Flowserve ISC User Manual
Page 4
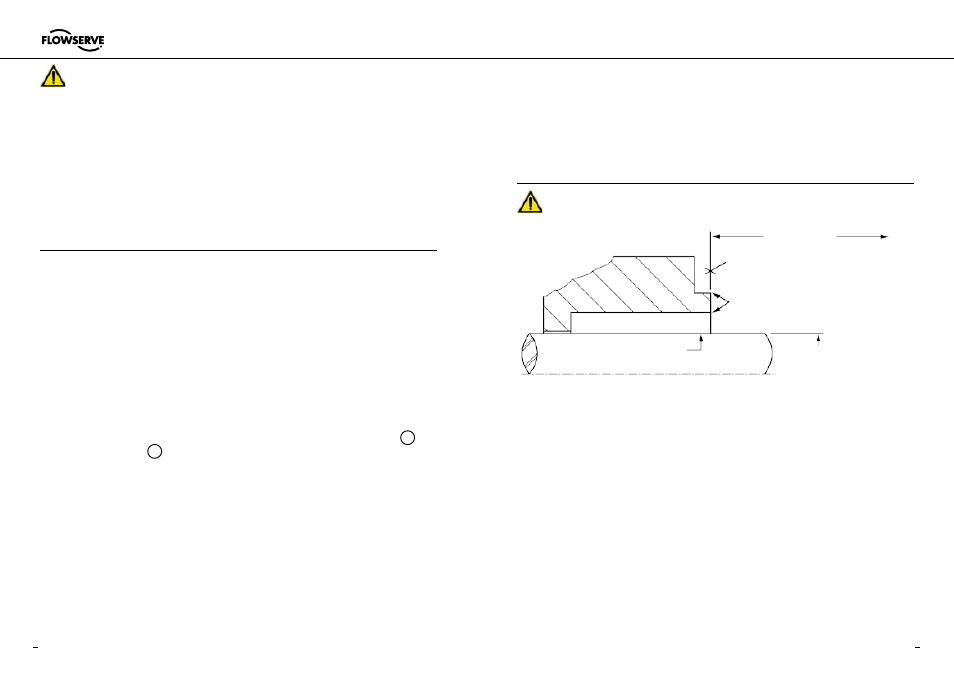
6
7
ISC Innovative Standard Cartridge Seal - Installation Instructions for Machinery Components
!
If the machine is to be preserved with integrated mechanical seal(s) the preserving
medium must not impair the functions of the mechanical seal(s) by e.g. fouling of
the seal faces, hardening, or swelling the secondary seals.
After a storage period of years the mechanical seal must be inspected for its “as new”
properties. This applies in particular to the seal faces and secondary sealing elements. An
inspection by Flowserve becomes necessary.
The mechanical seal can in principle be transported with suitable means like lifting
accessories.
5. Equipment Check
5.1 Follow plant safety regulations prior to equipment disassembly:
• lock out motor and valves
• wear designated personal safety equipment
• relieve any pressure in the system
• consult plant MSDS files for hazardous material regulations
5.2 Disassemble equipment in accordance with equipment manufacturer’s instruc-
tions to allow access to seal installation area.
5.3 Remove existing mechanical seal and gland or compression packing and packing
gland.
5.4 Make sure the shaft or sleeve and the seal housing face are clean and free of burrs,
cuts, dents, or corrosion that might cause leakage past the sleeve packing 11
or gland gasket G . Replace worn shaft or sleeve. Remove sharp edges from
keyways and threads.
5.5 Check equipment dimensions to ensure that they are within the dimensions
shown in Figures 1 and 2. Critical dimensions include:
• Box Bore (ØC)
• Box Depth (G)
• Distance to First Obstruction (K)
• Pump Frame accomodates Gland OD (ØE)
5.6 Check gland bolting to ensure that bolt diameter and bolt circle conform to the
dimensions shown in Figure .
5.7 Handle the ISC with care, it is manufactured to precise tolerances.
The sealing faces of the ISC seal are the Primary Ring and the Mating Ring.
They are lapped flat to within three light bands (0.9 µm).
Keep the seal faces perfectly clean at all times.
Seal Chamber Requirements
The mechanical seal may be installed when there are no visible signs of damage
to the mechanical seal. This applies in particular to the seats, centrings, and the
statically sealing 0 rings.
!
!
!
!
If the pump condition exceeds the above criteria (including consideration for thermal
growth), consult Flowserve Application Engineering for recommendations to avoid seal
performance compromises.
to first obstruction
Face of seal housing to be square to the axis of the
shaft to within 0.00 inch (0.08 mm) FIM and have
√6-µ Inch (1.6 µm) Ra finish or better.
Gland pilot can be either of these register locations.
Concentric to within 0.005 inch (0.1 mm) FIM of
shaft or sleeve OD
Shaft or sleeve finish to be
µ inch (0.8 µm) Ra or better
Shaft or sleeve OD
+0,000 inch (+ 0,000 mm)
-0,00 inch (- 0,050 mm) ANSI
+0,000 inch (+0,000 mm) API 610
-0,001 inch (-0,05 mm) DIN / ISO
• Bearings must be in good condition.
• Maximum lateral or axial movement of shaft (end play) = 0.010 inch (0.5 mm) FIM
• Maximum shaft runout at face of seal housing = 0.00 inch (0.05 mm) FIM
• Maximum dynamic shaft deflection at seal housing = 0.00 inch (0.05 mm) FIM
Seal housing bore to have
√15 µ inch
(. µm) Ra or better
!
Figure 1