Flowserve Desuperheaters User Manual
Page 12
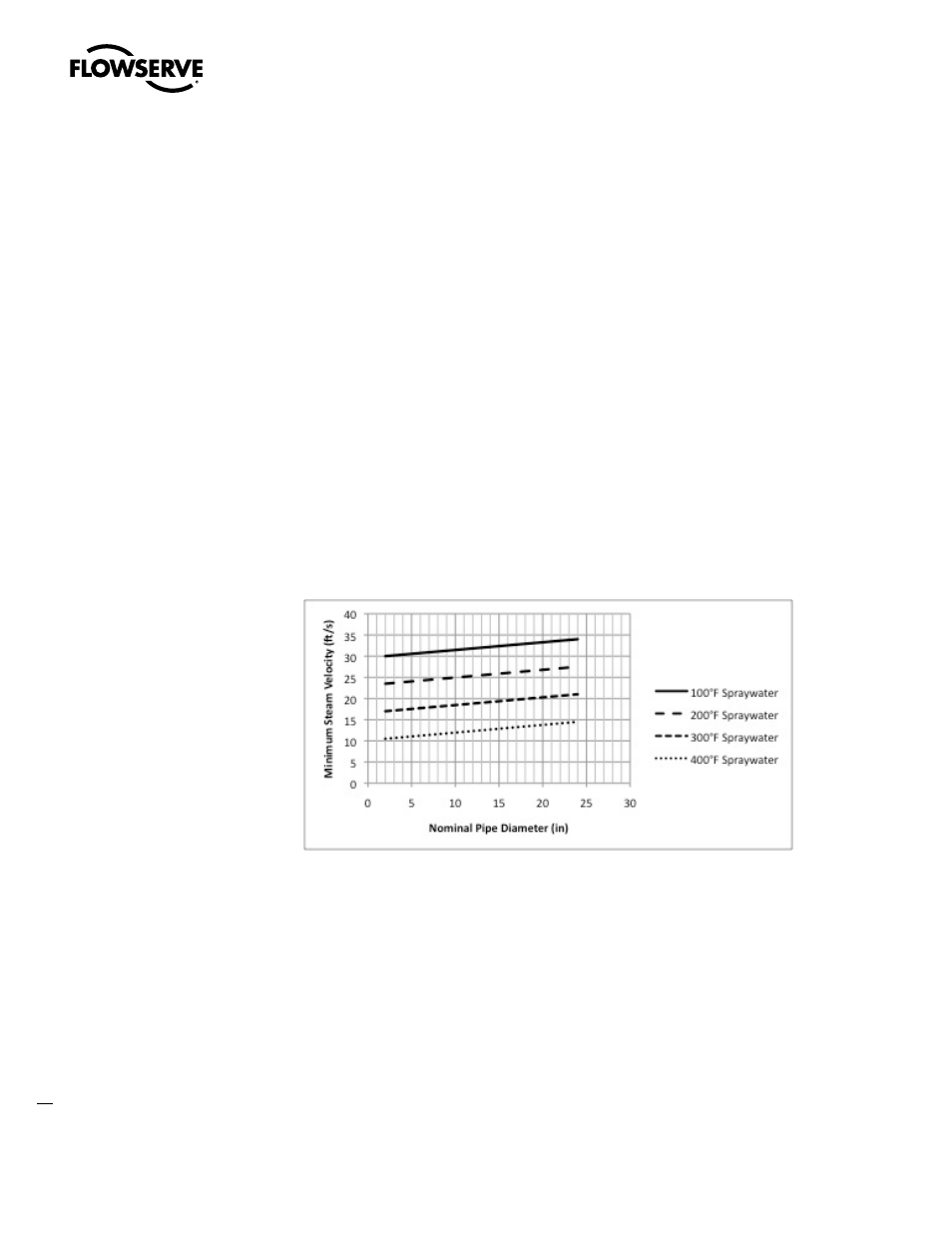
Desuperheaters FCD VLENIM0115-00– 09/11
12
a
CAUTION: Failure to prevent particulate or debris from entering the desuperheater can
cause malfunction of the nozzles, poor temperature control, and dangerous equipment
failures.
5. Install and tighten line bolting on the mounting flange and cooling water flange to typical line
bolting torque values.
OPERATION
Desuperheaters should maintain the following conditions to operate optimally.
1. The cooling water control valve should be capable of tight ASME Class V or VI shutoff.
c
WARNING: Leaky cooling water valves could cause dripping water to impinge on equip-
ment causing thermal shock resulting in equipment damage.
a
CAUTION: If the temperature difference between the cooling water and the steam is
greater than about 800°F (427°C) thermal fatigue may need to be considered more
closely.
2. The minimum steam velocity should generally be 33 ft/s (10 m/s), but should be greater than the
limits shown in Figure 11. The maximum steam velocity generally is 250 ft/s (76 m/s) but should
not exceed 350 ft/s (107 m/s).
Figure 11: Minimum Steam Velocity for Atomization
c
WARNING: Steam velocities below the minimum values listed may not provide adequate
turbulence for mixing. This could result in cooling water falling out of the steam and impinging
on the pipe resulting in equipment damage.
c
WARNING: Steam velocities higher than the maximum values listed may result in stratified
steam in the piping and may require excessive straight pipe lengths for adequate cooling water
evaporation which could result in equipment damage.
3. For the MaxCool MCX nozzle the minimum pressure drop between the steam and the cooling water
should be 2.0 bar (29 psig) for a 1 bar (14.5 psig) cracking pressure nozzle, 4 bar (58 psig) for a 3
bar (43.5 psig) cracking pressure nozzle, and 6 bar (87 psig) for a 5 bar (72.5 psig) cracking pres-
sure nozzle. The minimum pressure drops between the steam and the cooling water for VaporCool
and VaporCool MicroNozzles are shown in Tables 3 and 4.