7 hydraulic, mechanical and electrical duty, 8 pumps for food use or potable water – Flowserve ME User Manual
Page 25
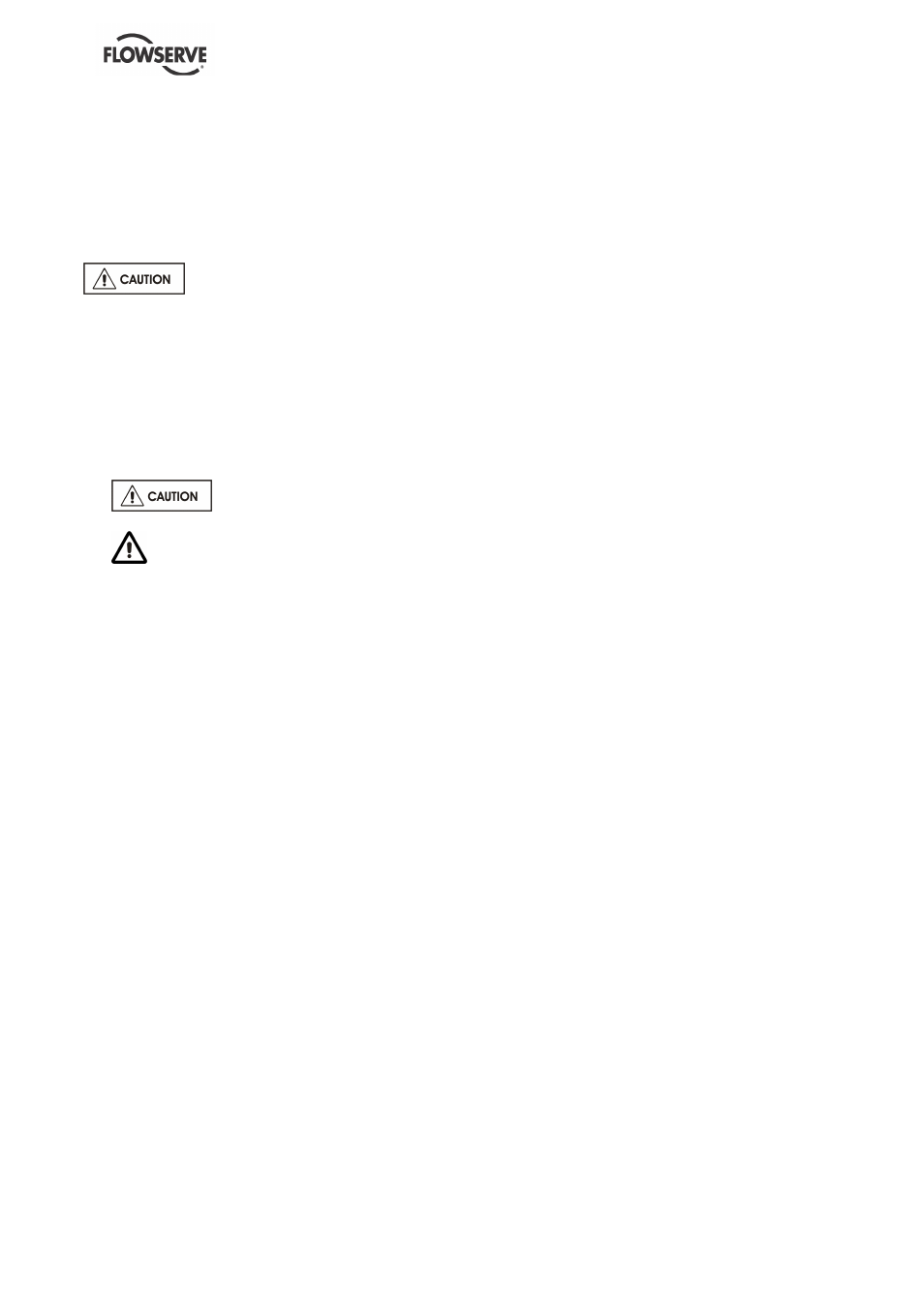
ME USER INSTRUCTIONS ENGLISH 71576287 - 02/13
Page 25 of 36
flowserve.com
f) Keep the pump fully filled with water. In case of
pumped liquid other than water, drain the pump
entirely.
g) Turn once per week the pump shaft of one or
two turns.
h) Never restart the pump without carrying out the
verifications recommended before starting (see
§ 5.4.1).
