Notice – Thermo Pride Heat Pump Coil LX-13 User Manual
Page 8
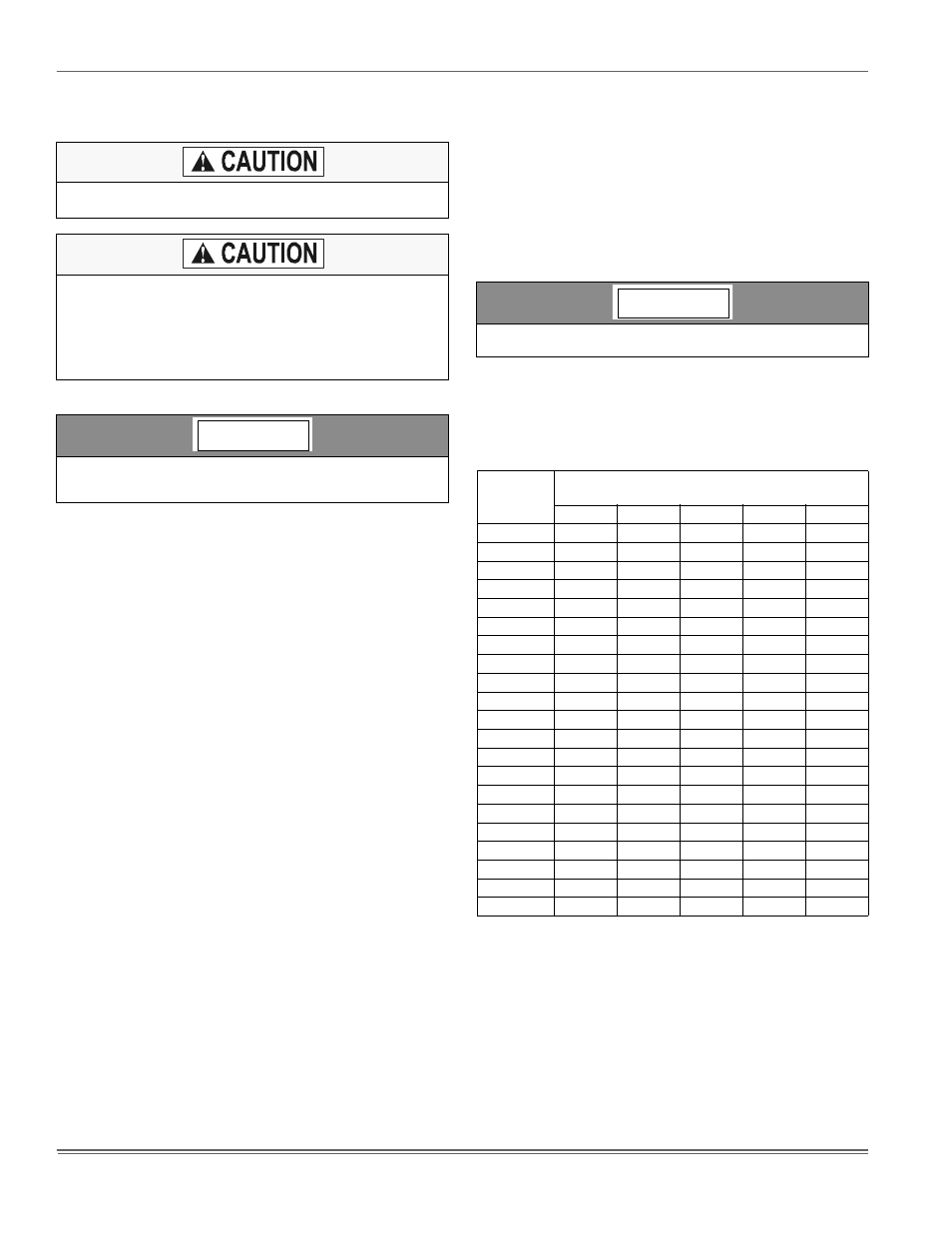
8
SECTION VII: REFRIGERANT LINE
CONNECTION
Connect lines as follows:
1.
