Pulse operation, Mk2000a parameter set-up – MK Products MK 2000A User Manual
Page 15
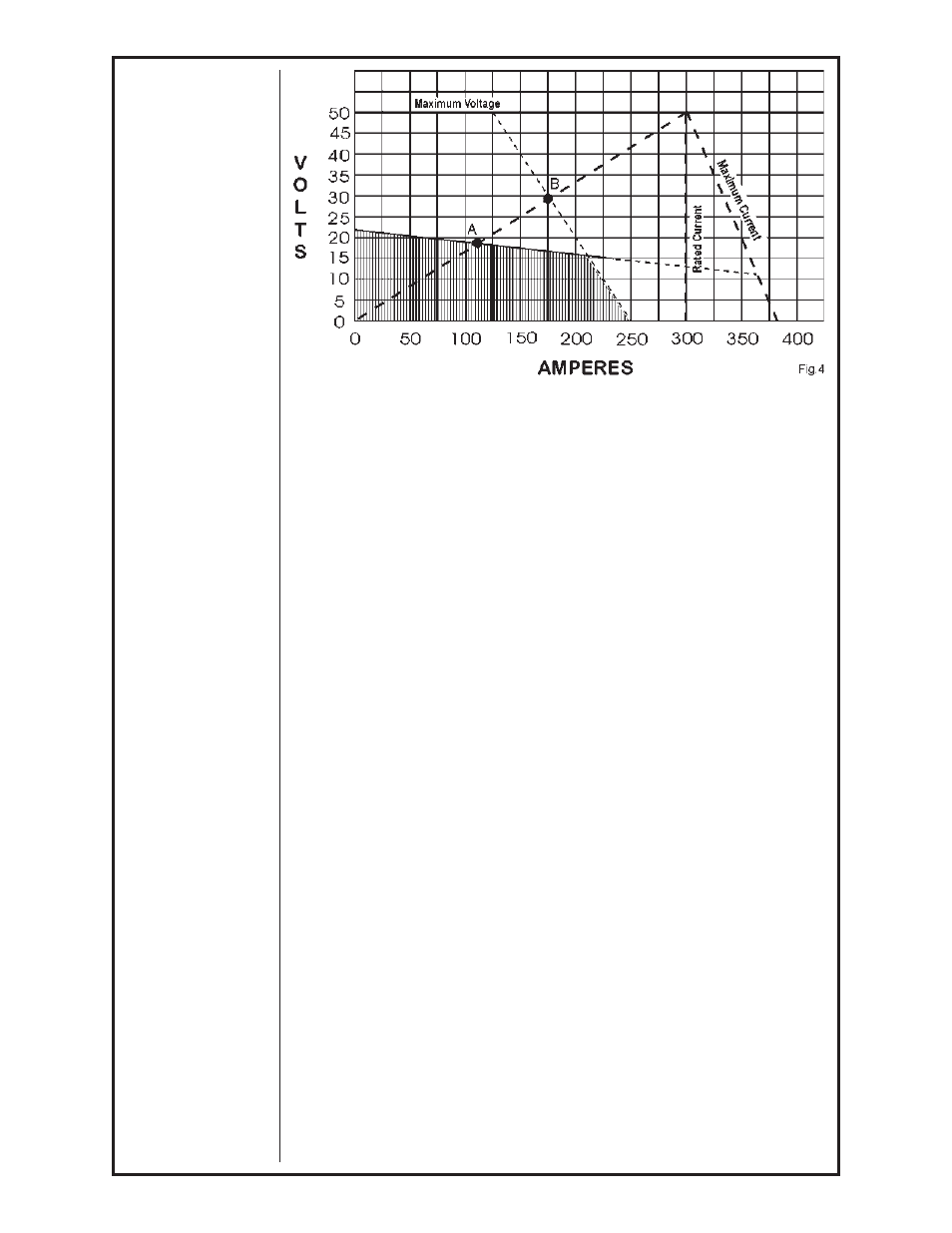
MK 2000A - Owner's Manual - Page 15
The ‘Pulse Slope’ is set for CC operation at 38 volts/100 amperes (70%) and
the Pulse Level is set to 175 amperes at pivot point “B”.
Welding at these settings results in a CV operating mode with wire feed
rates adjusted to provide any current between about l00 and 200 amperes.
Short circuit current, however, is limited to 250 amperes by the Pulse Level
setting.
The Pulse Level and Slope may also be adjusted to any desired values, and
are independent of the Background Level and Slope. It is not necessary for
point “B” to be set above point “A”, although this will normally be the case.
The only difference in operation between the Background Level/Background
Slope and the Pulse Level/Pulse Slope is that pulse operation adds to the
Background Level and does not change the Pulse Level.
Inductance may be used with any combination of other settings.
Pulse Operation
The MK2000A provides a range of operating capabilities not available in any
general purpose welding power supply.
Pulse operation is used to provide a measure of independence in the control
of heat input, current density during material transfer, and arc voltage which
effects both heat and cleaning capability.
The majority of available pulsed welding power supplies operate with a
background voltage and then induce extended firing of one or two thyristors
to provide voltage pulses at 60 or 120 pulses per second. (360 pps with three
phase operation) The current resulting from these voltages depends on the
firing point which, in turn, controls the pulse duration (width). It is usually
described in terms of the peak current value.
MK2000A Parameter Set-Up
In pulsed spray welding the current is varied from the background level to a
peak level. The background level is well below the transition current while
the peak level is well into the spray arc region, Figure 5. During the peak
level one droplet is transferred to the work. The current then drops to the
background level which allows the puddle to cool, at which time no metal
is transferred.