Applied Motion 1030 User Manual
Page 8
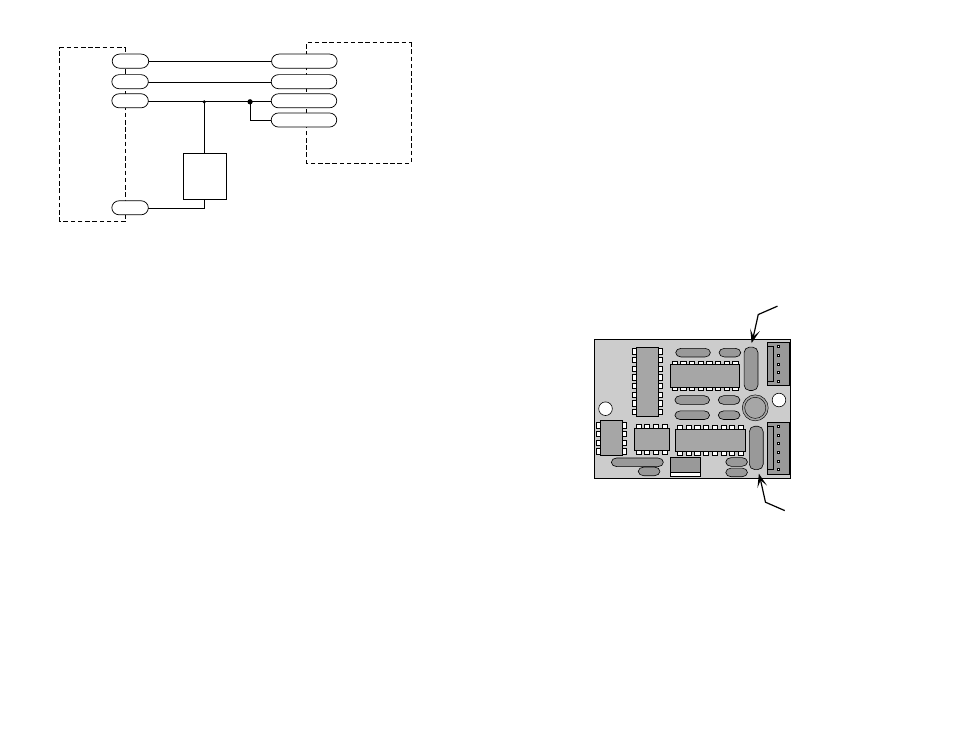
Selecting Between Full, Half and 1/4 Step
-8-
-9-
Idle Current Reduction
The 1030 includes a feature that automatically reduces the motor current to 60%
when the motor is not moving. This is known as idle current reduction.
The idle current reduction is not adjustable by the user. However we can change the
amount of current reduction during the manufacturing process. This is
accomplished by changing the software in the sequencing chips. On sample drives,
these chips are usually socketed, so units can be retrofitted if necessary.
For special options please call the factory.
Setting Phase Current
The phase current is set at the factory when the 1030 is manufactured. The only way
to change it in the field is to change the current sensing resistors.
If you feel that you must change the motor current, please follow these rules:
1. You must be skilled at soldering to change the resistors. You will void your
warranty by modifying the drive, but at least if you are a skillful solderer, the drive
should still work when you're done.
2. Choose the resistor value according to this formula: R = 0.4 / i, where R is the
sensing resistor you need, and i is the current, in amps, that you want.
3. Use a resistors whose value is between 0.39 and 2.0 ohms.
4. Use 1 watt resistors, metal oxide type.
Do not use wirewound resistors.
The 1030 is configured at the factory for full, half or 1/4 step when it is
manufactured. It is normally not possible to change this setting.
However, if your 1030 was an engineering sample, we may have put the step
sequencer chip in a socket.
If this is the case, and you want to try a different step mode, give a us call - we can
probably provide you with a different sequencing chip to put in the socket.
Why would I prefer one mode over another?
Full step mode will give you the most torque at low speeds. Full stepping also
allows you to achieve higher speeds than half stepping if the speed of your pulse
source is limited. For example, to drive a motor at 25 rev/sec in 1/4 step mode, you
must supply step pulses to the 1030 at a rate of 20,000 Hz. To get 25 rev/sec in full
step mode, only 5,000 pulses/sec are required.
Half stepping is smoother and quieter than full step, so you should use half step
mode whenever posssible.
1/4 stepping provides even more precise positioning and smoother motion than half
stepping.
For special options please call the factory.
1030
NAiS FP0 PLC
Connecting Aromat (NAiS) Model FP0 PLC.
The FP0 has sinking outputs.
If you are using a PLC with 24V logic,
please purchase the 24V logic version of the 1030
DIR-
STEP+
+
24VDC
Power
Supply
–
STEP-
Y2
+
–
Y0
DIR+
current sensing resistor
current sensing resistor