Applied Motion 1030 User Manual
Page 7
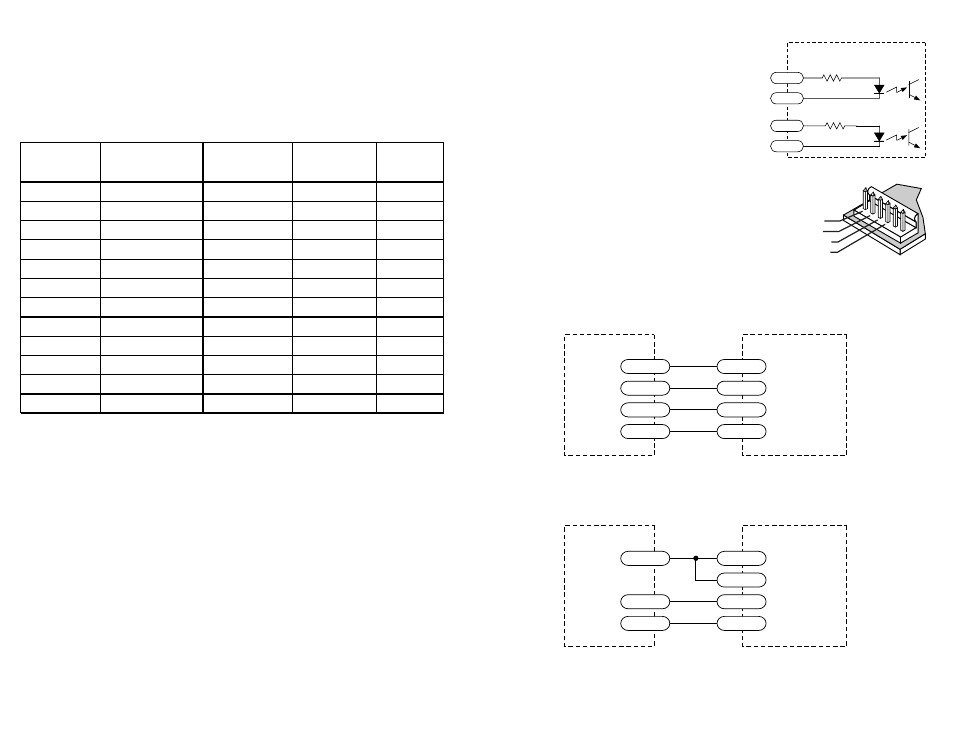
6 - DIR+
5 - DIR-
4 - STEP+
3 - STEP-
-7-
-10-
Motor
Size
Winding
Max Torque
Current
Number
inches
Connection
oz-in
Amps
5014-842
1.38 x 1.38 x 1.57
4 lead
22
1.0
5017-006
1.65 x 1.65 x 1.34
center-end
10
1.0
5017-009
1.65 x 1.65 x 1.54
center-end
17
0.8
5017-013
1.65 x 1.65 x 1.85
center-end
24
0.8
HT17-068
1.65 x 1.65 x 1.30
parallel
22
1.0
HT17-072
1.65 x 1.65 x 1.54
parallel
34
1.0
HT17-076
1.65 x 1.65 x 1.85
parallel
54
1.0
4023-839
2.22 x 2.22 x 1.5
center-end
35
1.0
4023-819
2.22 x 2.22 x 2.0
center-end
56
1.0
HT23-393
2.22 x 2.22 x 1.54
parallel
34
1.0
HT23-396
2.22 x 2.22 x 2.13
parallel
110
1.0
HT23-399
2.22 x 2.22 x 2.99
parallel
140
1.0
Recommended Motors
The following motors from Applied Motion Products are recommended for use with
the 1030. All motors in the list have been tested with the 1030. Dynamic torque data
is available.
Connecting A Pulse Source
The 1030 inputs contain optical isolation circuitry
to prevent the electrical noise inherent in switching
amplifiers from interfering with your circuits.
Optical isolation also allows the 1030 to accept
step and direction signals ranging from 5 to 24
volts. Furthermore, the input signals can be
sourcing (PNP) or sinking (NPN), depending on
whether you "common" the STEP+ & DIR+
terminals (sinking) or the STEP- & DIR- signals
(sourcing). You can also use differential signals.
A schematic diagram of the input circuit is at the
right. The wiring diagrams below show how to
connect the drive to various pulse sources.
inside 1030
STEP+
STEP-
DIR+
DIR-
DIR+
DIR-
1030
Si-100
1030
SI-1
DIR+
DIR-
STEP-
STEP-
STEP+
STEP+
Connecting Applied Motion Si-100
If you are using the Si-100, please purchase the 5V logic version of the 1030
STEP
DIR
STEP-
DIR-
DIR+
+5V
STEP+
Connecting Applied Motion Si-1
If you are using the Si-1, please purchase the 5V logic version of the 1030