5 actuator power, Worcester controls – Flowserve AF-17 Electronic Positioner User Manual
Page 15
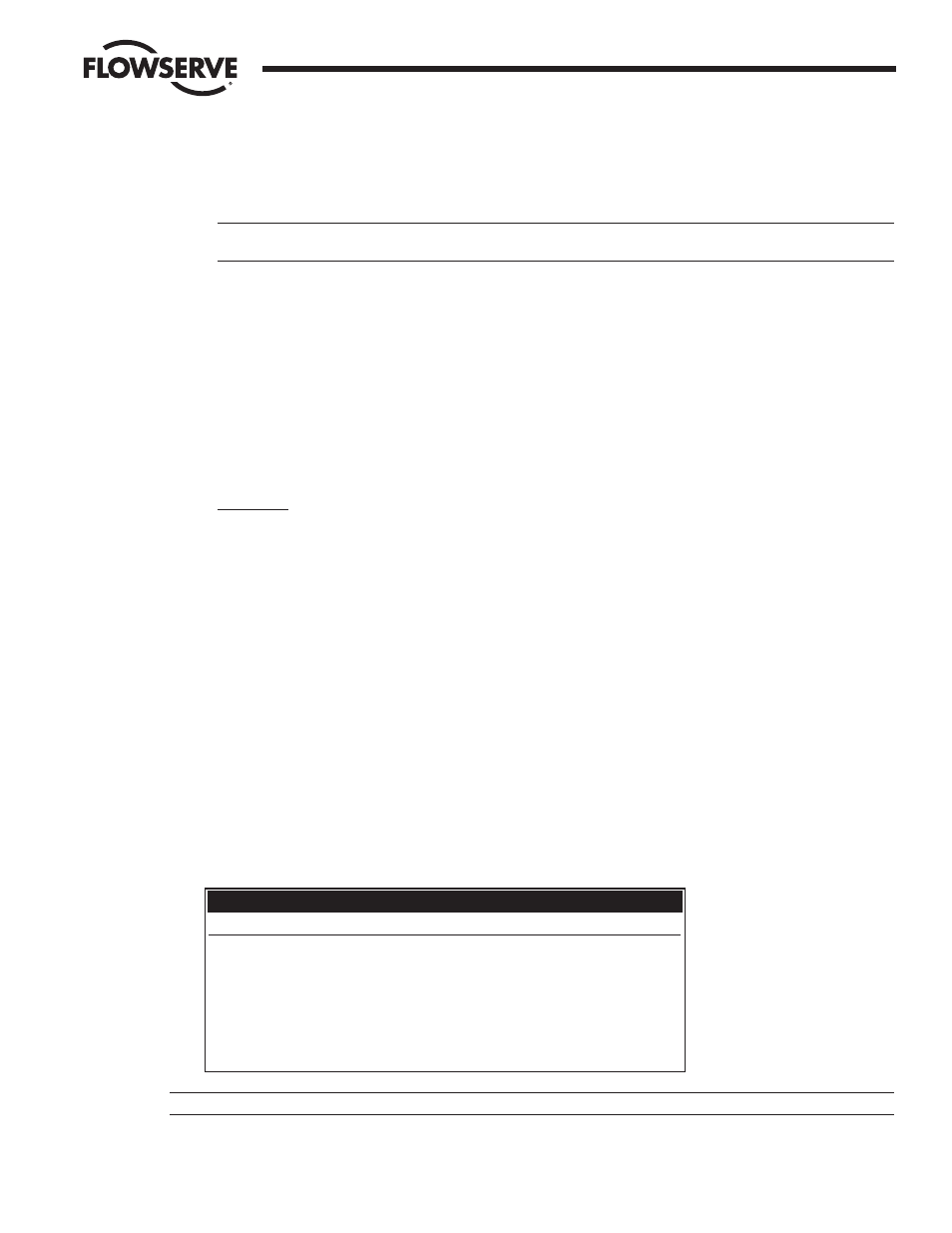
WCAIM2031
AF-17 Electronic Positioner: Installation, Operation and Maintenance
15
B. For 120 VAC board only, remove yellow wire from terminal 5 and brown wire from terminal 6, disconnect them from N.O.
contacts of switches 1 and 2 and discard them. For all AC boards, connect wires of output signal connector assembly
from AF-17 board connector (P1) such that red wire (+) is wired to terminal 5 and black wire (-) is wired to terminal 6 on
internal side of terminal strip.
NOTE: Check for wiring diagram label inside of cover, if it doesn’t have the 4-20 mA output option wiring shown,
mark label for terminals 5 and 6 according to Figure 7.
C. External wiring is between actuator terminal strip and outside power supply and various controls. Common wire of the
power supply is wired to terminal 1 and hot wire of the power supply to terminal 2. An outside position indicator meter is
wired with positive connection to terminal 5 and negative connection to terminal 6.
D. Securely tighten all terminal screws. Secure all wires neatly with the cable ties. Keep wiring away from all rotating parts
and ensure wiring is not pinched when actuator cover is installed.
E. The feedback potentiometer has to be adjusted to obtain the proper resistance range. See paragraph 3.2.4. To obtain
proper 4-20 mA output, the AF-17 board 4-20 mA output has to be calibrated. Using an ammeter connected to actuator
terminals 5 (positive) and 6 (negative) adjust the two potentiometers R29 and R30 on the board. Locate the actuator in
the closed position (0%) and adjust R30 potentiometer (closest to TB-2) to obtain 4 mA on the ammeter. Move the
actuator to the open position (100%) and adjust R29 potentiometer (closest to the shaft hole) to obtain 20 mA. Because
adjustment of one potentiometer affects the other, repeat the procedure several times to obtain proper values.
IMPORTANT: The feedback potentiometer is calibrated for only one 90° quadrant of valve operation. If the output shaft is
repositioned to another 90° quadrant or if the output shaft is rotated a multiple of 360° from its original position, or if the
4-20 mA position output option is disconnected from the AF-17 board, the feedback potentiometer will no longer be in
calibration and must be recalibrated. See paragraph C of part 1.1 and paragraph 3.2.4.
3.5 Actuator Power
3.5.1 Wire Size
AC power to the positioner and from the positioner to the actuator should be with wire no smaller than #18 gauge and with
insulation rated for the particular application. The #18 gauge wire size is sufficient for all Worcester Series 75 actuators.
When using the positioner with other makes of actuators, check the manufacturer’s current rating to determine the correct
wire size.
3.5.2 Terminations and Voltage
AC power connections are made to terminals 1 and 2 of the terminal strip. The AC neutral, or common, wire should be
connected to terminal #1 and the AC “Hot” wire to terminal #2. Note that the positioner requires a minimum of 110 VAC,
and a maximum of 130 VAC for the 120 VAC version and a 220 VAC minimum, 250 VAC maximum for the 240 VAC version.
Grounding wires should be connected to green colored grounding screw (if present) on actuator base or to any base plate
mounting screw in the actuator.
3.5.3 Minimum Fuse Ratings
See table below for minimum fuse rating when overcurrent protection is used in motor power circuit.
NOTE: This table shows the minimum rating to prevent inrush current from blowing the fuse.
Minimum Fuse Rating for Overcurrent Protection
Actuator Size
Voltage
Fuse Rating
10-23
120 VAC
5A
25/30
120 VAC
10A
10-23
240 VAC
3A
25/30
240 VAC
5A
10-23
12 VDC
10A
10-23
24 VDC
5A
Flow Control Division
Worcester Controls