Fi g.5 fi g.6, Fi g.3 fi g.4, Fi g.9 – Sealey INVMIG160 User Manual
Page 3: Fig.7 fig.8
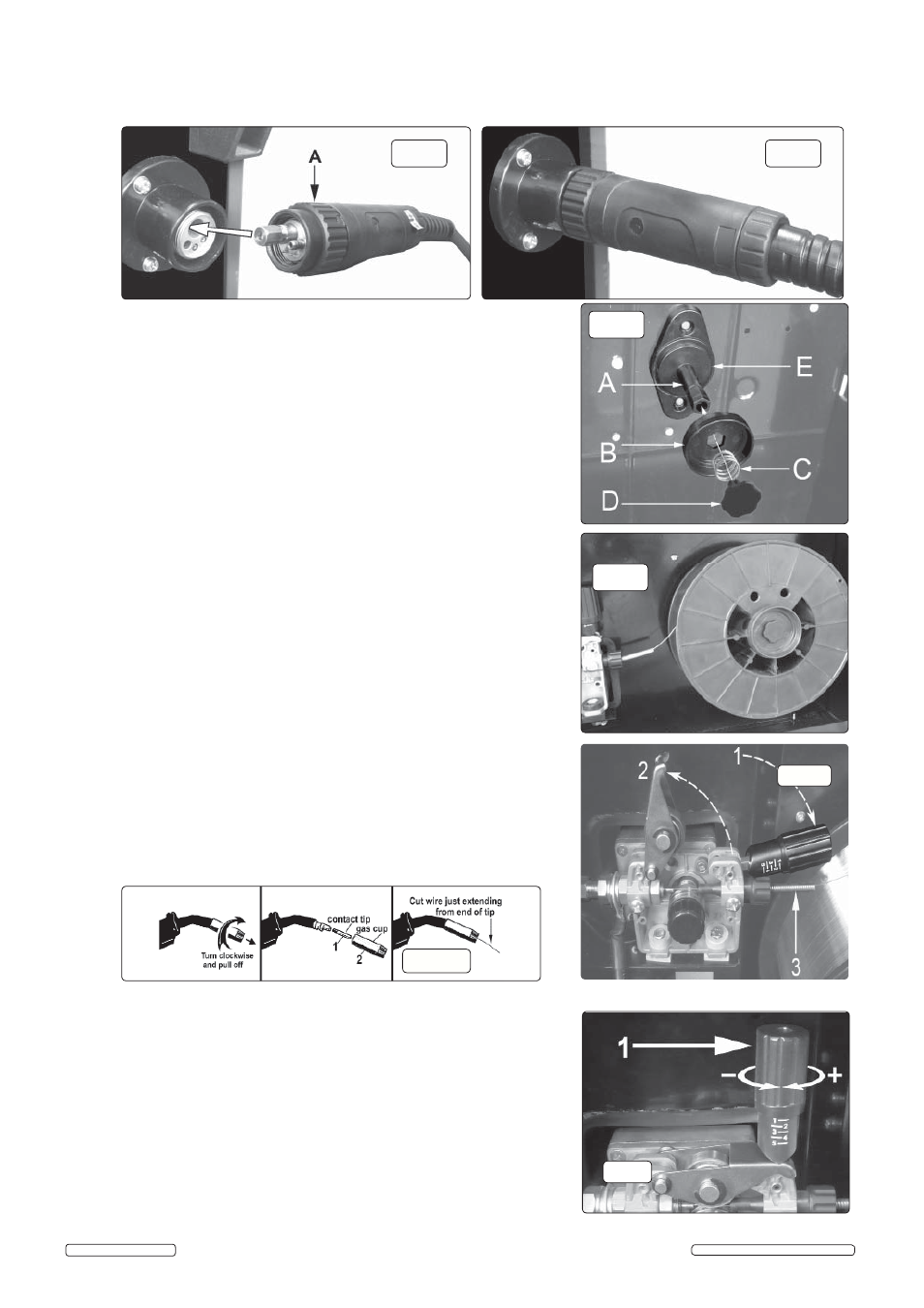
3.4.
FITTING A REEL OF WIRE (FIG.5).
INVMIG160 will accept up to a 5kg reel of
wire. Ensure that the wire diameter used is matched by the correct groove size in
the drive wheel and the correct tip size on the torch as well as the correct torch
liner. Failure to do this could cause the wire to slip and/or bind.
3.4.1.
Remove the retaining knob (D) from the end of the spindle (A) by turning the
knob 90° anticlockwise and pulling it outwards. Remove the spring (C) and the
retaining disc (B) from the end of the spindle also. Slide the reel of wire over the
spindle and hold it against the back plate so that the hole in the reel rests on the
flange (E). Ensure that the wire is coming off the top of the reel in the direction of
the wire drive unit as shown in fig.6.
3.4.2.