Suction and liquid line connections are made outside the cabinet.
Leave the tubing connection panel attached to the cabinet with the
tubes protruding through it. Coil access panel should be removed
for brazing. The lines are expanded to receive the field line set
tubes.
2.
Cut the end of the suction tube using a tube cutter. Place the tube
cutter as close as possible to the end of the tube to allow more
space for the connection and brazing of the suction line.
3.
Remove the heat shield from the Customer Packet, soak in water,
and install over coil tubing to prevent overheating of cabinet.
4.
Wrap a water soaked rag around the coil connection tubes inside
the cabinet to avoid damaging the TXV bulb.
5.
Remove grommets where tubes exit the cabinet to prevent burning
them during brazing.
6.
Purge refrigerant lines with dry nitrogen.
7.
Braze the suction and liquid lines.
8.
Remove the heat shield.
9.
Re-attach the grommets to the lines carefully to prevent air leak-
age.
10. Attach the coil access panel to the cabinet.
Refer to Outdoor unit Installation Manual for evacuation, leak check and
charging instructions.
Lines should be sound isolated by using appropriate hangers or strap-
ping.
All evaporator coil connections are copper-to-copper and should be
brazed with a phosphorous-copper alloy material such as Silfos-5 or
equivalent. DO NOT use soft solder.
SECTION VIII: COIL CLEANING
If the coil needs to be cleaned, it should be washed with Calgon Cal-
Clean (mix one part CalClean to seven parts water). Allow solution to
remain on coil for 30 minutes before rinsing with clean water. Solution
should not be permitted to come in contact with painted surfaces.
SECTION IX: AIR SYSTEM ADJUSTMENT
To check the CFM, measure the static pressure drop across the coil
using a portable manometer and static pressure tips. To prepare coil for
static pressure drop measurements - the system should have been
recently operational in cooling mode.
Drill 2 holes, one 3" after the coil (before any elbows in the ductwork)
and one 3” before the coil. Insert the pressure tips and read the pres-
sure drop from the manometer. See Table 5 to determine the air flow,
and make the necessary adjustments to keep the CFM within the air
flow limitations of the coil.
Coil is under inert gas pressure. Relieve pressure from coil by
removing rubber plug or by depressing schrader core.
Dry nitrogen should always be supplied through the tubing while it
is being brazed, because the temperature required is high enough
to cause oxidation of the copper unless an inert atmosphere is pro-
vided. The flow of dry nitrogen should continue until the joint has
cooled. Always use a pressure regulator and safety valve to insure
that only low pressure dry nitrogen is introduced into the tubing.
Only a small flow is necessary to displace air and prevent oxidation.
Route the refrigerant lines to the coil in a manner that will not
obstruct service access to the coil, air handling system, furnace flue
or filter.
NOTICE
Table 7 below has WET coil data. Run system for approximately 15
minutes in cooling mode prior to taking measurements.
TABLE 6: Air Flow Data - Static Pressure Drop
Coil Size
CFM @ Static Pressure Drop - IWG
(Based on wet coil)
0.10
0.15
0.20
0.25
0.30
18A
400
550
710
880
1000
18B
425
620
830
970
1125
24A
400
600
800
950
1075
24B
425
725
900
1075
1215
30A
425
600
800
950
1075
30B
450
725
900
1075
1215
32A
555
725
865
970
1080
35B
600
800
950
1090
1220
35C
792
1007
1206
1382
1572
36A
625
775
925
1025
1125
37A
689
880
1031
1180
1300
36B
825
976
1174
1300
1450
36C
975
1225
1375
1575
1775
42B
825
1000
1175
1325
1450
42C
1025
1275
1475
1650
1850
43C
785
1025
1210
1400
1570
48C
900
1075
1300
1475
1600
48D
1008
1224
1451
1620
1788
60D
1160
1432
1598
1750
1870
62D
1240
1532
1709
1870
2000
64D
1152
1362
1573
1783
1994
NOTICE