Ep - encoder position, Er - encoder ratio, Fc - feed to length with speed change – Applied Motion 1240i User Manual
Page 15: Fd - feed to double sensor
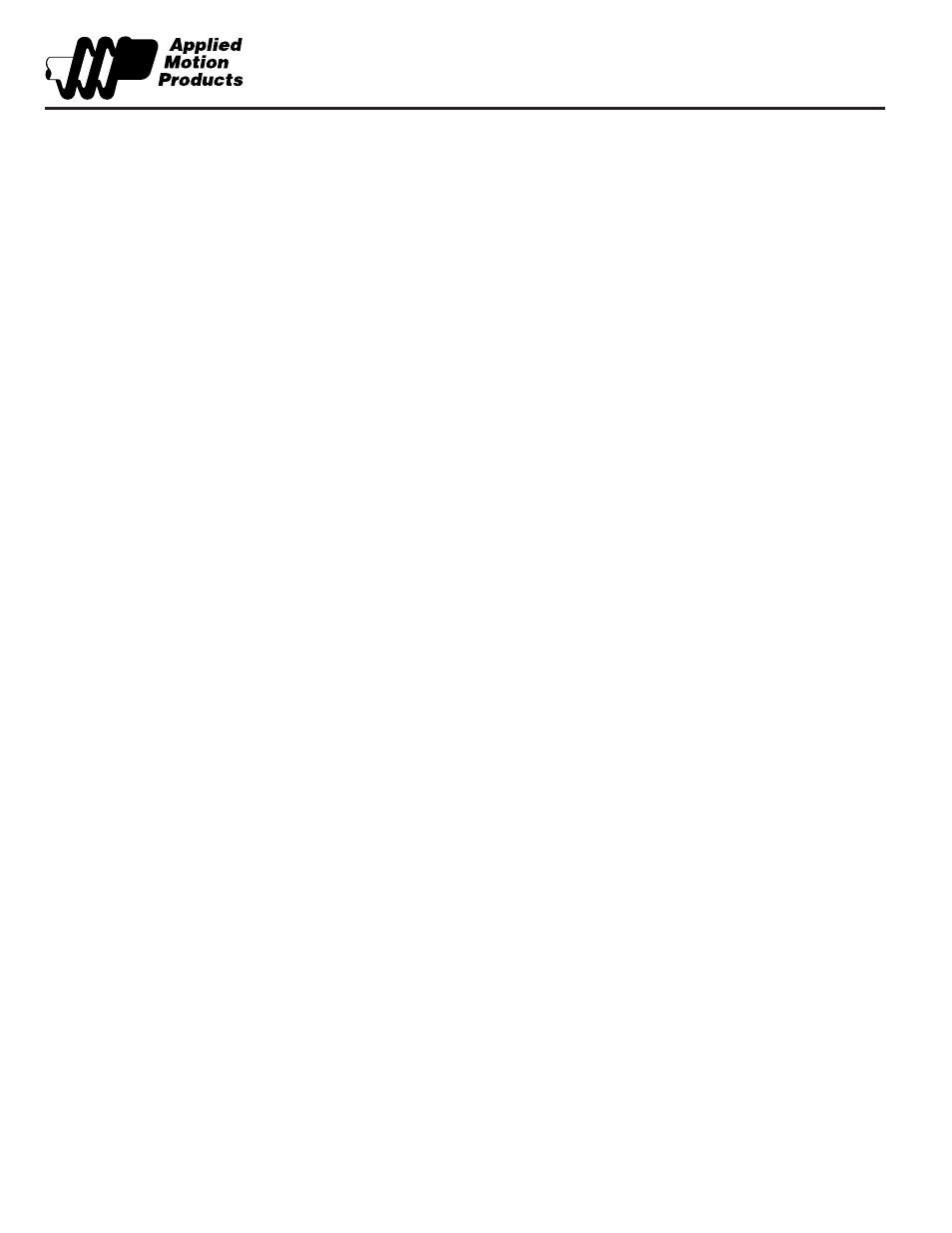
SCL Software Manual
15
920-0010 rev B
9/26/07
motor is not within the dead band, corrective action is taken. For both static position maintenance and
end of move correction, the corrective move length is half the distance to the ideal position. Additional
corrections are made until the encoder position is within the dead band.
Example:
You send
Drive sends
Notes
EF0
nothing
all automatic encoder functions are off (but the encoder
still tracks position and can be read via the EP or IE commands.)
EF1
nothing
Turns on end of move correction
EF2
nothing
Turns on static position maintenance
EF3
nothing
Enables static position maintenance and end of move correction
EP – Encoder Position
On drives supporting encoder feedback, the EP command allows the host to define the present en-
coder position. For example, if the encoder it at 4500 counts, and you would like to refer to this posi-
tion as 0, send “EP0”. Sending EP with no position parameter requests the present encoder position
from the drive.
ER – Encoder Ratio
On drives supporting encoder feedback, the ER command defines the encoder ratio. This number is
the motor resolution, in steps/rev, divided by the encoder resolution, in counts/rev.
For example, if you are using a 4000 count encoder and the motor resolution is set to 20000 steps/rev
(MR8), then you should set ER5. (Because 20000 / 4000 = 5. The motor will take 5 steps per encoder
count.) If your motor resolution is not evenly divisible by the encoder count, try a different motor reso-
lution (using the MR command.) Encoders with binary resolutions, such as 512 and 1024, are unac-
ceptable.
Note: the Si™ drive electronics use “X4” decoding, so a 1000 line encoder such as the U.S. Digital
E2-1000-250-H produces 4000 counts/revolution.
FC – Feed to Length with Speed Change
Executes Feed to Length (relative move) command. Move distance and direction come from the last
DI command. Accel and decel are from AC and DE commands. Initial speed is VE. After the motor
had moved DC steps, the speed is reduced to VC.
DC must not be greater than VE, and DC must
not exceed DI.
Example: You’re drilling holes. You want to rapidly approach the workpiece, then slow down for drill-
ing. Total move distance is 50000 steps, but after 45000 steps, you want to reduce the speed from 8
rev/sec to 0.5 rev/sec.
You send
Notes
VE8
initial speed is 8 rev/sec
VC0.5
change speed is 0.5 rev/sec
DI50000
total move distance is 50,000 steps
DC45000
change distance is 45,000 steps
FC
launch move
FD - Feed to Double Sensor
Accelerates the motor at rate AC to speed VE. When the first sensor “trips”, the motor decelerates (at
rate DE) to speed VC. When the second sensor is reached, the motor decelerates to a stop at rate DE.
The sign of the DI register is used to determine the direction.