Flowserve ISC User Manual
Page 9
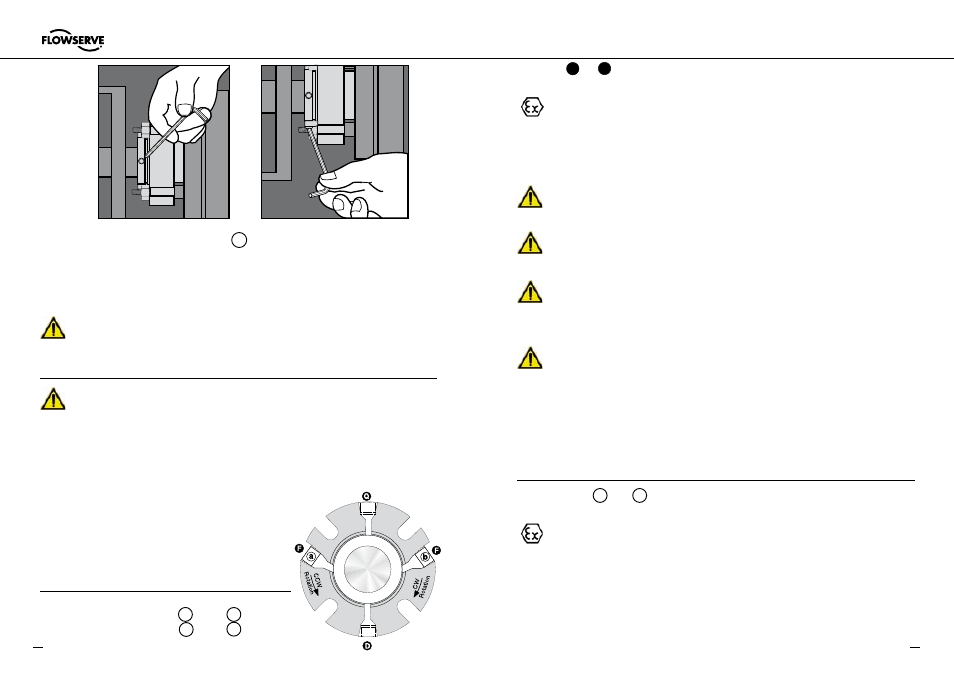
16
17
ISC Innovative Standard Cartridge Seal - Installation Instructions for Machinery Components
7.3 Taps and in the gland are quench and drain ports used for fluid quenching,
ASME Flush Plan 76. If they are not used, they should be plugged with pipe plugs.
Escaping leakage must not form an explosive mixture.
7.4 Remove lock outs on pump and valves.
7.5 Do not start up the equipment dry to check motor rotation, etc. Open valves to flood
pump with product fluid. Ensure that the seal flush system is operating. Vent air from
the casing of the pump and the seal chamber before start-up.
It must be ensured that the machine is protected against penetration by dust and /
or that dust deposits are removed at regular intervals so that they cannot exceed a
thickness of 5 mm on the surfaces of the faces.
It must be ensured, e.g. in the form of a level monitor, that the sealing chamber is
completely vented and filled with fluid in all running states if it is to minimise the
heat generated by friction and therefore the surface temperature of the seal elements.
If the application limits for running in accordance with these instructions cannot
be observed, the temperature of the supply liquid and / or the installed components
must be monitored at all times by a device that shuts down the machine once a
critical temperature is reached. This device can consist of resistance thermometers
or thermoelements.
The seal chamber must be vented carefully before startup.
7.6 Observe the start-up. If the seal runs hot or squeals, check the seal flush system. Do
not allow the equipment to run for any extended time if the seal gets hot or squeals.
8. Dual Seal Piping and Functional Recommendations
8.1 Flush taps a and b in the gland are barrier fluid inlet and outlet ports. Use
Figure 8 to determine which ports to use as inlet and outlet.
Forced ventilation of the seal chamber must be ensured when the circulation pipe is
connected. Should there be gas or air pockets in the sealing chamber, these can ac-
cumulate with the rotation at the outer diameter of the seal gap at machine start-up.
This causes the machine to run dry at the seal gap for an indefinite period, and the
seal faces can become damaged.
Figure 6
Figure 5
Figure 7
Q
D
6.9 Caution: Remove the centering tabs CT from the sleeve collar.
See Figure 6. Save the tabs and fasteners for future use when the pump impeller is
reset or when the seal is removed for repairs.
6.10 Turn the shaft by hand to ensure unobstructed operation.
6.11 See Operational Recommendations before start-up.
Conduct a static pressure test. Do not exceed the max. pressures.
7. Single Seal Piping and Functional Recommendations
7.1 Install an adequate seal flush system. Ensure that piping is connected to the
correct pipe ports to prevent unsafe situations. The connections on the me-
chanical seal are properly marked.
The ISC requires a clean cool environment for maximum seal life. With a clean cool
product, use a bypass flush from the pump discharge (API plan 11) or a bypass
flush to the pump suction (API plan 1). With clean hot products use a bypass flush
through a cooler (API plan 1). With abrasive products or products that are in-
compatible with the seal, use a flush from a clean
external source (API plan ).
7.2 Use flush port that coincides with gland markings
and direction of equipment rotation. Plug extra NPT
opposite of flush (see Figure 7).
Shaft rotation from exposed end of gland
Inlet
Plugged Port
Clockwise (CW)
Port b Port a
Counterclockwise (CCW) Port a Port b