Flowserve ISC User Manual
Page 8
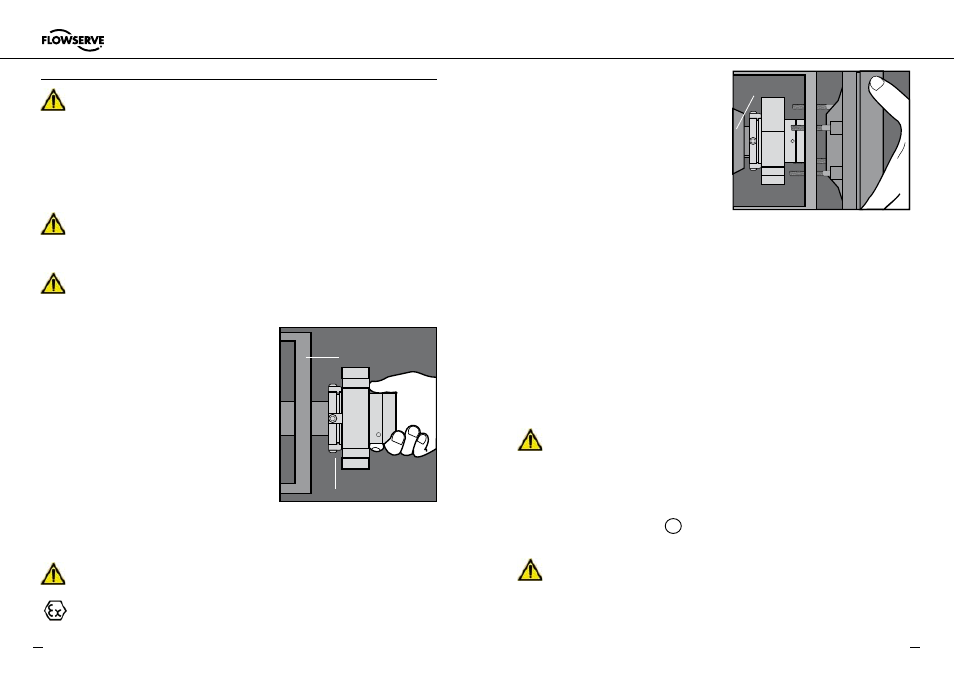
14
15
ISC Innovative Standard Cartridge Seal - Installation Instructions for Machinery Components
6. ISC Installation- Single Seal Design
The installation chamber for the mechanical seal must be checked against the
corresponding drawing and table of dimensions. It must be ensured that all dimensi-
ons, surface qualities, and tolerances (e.g. concentricity, run-out, fits) are observed.
The specifications under e.g. ISO 1049 or API 68, DIN 8161, FLOWSERVE
publication FSD 101, FLOWSERVE publication FSD17 must be observed.
NOTE: No seal setting measurements are needed to install the seal.
Instructions are for vertically split case end-suction ANSI pumps.
Modification of the procedure may be required for other style pumps. Consult Flowserve.
Take care that seal cartridge or components of the seal are handled and carried
safely during installation of mechanical seal and that the ergonomic principles
are followed. In order to prevent personal injuries the operator should also wear
protective clothing as per the plant’s safety regulations.
Precautions must be taken for parts of the mechanical seal that will be used as
support to step on during assembly operations. These parts must be protected
against slipping, stumbling or falling (for example by using a strut).
6.1 Tools needed for installation:
* An open end wrench for the gland bolt nuts
* 1/8" (imperial sizes) or mm (metric sizes).
Allen wrench (provided)
* /16" (imperial sizes) or 5 mm (metric
sizes). Allen wrench (provided) for sizes
>.500" (65 mm)
6.2 Lubricate the shaft or sleeve lightly with
silicone lubricant unless otherwise specified.
6.3 Tighten the Centering Tab screws
6.4 Install the complete ISC cartridge assembly
onto the shaft or sleeve with the centering tabs
near the bearing housing. See Figure .
For some pumps it may be required to remove the bearing frame before installing the
cartridge seal.
Vibrations must be prevented from transferring to the installed ISC during operation,
e.g. through structural measures implemented on the machine.
The machine to take the ISC must be earthed in accordance with the applicable regu-
lations for electrical installations (e.g. VDE rules) to conduct away any electrostatic
build-up and so prevent spark formation.
Bearing Frame
Setting Device
Figure 3
6.5 Install the pump back plate (seal
chamber) and bolt it in place on the
bearing frame.
See Figure 4.
If removed re-install the bearing frame
first.
6.6 Position the ISC with the gland tight against the seal chamber face. If equipment
conditions allow, position gland with the outlet port or plugged flush port as close
to the 1:00 position as possible.
See Sections and 4 for further piping considerations. Otherwise turn the gland so
that the vent tap is as close to the 1:00 o’clock position as possible and so that the
flush piping will clear the bearing frame.
Caution: Centering Tabs should not be removed or loosened before tightening the
gland bolts and tightening the set screws to the shaft.
Tighten the gland nuts evenly in a diagonal sequence.
Do not over tighten the gland nuts, as this can warp parts and cause leakage. The
suggested ISC minimum torque values are as follows:
Shaft sizes 1.000” – 1.97” 5 – 48 mm:
20 Nm
Shaft sizes .000” – .750” 50 – 70 mm:
27 Nm
Components provided by the customer for installing the mechanical seal, e.g. the
pump cover or fastening screws, must exhibit adequate properties and dimen-
sions. It must not be possible to overstress these components, e.g. the max
permitted tightening torque must not be exceeded.
6.7 Assemble the pump. Avoid pipe strain. Align coupling properly.
6.8 With the impeller, shaft, coupling, and bearings in their final operating positions,
tighten the ISC set screws 13 .
See Figure 5.
Inaccurate tightening of these screws can lead to unsafe situation as mechanical
seal may move out of the seal chamber when pressure is applied.
Suggested minimum torque values for set screws are as follows:
Shaft sizes 1.000” – .500” 5 – 65 mm:
4.5 Nm
Shaft sizes .65” – .750”
70 mm:
13.5 Nm
Bearing Frame
Pump
Back
Plate
Figure 4
!