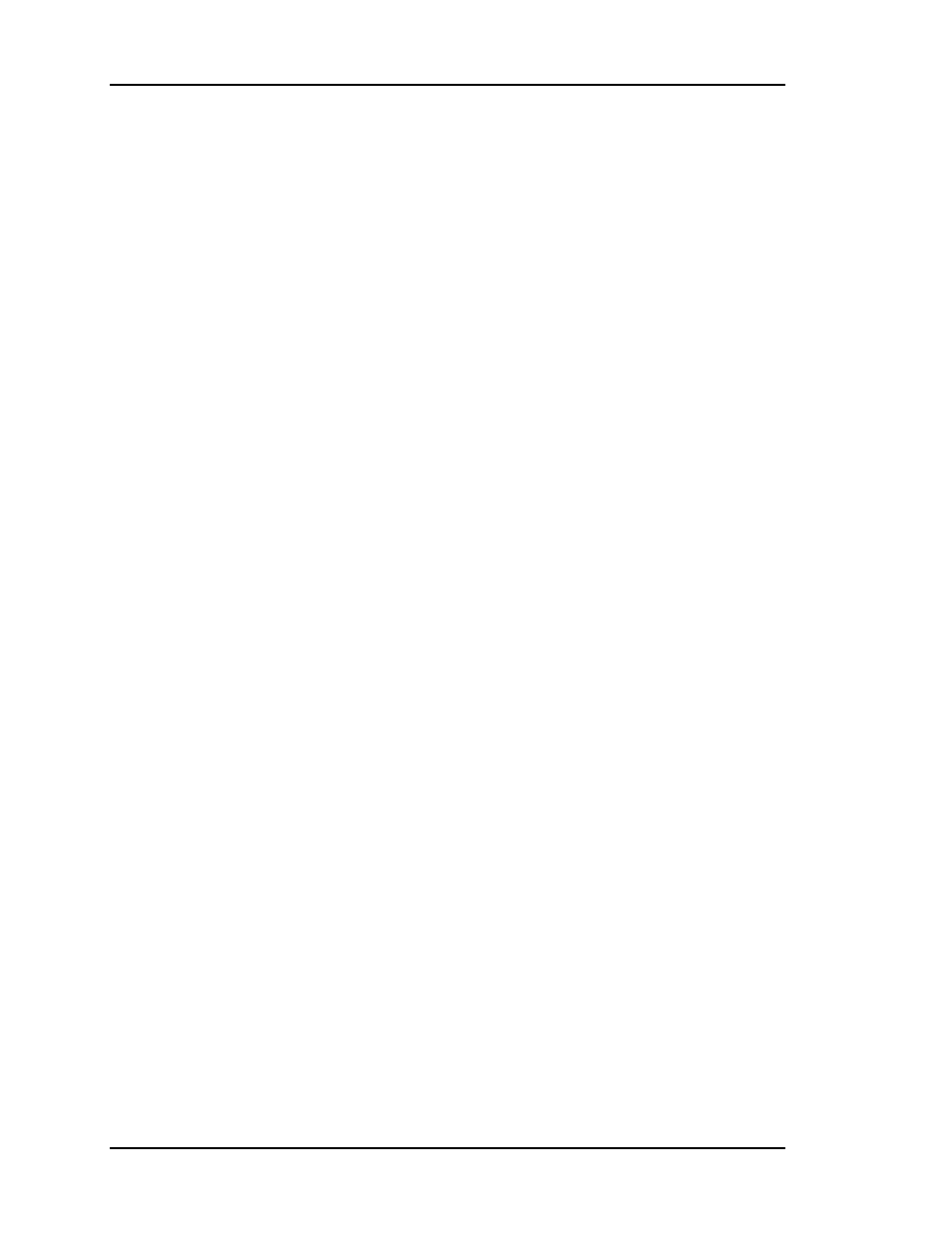
Section 2
Auto-Zone CV-C
2-28
Sequence of Operation
PID Operation
PID Operation
PID Operation
PID Operation
The Hot & Chilled Water Valves are controlled via a Proportional, Integral, Derivative (
PID ) loop. This method of control provides accurate temperature control with minimal
adjustments to the valve position. The best method of explaining the PID operation is to
show a simplified form of the formulas incorporated into the controller code.
The following abbreviations will be used in the formula:
TimeSP
= Integrating Interval
HotSP
= Supply Air Temperature Setpoint
Kp
= Proportional Constant
Ki
= Integral Constant
Kd
= Derivative Constant
P
= Proportional Error
I
= Integral Error
D
= Derivative Error
HWValve
= Calculated Valve Position
SupplyAir
= Current Supply Air Temperature Reading
IF the TIMER has exceeded the TimeSP THEN
Error = HotSP - SupplyAir
P
= ( Error x ( Kp / 100 )) x 100
I
= ( Error x ( Ki / 10))
D
= ( Error - OldError ) x ( Kd / 10 )
HWValve =
P + I + D
OldError
= Error
“ Save current error for next time “
END ROUTINE
The Error is the difference between the Setpoint and the actual Temperature. The P error
uses a limited amount of this error to create a proportional only valve position. For
example, if the Kp was set to 10 then a 10°C temperature error would cause the P error
to set the valve 100% open.
10° Error = ( 10 x ( 10 / 100)) x 100 = 100%
5° Error = ( 5 x ( 10 / 100)) x 100 = 50%