Flowserve WPG IDP User Manual
Page 14
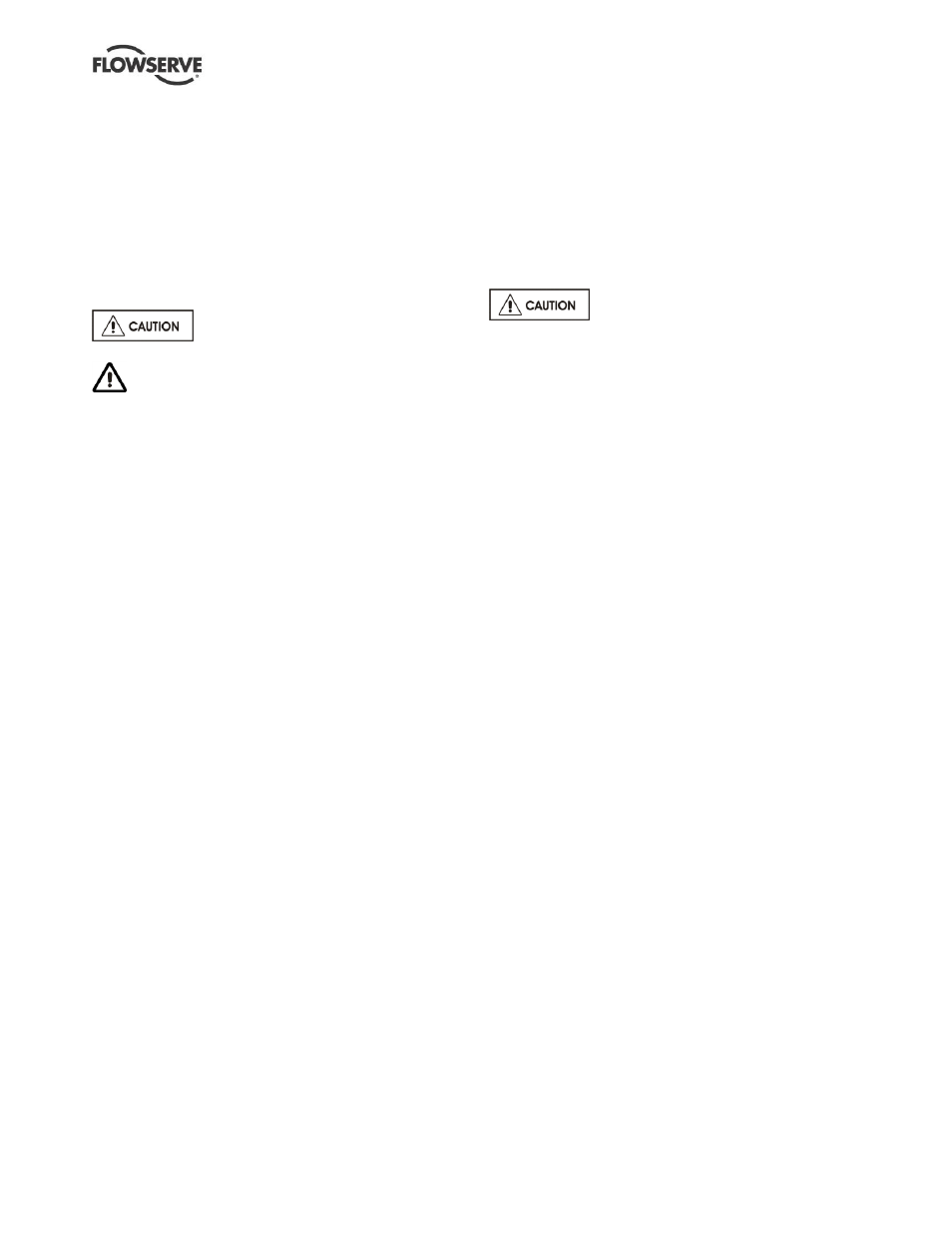
WPG and WPH USER INSTRUCTIONS ENGLISH 26999969 10-12
Page 14 of 40
flowserve.com
Maximum forces and moments allowed on the pump
flanges vary with the pump size and type. To minimize
these forces and moments that may, if excessive, cause
misalignment, hot bearings, worn couplings, vibration
and the possible failure of the pump casing, the
following points should be strictly followed:
Prevent excessive external pipe load
Never draw piping into place by applying force to
pump flange connections
Do not mount expansion joints so that their force,
due to internal pressure, acts on the pump flange
Ensure piping and fittings are flushed
before use.
