Flowserve 3400IQ Digital Positioner User Manual
Page 29
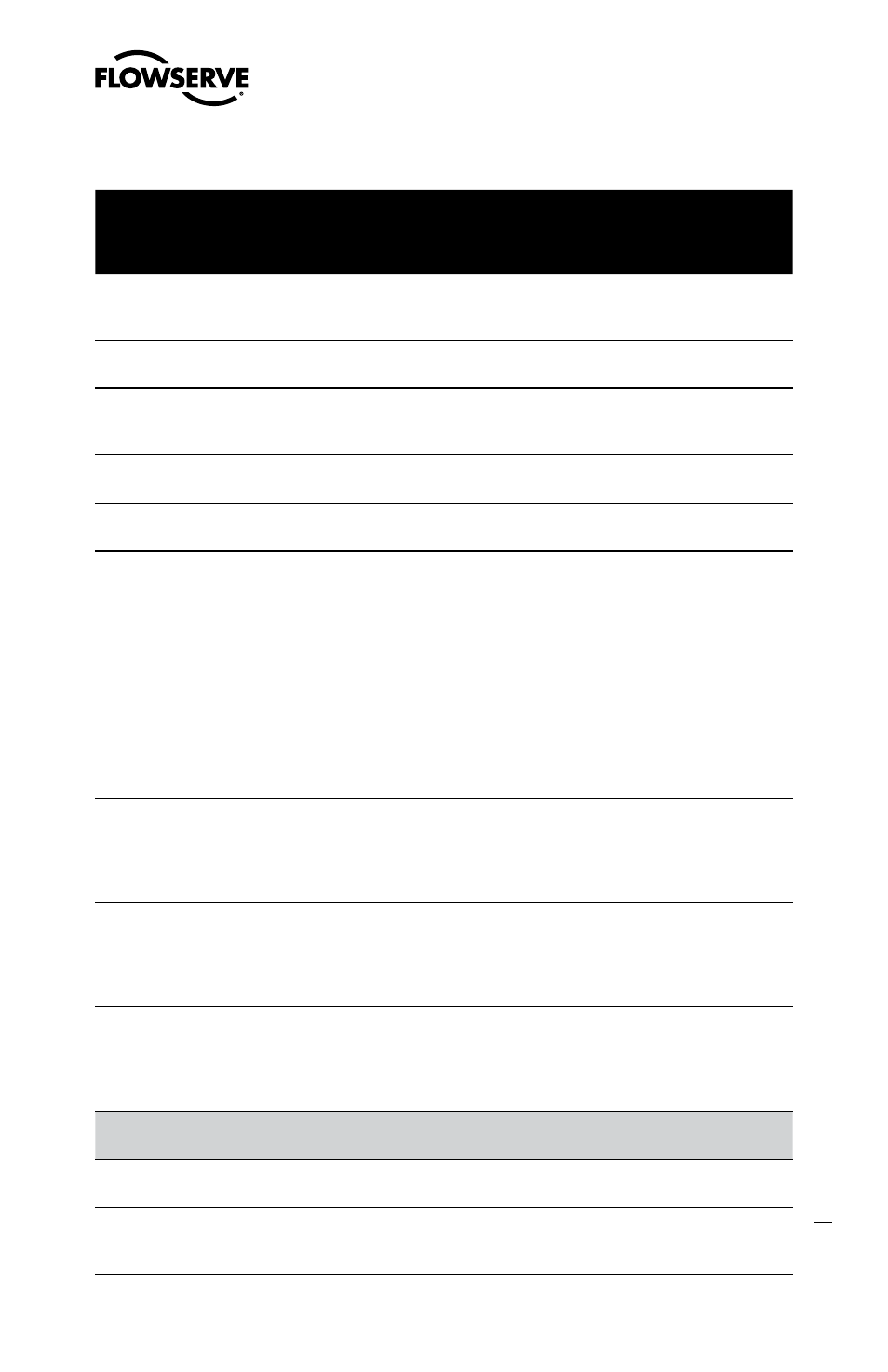
Logix 3400IQ Digital Positioner FCD LGENIM3401-00 – 06/06
flowserve.com
Table VII: Status and Conditions (continued)
Co
lo
rs
Id
en
tifi
er
Indication and Resolution
YGRR
14
Local jog control mode The unit has been placed in a local override mode where the valve
can only be stroked using the two local jog buttons. It may be cancelled by briefly pushing the
RE-CAL button.
YYGR
15
Pressure calibration in progress Calibration sequence controlled by a handheld or Host
software that can only be cancelled by that software.
YYYY
16
Local user interface disabled Host software has been used to disable the local interface. If
local control is desired then the local interface must be re-enabled from the remote software.
This code is only present for a short time when the RE-CAL button is pressed.
YRRG
17
Waiting Adjust to full open position setting from User—only used during Jog calibration
see explanation in Section 7.5, “RE-CAL,” for operation.
YRYG
18
Setting IL offset while calibrating An automatic step in the calibration process that is done
with the valve at 50% position. This must be completed for proper calibration.
YRYY
19
No feedback motion while calibrating Indicates that there was no motion of the actuator
based on the current stroke time configuration. Check linkages and air supply to make sure
the system is properly connected. If the time out occurred because the actuator is very large
then simply retry the RE-CAL and the positioner will automatically adjust for a larger actuator
by doubling the time allowed for movement. This error may be cleared by briefly pushing
the RE-CAL button, which will force the positioner to use the parameters from the last good
calibration.
YRYR
20
Feedback 0% out of range Calibration error indicating that the position sensor was out
of range during the calibration of the closed position. To correct the condition, adjust the
positioner mounting, linkage or feedback potentiometer to move the position sensor back into
range then restart the calibration. This error may be cleared by briefly pushing the RE-CAL
button, which will force the positioner to use the parameters from the last good calibration.
YRRY
21
Feedback 100% out of range Calibration error indicating that the position sensor was
out of range during the calibration of the open position. To correct the condition, adjust the
positioner mounting, linkage or feedback potentiometer to move the position sensor back into
range then restart the calibration. This error may be cleared by briefly pushing the RE-CAL
button, which will force the positioner to use the parameters from the last good calibration.
YRRR
22
Feedback span too small The range of motion of the position feedback arm was too small
for optimum performance. Check for loose linkages and/or adjust the feedback pin to a posi-
tion closer to the follower arm pivot to create a larger angle of rotation and recalibrate. Briefly
pushing the RE-CAL button acknowledges this condition and the positioner will operate using
the current short stroke calibration if otherwise a good calibration.
YRGR
23
Feedback unstable while calibrating Check for loose linkages or loose positioner sensor.
This error may be cleared by briefly pushing the RE-CAL button, which will force the
positioner to use the parameters from the last good calibration. This error may appear on
some very small actuators during the initial calibration. Redoing the calibration may clear the
problem.
R - - -
Any sequence starting with a red light indicates that there is an operational problem with
the unit.
RGRR
24
Position deviation (user-set) The position has exceeded user-defined error band between
command and position.
RGYY
25
Pressure reading out of range The internal pressure sensors are either saturated with a
pressure over 150 psi or the sensor has failed. Check supply pressure and if OK check the
pressure sensor board connections and replace pressure sensor board if necessary.
Continued on page 30