Flowserve Chemstar standard User Manual
Page 14
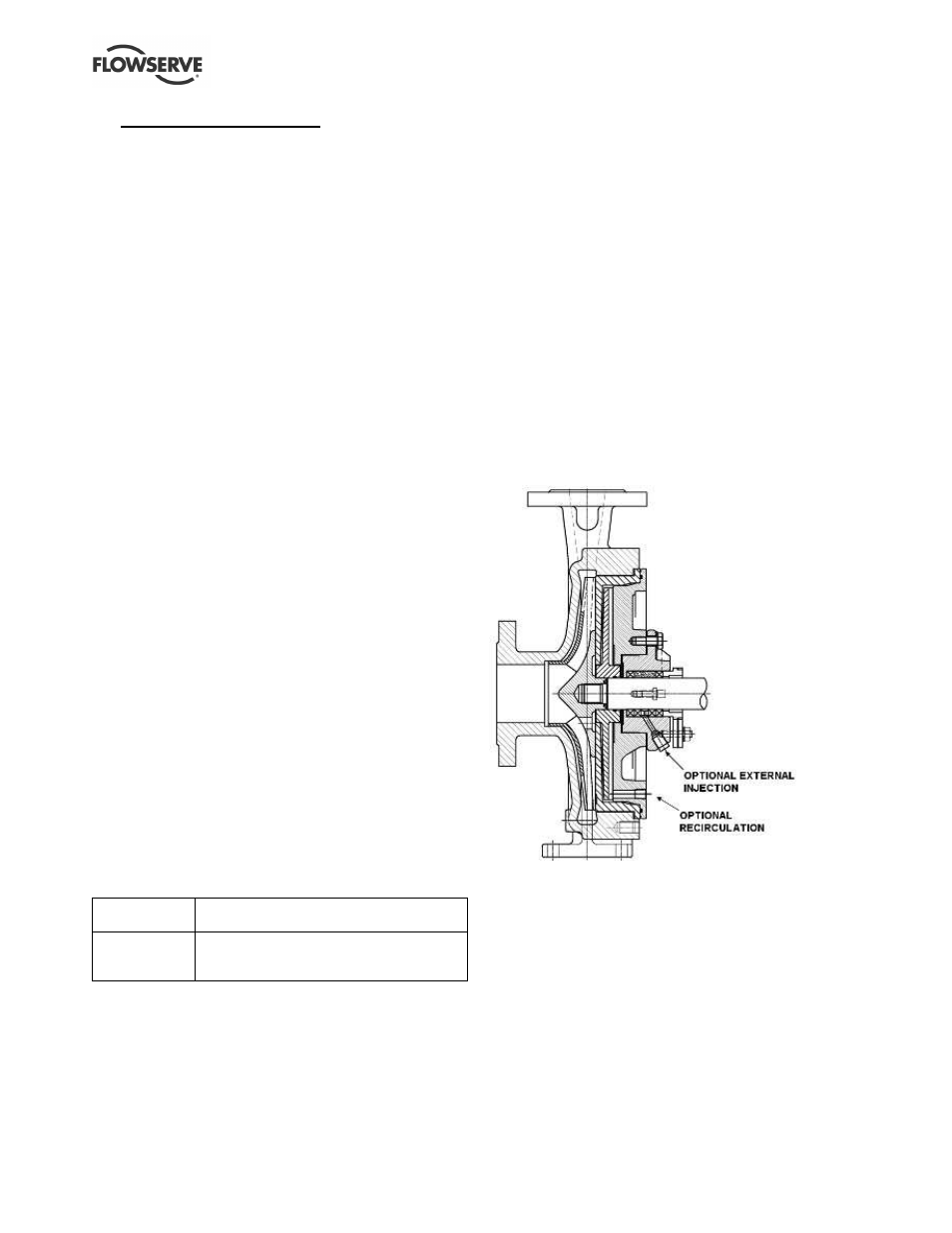
CHEMSTAR USER INSTRUCTIONS ENGLISH 71569185 02-10
Page 14 of 44
flowserve.com
Chemstar repeller pump only
In Chemstar pumps fitted with a repeller and with
dry running gland packing as secondary sealing
the packing is factory installed.
In some applications to limit the gland packing
fouling, Chemstar repeller pumps could possibly
have a 0.25 to 0.5 m³/h external clean compatible
liquid flush injected into the stuffing box at 5 to 10 m
head above ambient pressure prior to start up and
prior to shut down.
4.6.4.2 Pumps fitted with mechanical seals
The Seal Sentry design of the anti-vortex single
internal rear cover provides excellent liquid circulation
around the seal and will not normally require a
separate flush.
Single seals requiring flush by re-circulation of pumped
liquid will normally be provided with the auxiliary piping
from pump casing already fitted. (Where an external
compatible flush is specified, the piping to the pump is
the responsibility of the pump installer.)
Rear covers with an auxiliary quench connection
require connection to a suitable source of liquid, low
pressure steam or static pressure from a header tank.
Recommended pressure is 0.35 bar (5 psi) or less.
Double seals require a barrier liquid between the
seals, compatible with the pumped liquid.
With back-to-back double seals, the barrier liquid should
be at a minimum pressure of 1 bar (15 psi) above the
maximum pressure on the pump side of the inner seal
and at least 1 bar (15 psi) above ambient external
pressure. The barrier liquid pressure must not exceed
limitations of the seal on the atmospheric side.
For toxic service the barrier liquid supply and
discharge must be handled safely and in line with
local legislation.
Seal chamber pressure:
Mechanical
seal
Use seal manufacturer's limits or ask seal
manufacturer to verify seal pressure
Gland
packing
Maximum stuffing box pressure =
5 bar (3 500 r/min), 7 bar (2 900 r/min)
and 10 bar (1 450 and 1 750 r/min)
Special seals may require different auxiliary piping to
that described above. Consult separate User
Instructions and/or Flowserve if unsure of correct
method or arrangement.
For pumping hot liquids, to avoid seal damage, it is
recommended that any external flush/cooling supply
be continued after stopping the pump.
4.6.4.3 External recirculation and flush for
pumps fitted with repeller
Only dry running single mechanical seals or packing
arrangement approved by Flowserve must be used.
(Refer to section 8.3.) In some applications, to keep
seal faces clean, pumps could possibly have a 0.25
to 0.5 m
3
/h external clean compatible liquid flush
injected into the seal cavity at 5 to 10 m head above
atmospheric pressure prior to start up and prior to
shut down. The Chemstar repeller chamber can
have an auxiliary recirculation connection back to the
suction side pipe.
Customers should always seek instructions from
Flowserve if the pump is not supplied with the
optional recirculation line or external flush and if it is
planned to install these later.
4.6.4.4 Pumps fitted with heating/cooling jackets
Connect the heating/cooling pipes from the site
supply. The top connection should be used as the
outlet to ensure complete filling/venting of the jacket
unless the heating medium is steam, when the
bottom connection should be used as the outlet.
4.6.5 Final checks
Check the tightness of all bolts in the suction and
discharge pipework. Check also the tightness of all
foundation bolts.