Flowserve P-200 Durametallic User Manual
Page 4
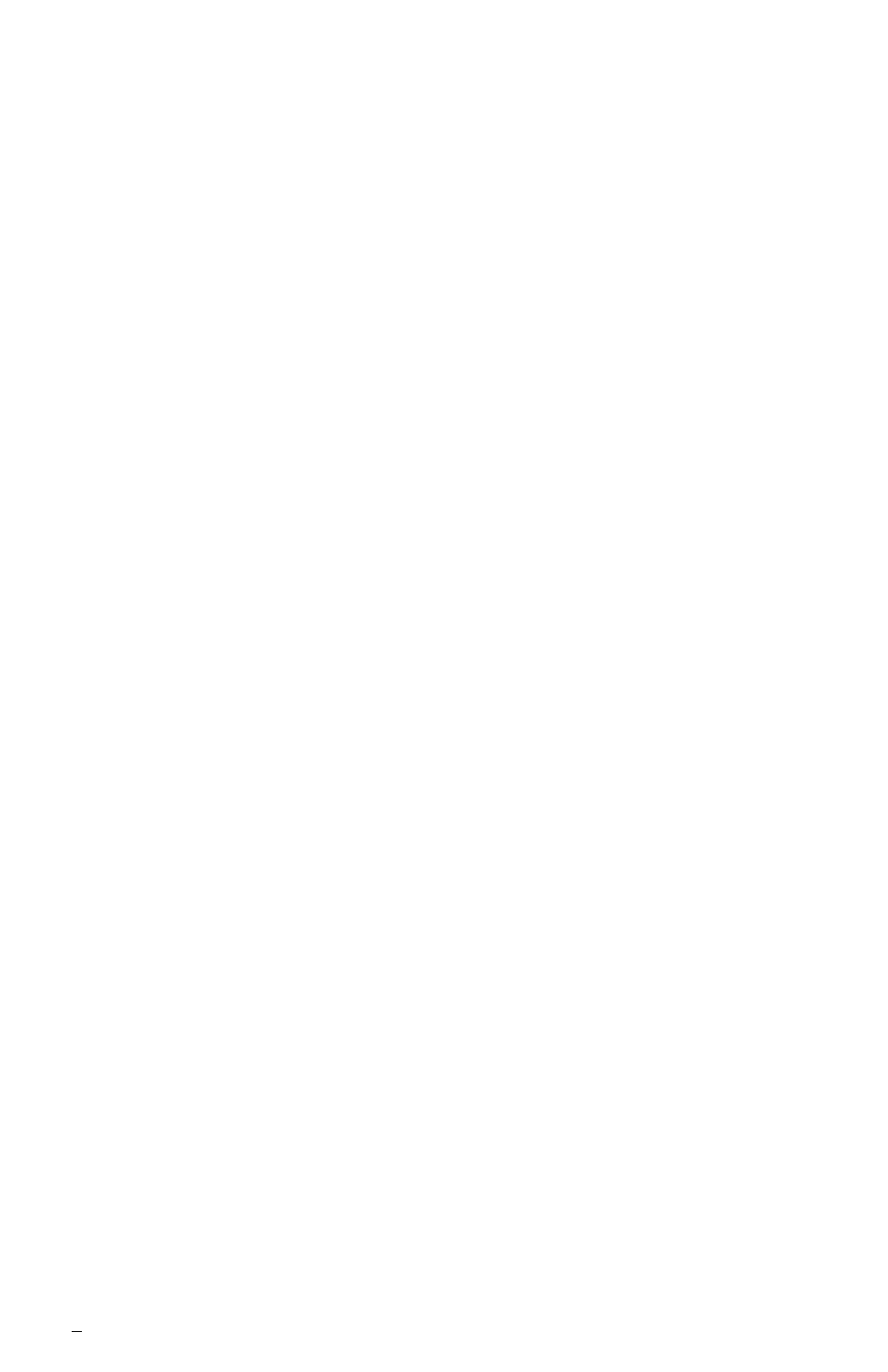
1.2 Disassemble equipment in accordance with equipment manufac-
turer’s instructions to allow access to seal installation area.
1.3 Remove existing mechanical seal and gland or compression
packing and packing gland (follower flange).
1.4 Make sure the shaft or sleeve is free of burrs, cuts, dents or
corrosion that might cause leakage past the sleeve gasket, as
shown on the assembly drawing. Replace worn shaft or sleeve.
Remove sharp edges from keyways and threads.
1.5 Make sure the seal housing face is clean and free of burrs, cuts,
dents or corrosion that might cause leakage at the gland gasket or
misalign the seal gland.
1.6 Check equipment dimensions to ensure they are within the
dimensions shown in Figures 1 and 2. Critical dimensions include
shaft or sleeve OD (A), chamber depth (C), minimum and maxi-
mum seal housing bore (B), and the minimum distance to the first
obstruction (E) plus 3.175 mm (0.125 inch).
1.7 Check gland bolting to ensure that bolt diameter (H) and bolt
circle (J) conform to the dimensions shown in Figure 2.
1.8 Handle the P-200 seal with care, it is manufactured to precise
tolerances. The sealing faces of the rotating face and stationary
face are of special importance. They are lapped flat to within three
light bands (34.8 millionths of an inch). Keep the seal faces
perfectly clean at all times.
4