When ambient temperatures are
likely to drop below freezing point, the pump and any
cooling and flushing arrangements must be drained
or otherwise protected.
5.6.4 Restarting in continuous running
a) Ensure that the pump is completely full of liquid.
b) Ensure a continuous supply with a sufficient
available NPSH.
c) Ensure a backpressure so that the motor power
is not in excess.
d)
Respect the starting frequency
imposed by the motor manufacturer.
e)
Protect the pump against water hammer
when stopping or starting.
5.7 Hydraulic, mechanical and electrical
duty
This product has been supplied to meet the
performance specifications of your purchase order,
however it is understood that during the life of the
product these may change.
The following notes may help the user decide how to
evaluate the implications of any change. If in doubt
contact your nearest Flowserve office.
5.7.1 Specific gravity (SG)
Pump capacity and total head in meters (feet) do not
change with SG, however pressure displayed on a
pressure gauge is directly proportional to SG. Power
absorbed is also directly proportional to SG.
It is therefore important to check that any change in
SG will not overload the pump driver or over-
pressurize the pump.
5.7.2 Viscosity
For a given flow rate the total head reduces with
increased viscosity and increases with reduced
viscosity. Also for a given flow rate the power
absorbed increases with increased viscosity, and
reduces with reduced viscosity. It is important that
checks are made with your nearest Flowserve office
if changes in viscosity are planned.
5.7.3 Pump speed
Changing pump speed effects flow, total head,
power absorbed, NPSH
R
, noise and vibration. Flow
varies in direct proportion to pump speed, head
varies as speed ratio squared and power varies as
speed ratio cubed.
The new duty, however, will also be dependent on
the system curve. If increasing the speed, it is
important therefore to ensure the maximum pump
working pressure is not exceeded, the driver is not
overloaded, NPSH
A
> NPSH
R
, and that noise and
vibration are within local requirements and
regulations.
5.7.4 Net positive suction head (NPSH
A
)
NPSH available (NPSH
A
) is the head available at the
impeller inlet, above the vapor pressure of the
pumped liquid.
NPSH required (NPSH
R
) is the minimum head required
at the impeller inlet, above the vapor pressure of the
pumped liquid, to avoid excessive cavitation and
extreme performance degradation.
It is important that NPSH
A
> NPSH
R
. The margin
between NPSH
A
> NPSH
R
should be as large as
possible.
If any change in NPSH
A
is proposed, ensure these
margins are not significantly eroded. Refer to the
pump performance curve to determine exact
requirements particularly if flow has changed. If in
doubt please consult your nearest Flowserve office
for advice and details of the minimum allowable
margin for your application.
5.7.5 Pumped flow
Flow must not fall outside the minimum and
maximum continuous safe flow shown on the pump
performance curve and or data sheet.
5.8 Pumps for Food Use or Potable
Water
If the pump has not been specifically ordered for a
food or drinking water application it must not be
used for these types of applications. If it has been
ordered for this type of application the following
recommendations are to be followed.
5.8.1 Cleaning prior to operation
Pumps that are to be used for a food or drinking
water application should be cleaned before being
put into initial operation and after the installation of
spare parts that are in contact with the liquid.
Cleaning once the pump has been commissioned
will depend on the application and operating
conditions. The user must ensure that the cleaning
procedures are suitable for the application and
operating conditions, and local regulations.