5 adjustment recheck, 6 operational check, 7 if problems occur – Flowserve AF-17 Electronic Positioner User Manual
Page 18
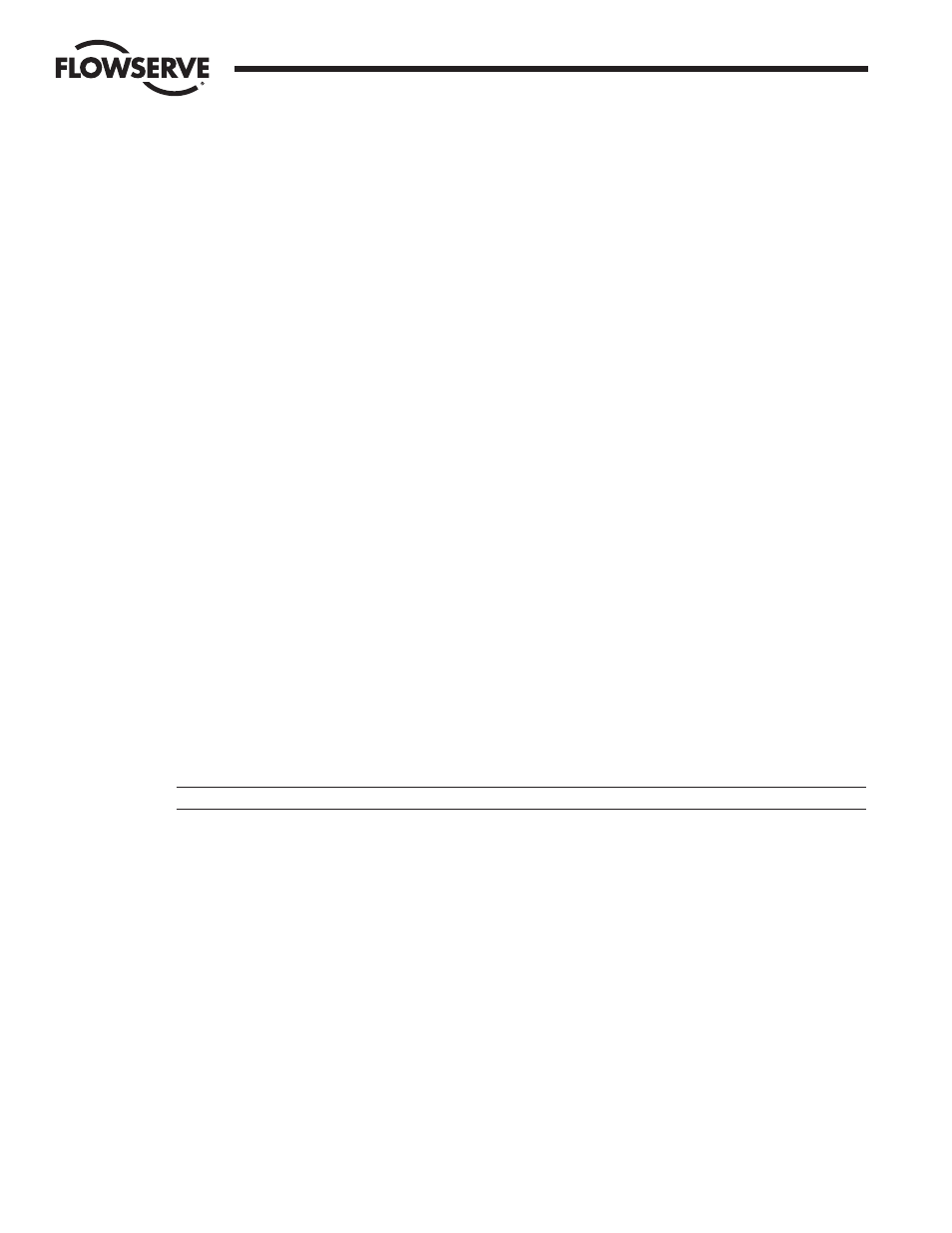
18
AF-17 Electronic Positioner: Installation, Operation and Maintenance
WCAIM2031
4.5 Adjustment Recheck
There is some interaction between adjustments of the “Zero” and “Range” controls, therefore if an adjustment is made at one end
of travel, the opposite end should be rechecked.
Although the “Range” and “Zero” settings are relatively unaffected by fairly large temperature changes, it is suggested that
positioners be checked during a users routine maintenance schedule.
4.6 Operational Check
Once the AF-17’s circuit board zero and span potentiometers are set for the minimum and maximum process signal values,
typically a 4-20 mA signal, do the following checks:
4.6.1 Increasing Signal
Reduce process input signal below the minimum value so that actuator stops on its closed limit switch and closed LD2 is
on. Increasing the input signal in small increments should allow the actuator to move in angular increments proportional to
these small incremental increases in the incoming signal.
4.6.2 Decreasing Signal
Continually adjust the signal until the maximum signal value is reached and actuator is in fully open position. With a signal
over 20 mA, when the positioner is calibrated for 4 to 20 mA, the actuator will operate until the proper cam has actuated the
open limit switch. Note that the open LD1 will be “on” when actuator stops at limit switch.
In similar fashion, decrease the process signal in small values. The actuator should move closed in small steps until the
fully closed position is reached at the minimum signal value, typically 4 mA for a 4-20 mA calibration.
4.6.3 Attaching Label
Attach label to board.
4.7 If Problems Occur
If problems occur while trying to obtain the desired positioner action, check the following:
4.7.1 Cam Adjustment
The actuator cams should actuate the limit switches 1° to 3° after the actuator stops at either the fully open or fully closed
position.
If the actuator is closed at 0 degrees, the limit switch must actuate by the time the actuator is at the minus 1 to 3 degree
position. Similarly, at the open or 90-degree position, the limit switch must actuate by the time the actuator is at the 91 to
93 degree position.
NOTE: See CAUTION in part 4.1.
4.7.2 Feedback Potentiometer Calibration
Check the feedback potentiometer calibration per paragraph 3.2.4 of the manual. At either the full open or the full closed
position, stopping at either limit switch, the potentiometer must still be within its electrical travel. To verify this, check the
resistance at either the full open or full closed position. The resistance measured between terminals 2 and 3 or 2 and 1 on
the AF-17 terminal block, with the power off, must be between 80 ohms and 90 ohms.
Readjust the feedback potentiometer as necessary and check as in the previous steps for proper incremental movement of
the valve actuator from limit switch to limit switch; full closed to full open; -1° to -3°, +91° to +93°.
4.7.3 Reverse-Acting
For a reverse-acting actuator, read part 5.4 in the manual. Simply follow the instructions of part 5.4 and readjust the circuit
board “zero” and “range” potentiometers as needed.
4.7.4 Adjustment to Loop Process
Once the actuator and positioner are installed in the system, further adjustments may be necessary to trim the AF-17 circuit
board/actuator action to the process controller’s action in the process loop. The AH potentiometer on the circuit board may
require adjustment counterclockwise to stop the AF-17 circuitry from reacting to spurious electrical noise signals.
Flow Control Division
Worcester Controls