Flowserve ME User Manual
Page 27
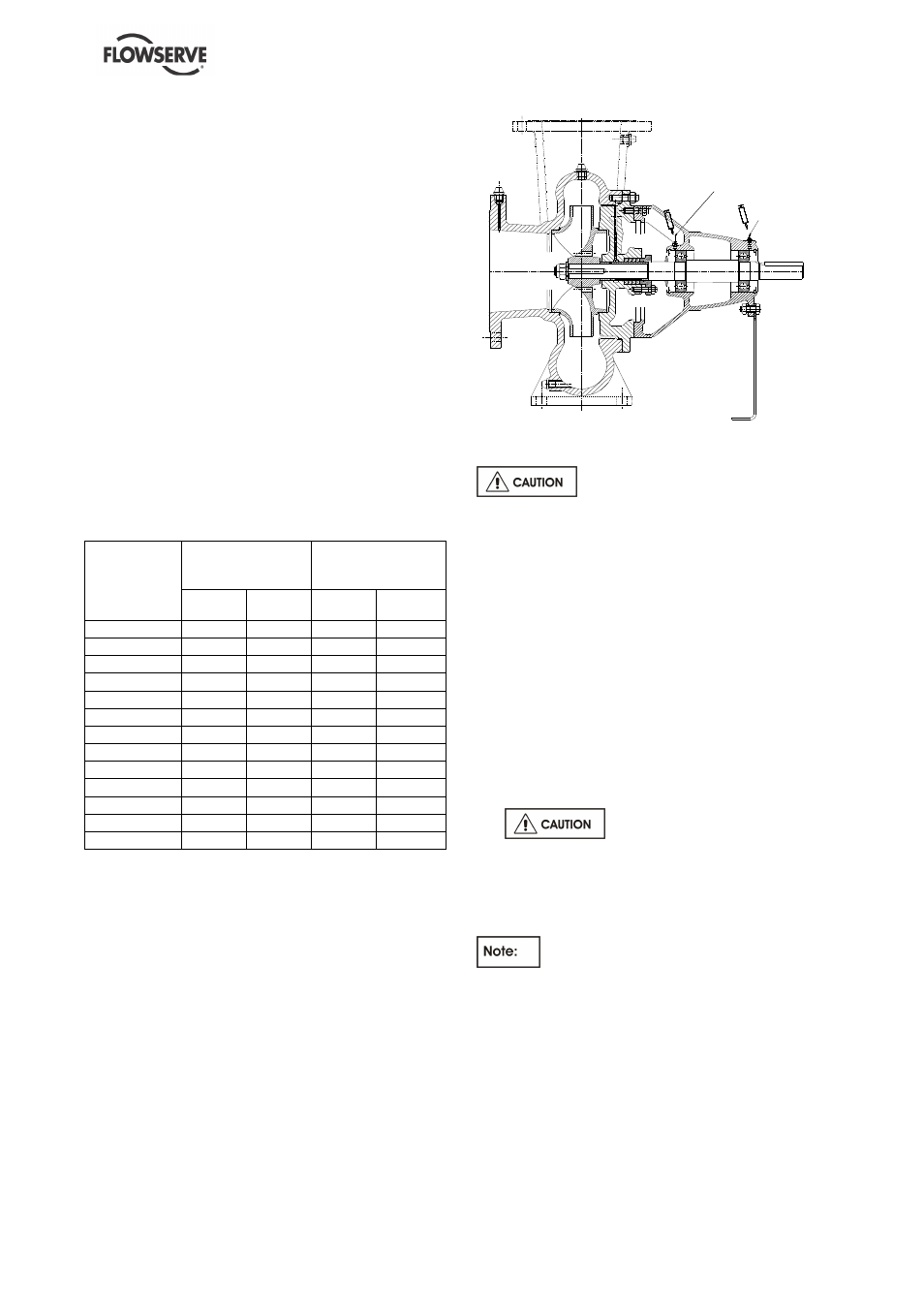
ME USER INSTRUCTIONS ENGLISH 71576287 - 02/13
Page 27 of 36
flowserve.com
If any problems are found the following sequence of
actions should take place:
a) Refer to section 7, Faults; causes and remedies,
for fault diagnosis.
b) Ensure equipment complies with the
recommendations in this manual.
c) Contact Flowserve if the problem persists.
6.2.1 Standard maintenance
Roller bearing
6.2.1.1 For ME 150-200, 200-250, 200-315, 200-
355, 250-250, 250-315, 300-300
The bearing housings are provided with sealed for
life ball bearings. No maintenance is required.
6.2.1.2 For other ME
The bearings fitted are prepacked with grease at the
factory. When the regressing period is reached it is
necessary to remove as much of the old grease as
possible with a clean lint free cloth and repack the
bearings with fresh grease.
Pump type
Lubrication in
hours frequency *of
operation
Added quantity in
cm
3
(oz)
Coupling
side
Pump
side
Coupling
side
Pump
side
ME 150 - 500
4 000
4 000
30 (1.01)
30 (1.01)
ME 200 - 400
8 000
8 000
25 (0.85)
25 (0.85)
ME 200 - 500
4 000
4 000
30 (1.01)
30 (1.01)
ME 250 - 355
8 000
8 000
25 (0.85)
25 (0.85)
ME 250 - 400
8 000
8 000
25 (0.85)
25 (0.85)
ME 250 - 500
4 000
4 000
30 (1.01)
30 (1.01)
ME 300 - 400
8 000
8 000
25 (0.85)
25 (0.85)
ME 300 - 450
4 000
4 000
30 (1.01)
30 (1.01)
ME 300 - 500
3 500
3 500
50 (1.69)
50 (1.69)
ME 350 - 350
4 000
4 000
40 (1.35)
40 (1.35)
ME 400 - 500
3 500
3 500
50 (1.69)
50 (1.69)
ME 400 - 650
3 500
3 500
50 (1.69)
50 (1.69)
ME 500 - 500
3 500
3 500
50 (1.69)
50 (1.69)
* At least once a year
The grease used in factory for first filling is:
SHELL ALVANIA R2
Its equivalents: MOBIL: Mobilux EP 2,
TOTAL: Multis 2,
ELF : ELF MULTI
Grease
nipple
Grease
nipple
6.2.2 Routine inspection (daily/weekly)
The following checks should be made
and the appropriate action taken to remedy any
deviations:
a) Check operating behavior. Ensure noise,
vibration and bearing temperatures are normal.
b) Check that there are no abnormal fluid or
lubricant leaks (static and dynamic seals) and
that any sealant systems (if fitted) are full and
operating normally.
c) Pump fitted with a stuffing box: leakage of 20
drops per minute.
d) Pump fitted with a mechanical seal: no leakage.
e) Check the level and condition of oil lubricant. On
grease lubricated pumps, check running hours
since last recharge of grease or complete
grease change.
6.2.3 Periodic inspection (six monthly)
a)
Check foundation bolts for
security of attachment and corrosion.
b) Check pump-running records for hourly usage to
determine if bearing lubricant requires changing.
c) The coupling should be checked for correct
alignment and worn driving elements.
If a check shows a bad running of the
motor pump unit, the user must:
a)
Refer to the "fault finding chart" chapter 7
of this leaflet to apply the recommended
solutions.
b) Ensure that your equipment corresponds to the
arrangements of this leaflet.
c) Contact Flowserve after-sales Department if the
problem persists.