Ensure piping for hazardous liquids is arranged
to allow pump flushing before removal of the pump.
Take into account the available NPSH which must be
higher than the required NPSH of the pump.
4.6.2 Suction piping
a) The inlet pipe should be one or two sizes larger
than the pump inlet bore and pipe bends should
be as large a radius as possible.
b)
On suction lift the piping should be inclined up
towards the pump inlet with eccentric reducers
incorporated to prevent air locks.
c)
On positive suction, the inlet piping must have a
constant fall towards the pump.
d) The pipe next to the pump should be the same
diameter as the pump suction and have a
minimum of two pipe diameters of straight section
between the elbow and the pump inlet flange.
Where the NPSH margin is not large, it is
recommended that the pipe straight is 5 to 10
pipe diameter. (See section 10.3, Reference 1.)
Inlet strainers, when used, should have a net 'free
area' of at least three times the inlet pipe area.
e)
Fitting isolation and non-return valves will allow
easier maintenance.
f)
Never throttle pump on suction side and never
place a valve directly on the pump inlet nozzle.
4.6.3 Discharge piping
a) A non-return valve should be located in the
discharge pipework to protect the pump from
excessive back pressure and hence reverse
rotation when the unit is stopped.
b) Fitting an isolation valve will allow easier
maintenance.
4.6.4 Flange loads
The permissible flange loading is dependent on a
number of factors such as dimensions, flange rating,
pressure, temperature, material, pump configuration etc.
The recommendations contained in the section on
pipework connections should be followed to eliminate
these loads.
When requested the permissible flange loading will
have been supplied separately to the purchaser and
should be obtained and retained with this manual. If in
doubt contact Flowserve for information.
4.6.5 Auxiliary piping
The connections that are to be piped
up will have been fitted with protective metal or
plastic plugs which will need to be removed.
4.6.5.1 Pumps fitted with packed glands
a)
When suction pressure is below ambient pressure
and differential head is less than 10 m, it may be
necessary to feed gland packing with liquid to
provide lubrication and prevent the ingress of air.
b)
When pumping “dirty” liquids a clean liquid supply
to the gland is recommended.
4.6.5.2 Pumps fitted with mechanical seals
a)
Single seals requiring re-circulation will normally
be provided with the auxiliary piping from pump
casing already fitted.
b)
Seal housings/covers having an auxiliary quench
connection require connection to a suitable source
of liquid flow, low pressure steam or static
pressure from a header tank. Recommended
pressure is 0.35 bar (5 psi) or less.
c)
Double seals require a barrier liquid between the
seals, compatible with the pumped liquid.
d)
With back-to-back double seals, the barrier liquid
should be at a minimum pressure of 1 bar above
the maximum pressure on the pump side of the
inner seal. The barrier liquid pressure must not
exceed limitations of the seal on the atmospheric
side. For toxic service the barrier liquid supply and
discharge must be in a safe area.
e)
Special seals may require modification to auxiliary
piping described above. Consult Flowserve if
unsure of correct method or arrangement.
f)
For pumping hot liquids, to avoid seal damage, it is
recommended that any external flush/cooling
supply be continued after stopping the pump.
4.6.5.3 Pumps fitted with heating/cooling jackets
Connect the heating/cooling pipes from the site supply.
The top connection should be used as the outlet to
ensure complete filling/venting of the annulus.