Electrical connections (4.7) – Flowserve PolyChem GRP User Manual
Page 22
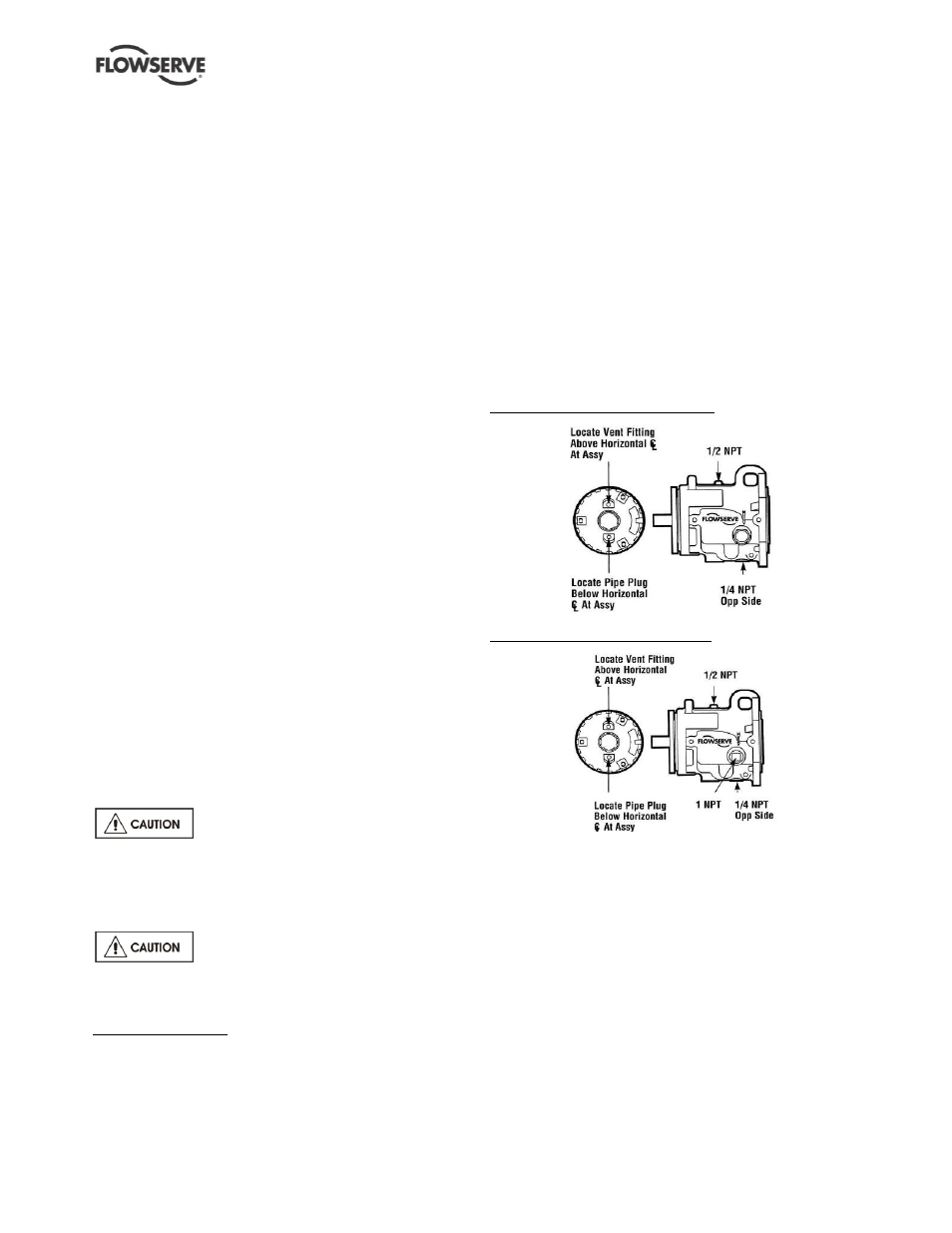
USER INSTRUCTIONS POLYCHEM GRP ENGLISH 71569132 12-04A
Page 22 of 52
flowserve.com
Single seals requiring re-circulation will normally be
provided with the auxiliary piping from the pump
casing already fitted.
Seal housings/covers having an auxiliary quench
connection require connection to a suitable source of
liquid flow, low pressure steam or static pressure from a
header tank. Recommended pressure is 0.35 bar
(5 psi) or less. Check General arrangement drawing.
Double seals require a barrier liquid between the
seals, compatible with the pumped liquid.
With back-to-back double seals, the barrier liquid
should be at a minimum pressure of 1 bar above the
maximum pressure on the pump side of the inner
seal. The barrier liquid pressure must not exceed
limitations of the seal on the atmospheric side. For
toxic service the barrier liquid supply and discharge
must be in a safe area.
Special seals may require modification to auxiliary
piping described above. Consult Flowserve if unsure
of correct method or arrangement.
For pumping hot liquids, to avoid seal damage, it is
recommended that any external flush/cooling supply
be continued after stopping the pump.
Tandem seals require a barrier liquid between the
seals compatible with the pumped liquid.
4.6.6.2 Packing
When the pump is intended to be equipped with shaft
packing, it is not Flowserve standard practice to
install the packing in the stuffing box prior to
shipment. The packing is shipped with the pump. It
is the pump installer’s responsibility to install the
packing in the stuffing box.
Failure to ensure that packing is
installed may result in serious leakage of the pumped
fluid.
4.6.6.3 Piping connection
– seal/packing support
system
If the pump has a seal support system
it is mandatory that this system be fully installed and
operational before the pump is started.
Packing lubrication. Water, when compatible with the
pumpage, should be introduced into the seal gland at
pressure 0.69 to 1.03 bar (10 to 15 psi) above the
stuffing box pressure.
The gland should be adjusted to give a flow rate of 20
to 30 drops per minute for clean fluid. For abrasive
applications, the regulated flow rate should be 0.22 to
0.47 m
3
/h (1 to 2 US gpm)
Grease lubrication, when compatible with the liquid
being pumped, may be used. In non-abrasive
applications the liquid being pumped may be
sufficient to lubricate the packing without the need for
external lines.
4.6.6.4 Piping connection - Oil mist lubrication
system
The piping connections for an oil mist lubrication
system are shown below.
Oil mist ready housing wet sump
Oil mist ready housing dry sump
4.6.6.5 Piping connection
– air bleed line
The 1K3x2GS-7 self-priming pump evacuates the air
from the suction line when it primes. The length of
the line and diameter determine the volume of air and
the time required for priming. Flowserve
recommends that a small air bleed line be fitted from
the discharge piping to the sump if the air is not able
to freely vent out the discharge pipe.