Allmand Brothers TLB6235 Tractor User Manual
Page 16
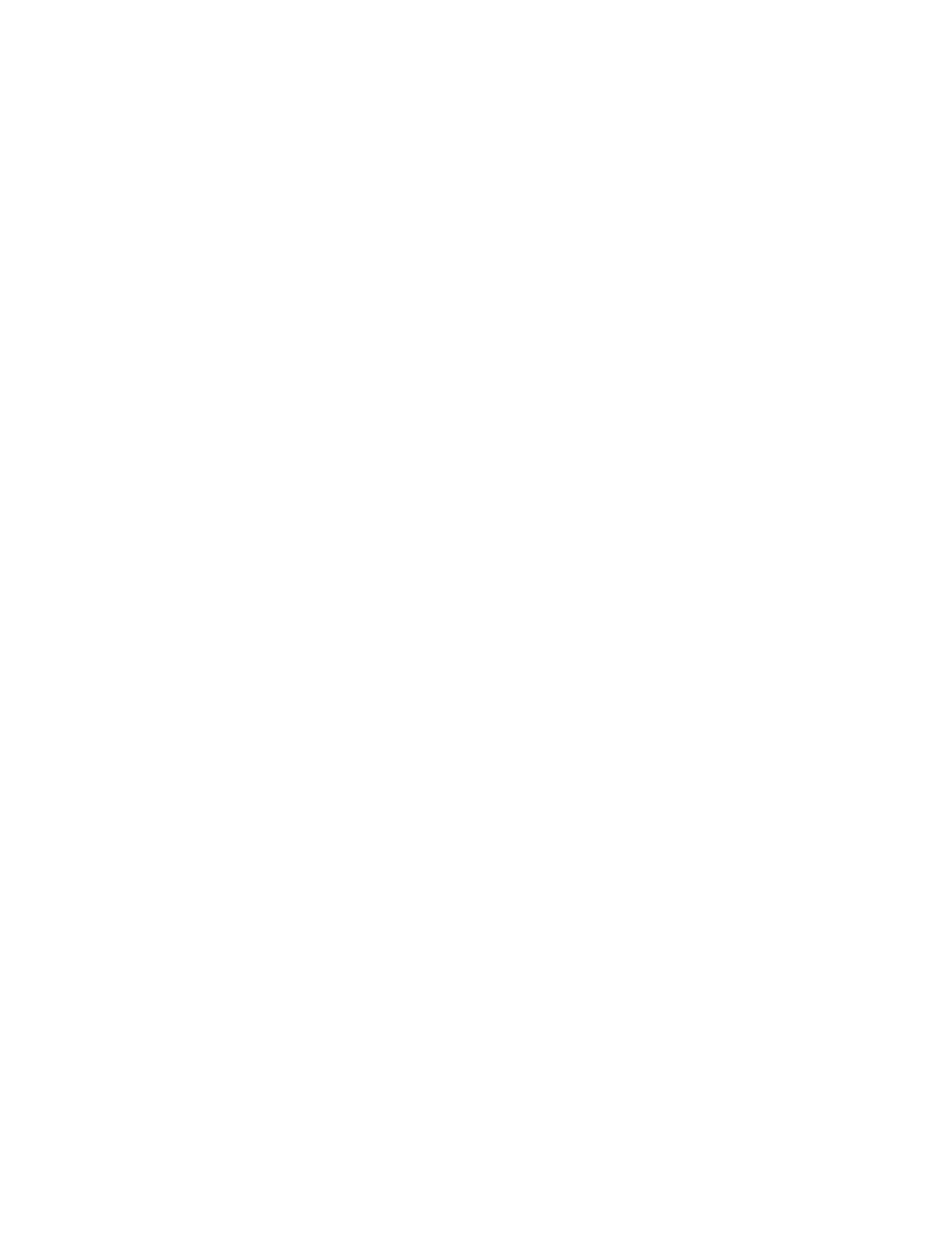
16
This in turn, at any given input speed, produces a certain flow from the pump. This flow is
transferred through high pressure lines to the motor. The ratio of the volume of flow from
the pump to the fixed displacement of the motor will determine the speed of the motor
output shaft.
Speed of the output shaft is controlled by adjusting the displacement flow of the transmis-
sion. Load ( working pressure) is determined by the external conditions (grade, ground
conditions, etc.) and this establishes the demand on the system.
Pump and motor are contained in separate housings. Oil is drawn directly from the reser-
voir into the hydrostatic charge pump. This oil then passes through a 500 psi 5 micron
fiberglass pressure filter. This filter has an internal bypass valve that bypasses fluid to the
reservoir when the filter becomes plugged.
The park brake is integral to the Comer front axle. The brake is activated by an adjustable
hand lever conveniently located to the right of the operators seat.
POWER STEERING SYSTEM
The power steering is fully fluid linked. It consists of a manually operated load sensing
steering control valve and a steering cylinder that is attached to the left and right steering
arms. Fluid pressure is supplied from the load sensing gear pump to the steering control
valve and is directed to the appropriate side of the steering cylinder. The steering control
valve is a non-load reaction design which holds the axle position whenever the operator
releases the steering wheel.
HYDRAULIC SYSTEM
Total system capacity is 25 gallons. Oil leaves the reservoir through two separate suction
lines: one for the hydrostatic drive system and the other supplies the auxiliary hydraulic
pump. The hydrostatic drive system draws fluid from the right reservoir through the 100
mesh suction strainer. The hydraulic transmission offers infinitely variable control of speed
and direction. The operator has complete control of the TLB 6235 with the control foot
pedal for starting and stopping, in forward and reverse motion.
The auxiliary hydraulic circuit draws fluid through a 100 mesh suction strainer. Fluid enters
the accessory pump which is a 8.0 g.p.m. gear type pump.
The circuit delivers fluid to the load-sensing steering control valve . Fluid out of the steering
control valve returns to the reservoir. The remainder of the flow, approximately 8 g.p.m.,
enters the manual control valve which supplies fluid for control of the loader arm cylinders
and loader bucket cylinders. The valve is equipped with a 2500 p.s.i. relief valve. Fluid to
the backhoe is supplied by a power beyond port off the hydraulic control valve for the
loader.
The loader control valve and backhoe control valve, both return through a 5 micron return
filter with a pressure bypass. As in all hydraulic systems, reliability depends upon clean
and cool oil.