5 commissioning, start-up, operation and, Shutdown, 1 pre-commissioning procedure – Flowserve WMV IDP User Manual
Page 14: 2 direction of rotation, 3 guarding, 4 priming and auxiliary supplies, 5 starting the pump, 6 running the pump, Commissioning and operation (5), Direction of rotation (5.2)
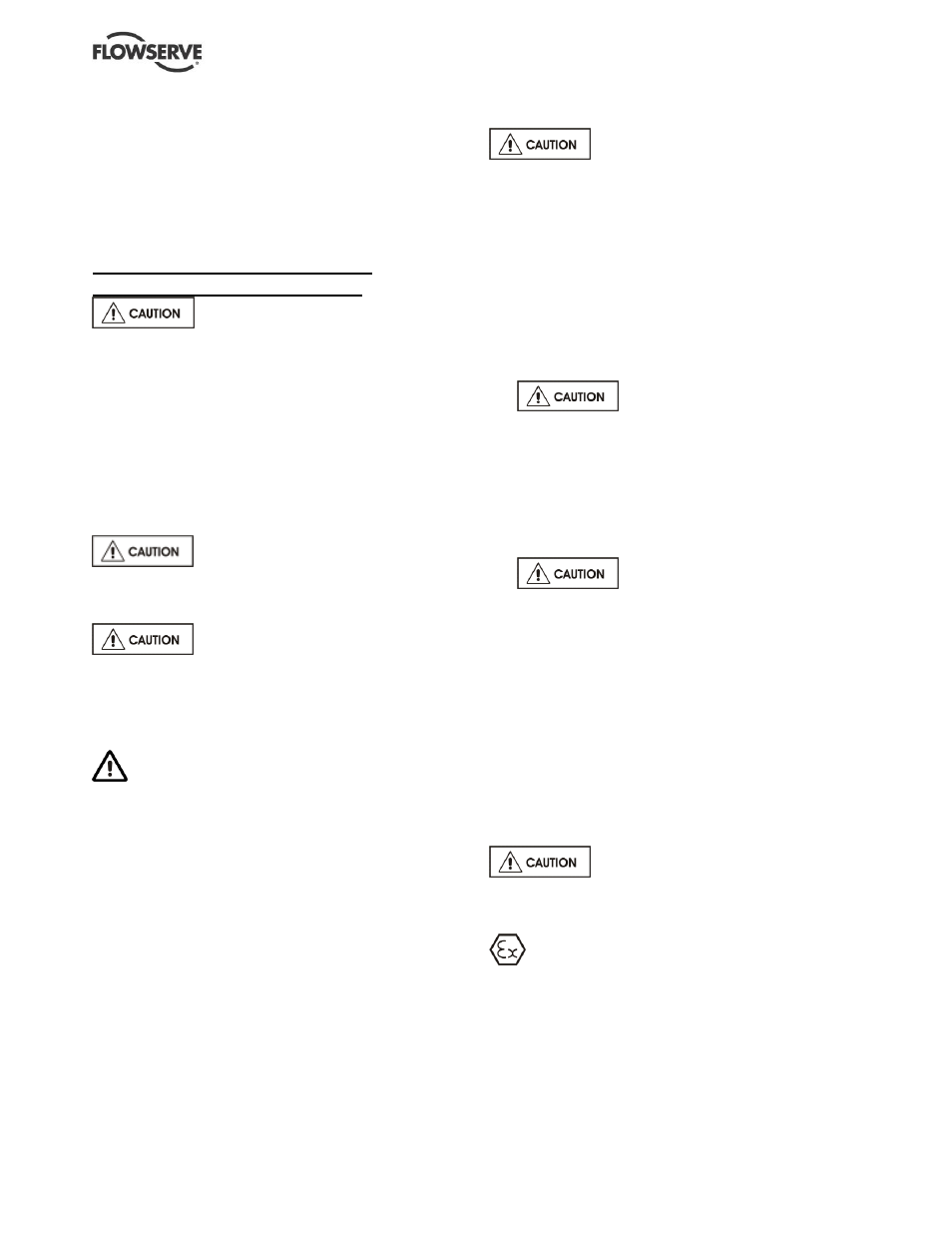
WMV, WMVS USER INSTRUCTIONS ENGLISH 26999970 10-12
Page 14 of 28
flowserve.com
If leakage of product from the pump or its associated
sealing system can cause a hazard install an
appropriate leakage detection system.
To prevent excessive surface temperatures at
bearings carry out temperature or vibration
monitoring.
5 COMMISSIONING, START-UP,
OPERATION AND SHUTDOWN
These operations must be carried
out by fully qualified personnel.
5.1 Pre-commissioning procedure
5.1.1 Lubrication
The pump is lubricated by the liquid pumped
Electric motors are supplied pre-greased and are
normally sealed for life. If in doubt, refer to motor
instruction manual.
5.2 Direction of rotation
Serious damage can result if the
pump is started or run in the wrong direction of
rotation. These pumps turn clockwise as viewed from
the motor end.
If maintenance work has been carried
out to the site's electricity supply, the direction of
rotation should be re-checked as above in case the
supply phasing has been altered.
5.3 Guarding
Guarding is supplied fitted to the pump set.
In member countries of the EU and EFTA, it is a legal
requirement that fasteners for guards must remain
captive in the guard to comply with the Machinery
Directive 2006/42/EC. When releasing such guards,
the fasteners must be unscrewed in an appropriate
way to ensure that the fasteners remain captive.
Whenever guarding is removed or disturbed ensure
that all the protective guards are securely refitted
prior to start-up.
5.4 Priming and auxiliary supplies
Ensure all electrical, hydraulic, pneumatic, sealant and
lubrication systems (as applicable) are connected and
operational.
5.4.1 Filling and priming
Ensure inlet pipe and pump casing is
completely full of liquid before starting continuous
duty operation.
Priming may be carried out with an ejector, vacuum
pump interceptor or other equipment, or by flooding
from the inlet source.
When in service, pumps using inlet pipes with foot
valves may be primed by passing liquid back from the
outlet pipe through the pump.
5.5 Starting the pump
a)
Ensure flushing and/or cooling/
heating liquid supplies are turned ON, before
starting pump.
b) CLOSE the outlet valve.
c) OPEN all inlet valves.
d) Prime the pump.
e) Start motor and check the outlet pressure.
f) If the pressure is satisfactory, SLOWLY open the
outlet valve.
g)
Do not run the pump against a
closed valve for more than 1 to 2 minutes.
h) If NO pressure, or LOW pressure, STOP the
pump. Refer to section 7, Faults; causes and
remedies, for fault diagnosis.
5.6 Running the pump
Vent the pump to enable all trapped air to escape
taking due care with hot or hazardous liquids
5.6.1 Pumps fitted with mechanical seal
Mechanical seals require no adjustment. Any slight
initial leakage will stop when the seal is run in. Seals
will always have leakage emission from the boundary
film edge in operation.
Never run a mechanical seal dry, even
for a short time.
5.6.2 Bearings
If the pumps are working in a potentially
explosive atmosphere monitor temperature and/or
vibration at the bearings.