Retain hand pressure on the reel to keep it on the flange and slide the retaining
disc (B) over the end of the spindle and into the hole in the reel. Note that the disc
(B) has a hexagonal hole in it which fits onto the hexagonal portion of the spindle.
Keep the disc under hand pressure to retain the reel. Place the spring (C) over
the spigot of the retaining knob (D). Match the indented end of the spigot to the
hole in the end of the spindle. Push the knob spigot into the end of the spindle,
against spring pressure and turn it through 90° to lock it in place.
3.5.
FEEDING WIRE THROUGH TO TORCH.
Open the wire feed mechanism by
pushing the locking/wire tension knob (fig.7.1) down to the right allowing the
pressure roller carrier (fig 7.2) to spring up revealing the feed roller.
Ensure that the required feed groove (0.6 or 0.8) is in line with the wire path. See
Section 3.7. on how to reverse or change the roller.
3.5.1.
Release the wire from the reel and cut off any bent portion ensuring that there are
no burrs left on the end of the wire. Keep the wire under tension at all times to
prevent it uncoiling.
3.5.2.
Straighten about 40-50mm of wire and push it gently through the flexible metal
sheathed cable (fig7.3) and through the 0.6 or 0.8mm feed roller groove and on
into the torch cable liner.
3.5.3.
Push down the pressure roller carrier onto the wire feed roller and hold it down.
Lift up the locking/wire tension knob so that it enters the slot in the pressure
roller carrier and snaps into the indent in its top surface (fig.7). Rotate the tension
knob to a medium setting i.e. between 2 and 3.
3.5.4.
3.5.4.
Remove gas cup (fig.8.2) and contact tip (fig.8.1) from end of torch as follows:
Remove gas cup (fig.8.2) and contact tip (fig.8.1) from end of torch as follows:
a) Take torch in left hand with the torch tip facing to the right.
a) Take torch in left hand with the torch tip facing to the right.
b) Grasp gas cup firmly in your right hand.
b) Grasp gas cup firmly in your right hand.
c) Turn gas cup clockwise only and pull it off end of torch tip.
c) Turn gas cup clockwise only and pull it off end of torch tip.
WARNING!
WARNING!
do not turn gas cup anti-clockwise, as this will damage the
do not turn gas cup anti-clockwise, as this will damage the
internal spring.
internal
spring.
d) Unscrew copper contact tip (right hand thread) to remove.
d) Unscrew copper contact tip (right hand thread) to remove.
fi g.5
fi g.6
fig.7
fig.8
fi g.3
fi g.4
3.3.
CONNECTING THE TORCH CABLE TO THE WELDER.
Align the pins on the Euro connector with the socket on the welder front
panel as shown in fig.3. Push the connector into the socket and rotate the locking ring (A) clockwise so that it draws the plug into the
socket as shown in fig.4.
Note: damage to torches and cables is not covered by warranty.
3.5.5 Check welder is switched off and that the earth clamp is away from the torch
3.5.5 Check welder is switched off and that the earth clamp is away from the torch
tip. Connect the welder to the mains power supply and set the voltage switch
tip. Connect the welder to the mains power supply and set the voltage switch
(fig1.6) to '1'.
(fig1.6) to '1'.
3.5.6 Set the wire speed knob to position (fig1.7) 5 or 6. Keep the torch cable as
3.5.6 Set the wire speed knob to position (fig1.7) 5 or 6. Keep the torch cable as
straight as possible and press the torch switch. The wire will feed through the
straight as possible and press the torch switch. The wire will feed through the
torch.
torch.
3.5.7 a) Take torch in left hand, slide the contact tip over the wire and screw back
3.5.7 a) Take torch in left hand, slide the contact tip over the wire and screw back
into place.
into
place.
b) Grasp gas cup in right hand, push onto torch head and turn clockwise only.
b) Grasp gas cup in right hand, push onto torch head and turn clockwise only.
Do not turn gas cup anti-clockwise, as this will damage the internal spring.
Do not turn gas cup anti-clockwise, as this will damage the internal spring.
c) Cut wire so that it is just protruding from the cup.
c) Cut wire so that it is just protruding from the cup.
3.6
3.6
SETTING WIRE TENSION
SETTING WIRE TENSION
.. Adjust the wire tension by rotating the wire tension
Adjust the wire tension by rotating the wire tension
knob. Turn clockwise to increase the tension and anticlockwise to decrease the
knob. Turn clockwise to increase the tension and anticlockwise to decrease the
tension. See fig 9.1.
tension. See fig 9.1.
IMPORTANT:
IMPORTANT:
Too little or too much tension will cause problematic wire feed
Too little or too much tension will cause problematic wire feed
and result in poor welding.
and result in poor welding.
fi g.9
Original Language Version
© Jack Sealey Limited
INVMIG160 | Issue: 2S - 08/01/15